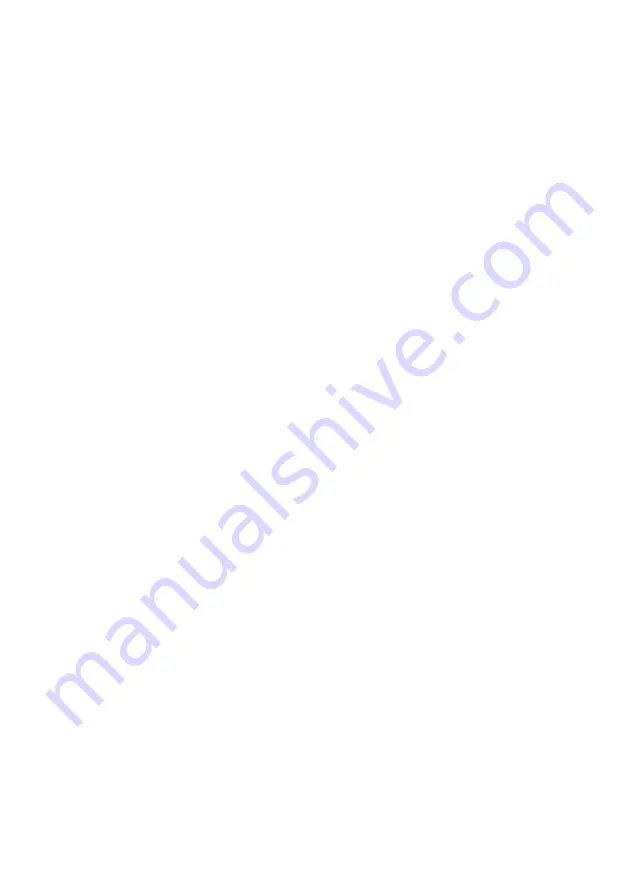
Festo — CMMT-ST-C8-1C-...-S0 — 2021-04b
Installation
15
–
A PELV fixed power supply must be used for the safety relay unit and the logic power supply of the
CMMT-ST. The GND (0 V) of the two fixed power supplies must also be connected to each another.
The device power supply and the power supply of the STO inputs must refer to the same GND
potential.
–
The wiring between the safety relay unit and the I/O interface of the servo drive must be installed
to ensure that the risk of a short circuit between the conductors or to 24 V, as well as a cross circuit
can be eliminated
è
EN 61800-5-2, Annex D.3.1. Otherwise, the safety relay unit must feature
detection of shorts across contacts and, in the event of a fault, must switch off the control signals
on 2 channels.
–
Only use suitable mating plugs and connecting cables
è
Manual Assembly, Installation. Use wire
end sleeves for multicore wires.
–
Avoid conductive contamination between neighbouring plug pins.
–
Make sure that no bridges or similar can be inserted parallel to the safety wiring. For example, use
the maximum wire cross section or appropriate plastic wire end sleeves.
–
To cross-wire safety-related inputs, use twin wire end sleeves. When cross-wiring STA diagnostic
contacts, a maximum of 10 devices may be cross-wired
è
Manual Assembly, Installation.
–
The safety relay unit and its inputs and outputs must meet the necessary safety classification of the
safety function required for the specific case.
–
Connect each of the control inputs to the safety relay unit on 2 channels.
–
If the STA feedback signal of the STO safety sub-function has to be evaluated: connect diagnostic
contact directly to the safety relay unit. The diagnostic contacts must not be connected in parallel,
since a device like this with an active safety sub-function would report a safe state for all devices.
–
Whether the diagnostic contact needs to be evaluated depends on the type of motor that is
connected and the desired safety classification.
–
If diagnostic contacts are cross-wired for a device compound: wire diagnostic contacts in series.
Basic circuitry concept
–
Safe sensors – e.g. emergency stop switches, light curtains – are routed to the safety relay unit (or
the safety PLC).
–
The safety relay unit requests the safety sub-function on the servo drive via 2 channels and
evaluates the feedback signal STA.
5.2
STO installation
Inputs and outputs for the safety sub-function STO
The 2-channel request for the safety sub-function is made via the digital inputs #STO-A and #STO-B.
The digital input #STO-A must not be connected to the digital input #STO-B. Make sure that no bridges
or the like can be used parallel to the safety sub-function.
The diagnostic contact STA indicates whether the safe state has been reached for the safety sub-func-
tion STO.