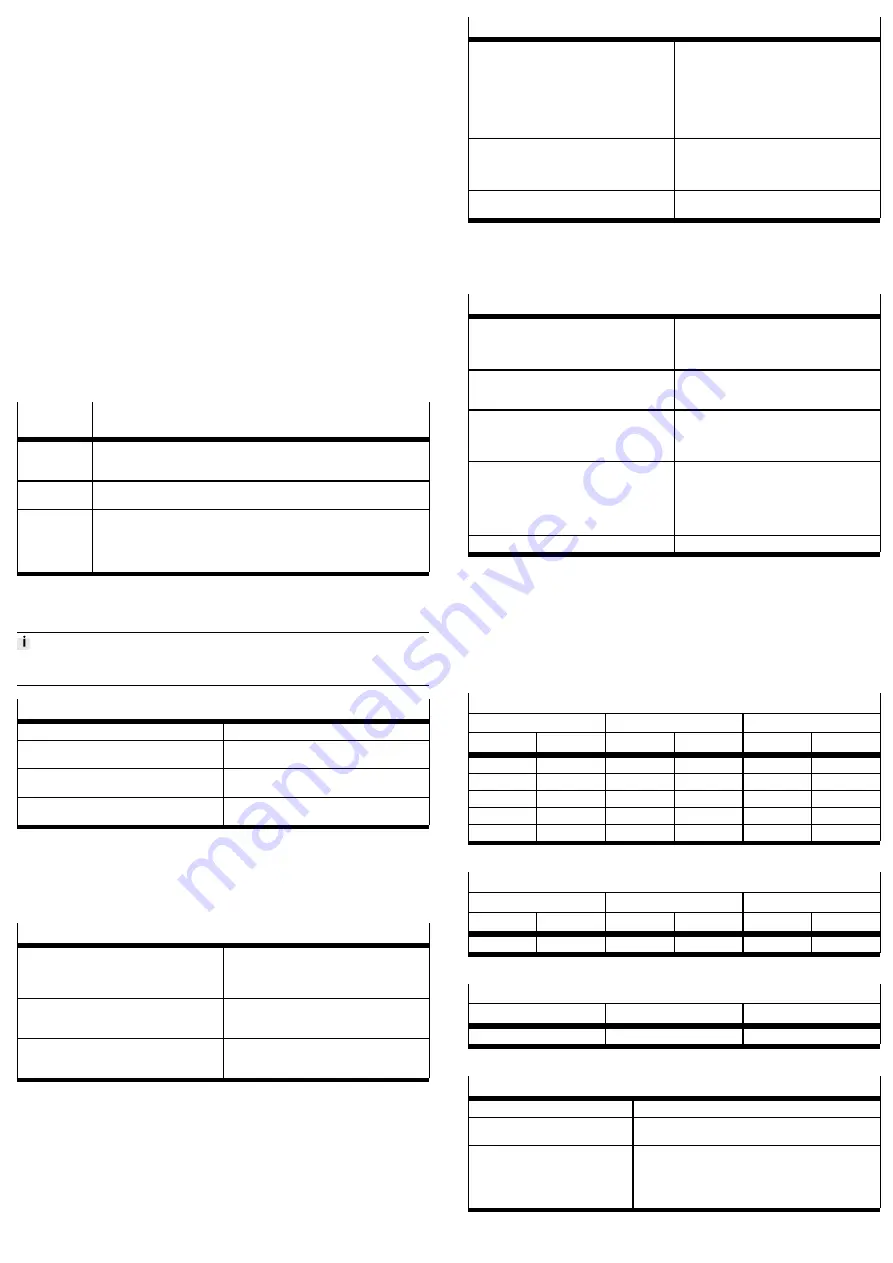
1. Connect the bus node with LAN.
2. Install and start the FFT on a Personal Computer.
3. If the device search does not start independently:
Call up the FFT function "Search for devices".
Devices available in the LAN are displayed.
4. If the PC is not in the same LAN sub-network
è
Online help or description of
"FFT".
5. Select the bus node CTEU-VN.
6. In the network settings or via the command line mode, enter a static address
and subnet mask.
7. Switch bus node off and back on.
The IP address is assigned.
8. Call up the FFT function "Search for devices" again.
Devices available in the LAN are displayed.
9. Select the bus node CTEU-VN.
Then carry out the Firmware update
è
Online help or description of "FFT".
8.4
Processing the Firmware update
è
Online help or description of "FFT"
9
Maintenance
Check the bus node regularly for Firmware updates. No further action.
10
Accessories
è
11
Glossary
Term/abbre-
viation
Meaning
LASALClass file
The LASAL Class file (configuration file, also known as "LASAL component") is
available in the "Product Catalogue" of the controller software "LASAL CLASS"
and contains all configuration data for communication with the bus node.
PLC
Programmable logic controller, also referred to as system controller or controller
for short (“Programmable Logic Controller”, PLC)
VARAN
Versatile Automation Random Access Network: network protocol based on Ether-
net technology in automation technology for the data exchange between a
higher-order control system (industry PC, PLC or I/O controller), network parti-
cipants and field devices/modules, e.g. valve terminals or drives
è
www.varan-bus.net
Tab. 12
12
Technical data
Technical data for the connected products can be obtained from the product doc-
umentation.
Electrical characteristics
Degree of protection through housing
IP65/IP67
1)2)
Protection against electric shock (protection
against direct and indirect contact)
Through the use of SELV circuits
Disconnection of network connections for oper-
ating voltage power supply U
EL/SEN
Electrically isolated, by means of transformer
(up to 500 V)
CE marking
3)
(see declaration of conformity)
è
In accordance with EU EMC Directive
1) Requirement: bus node mounted completely, plug connector in the plugged-in status or provided with cov-
er cap.
2) Connected products may only fulfil a lower degree of protection.
3) The product is suitable for industrial purposes only (Class A). Measures for interference suppression may
be required in residential areas (Class B).
Tab. 13
General mechanical characteristics
Vibration and shock resistance (to IEC 60068)
1)
–
Vibration (part 2-6)
–
Shock (part 2 – 27)
–
Continuous shock (part 2 – 27)
Severity level (SG)
1)
For wall or H-rail mounting
–
Wall: SG2; H-rail: SG1
–
Wall: SG2; H-rail: SG1
–
Wall and H-rail: SG1
Temperature range
2)
–
Storage/transport
–
Operation
–20 … +70 °C
–5 … +50 °C
Corrosion protection
The product is intended for indoor use in a typic-
al industrial atmosphere.
–
Avoid condensation.
General mechanical characteristics
Materials
–
Housing
–
Cover
–
Fibre-optic cables
–
Threaded bush M12
–
Threaded bush M3
–
Seals
–
Screws
RoHS-compliant
PA-reinforced
PA
PC
Nickel-plated brass
Brass
NBR
Galvanised steel
Dimensions
–
Width
–
Length
–
Height
40 mm
91 mm
39.7 mm
3)
Weight (bus node without cables and sub-
assembly)
98 g
1) Explanation of the severity level
è
Table "Explanation on vibration and shock – severity level"
2) Connected products may only cover a less extensive temperature range.
3) Height of the product: without guide pin, without cover cap
Tab. 14
Power supply
Operating voltage for bus node and connected
products
1)
–
Nominal value
–
Tolerance range
24 V DC
18 … 30 V DC
2)
Load voltage for bus nodes and connected
products
1)
–
Tolerance range
18 … 30 V DC
2)
Intrinsic current consumption at nominal operat-
ing voltage 24 V DC
Operating voltage supply for the electron-
ics/sensors (U
EL/SEN
)
typ. 65 mA
(internal electronics)
Power rating of operating and load voltage
power supplies
1)3)
–
Bus node on the connected product (e.g.
valve terminal)
–
Bus node on the decentralised electrical
sub-base CAPC
max. 4 A
max. 2 A
per I-Port Device
4)
Power failure buffering
10 ms
1) Separate, external fuses are required for the operating and load voltage power supplies (no bus node-
internal overload and reverse polarity protection for the products connected via X1 and X2).
2) The tolerance range is dependent on the connected products.
3) Total power rating of operating and load voltage power supplies PS and PL (residual current), maximum
permitted current consumption of bus node and connected products
4) Total power rating of operating and load voltage power supplies PS and PL (residual current), maximum
permitted current consumption per I-Port device
Tab. 15
Explanation of vibration and shock – severity level
Vibration load
Frequency range [Hz]
Acceleration [m/s
2
]
Deflection [mm]
SG1
SG2
SG1
SG2
SG1
SG2
2 … 8
2 … 8
–
–
±3.5
±3.5
8 … 27
8 … 27
10
10
–
–
27 … 58
27 … 60
–
–
±0.15
±0.35
58 … 160
60 … 160
20
50
–
–
160 … 200
160 … 200
10
10
–
–
Tab. 16
Shock load
Acceleration [m/s
2
]
Duration [ms]
Shocks per direction
SG1
SG2
SG1
SG2
SG1
SG2
±150
±300
11
11
5
5
Tab. 17
Continuous shock load
Acceleration [m/s
2
]
Duration [ms]
Shocks per direction
±150
6
1000
Tab. 18
Network-specific characteristics
Network protocol
VARAN-BUS
Network-specific functions and gener-
al protocols
–
Cyclic data exchange
–
Real-time data transmission (RT)
System-specific functions
–
Integrated VARAN splitter
–
System status via image table
–
Firmware update
–
Identification of network participants (electronic rat-
ing plate)