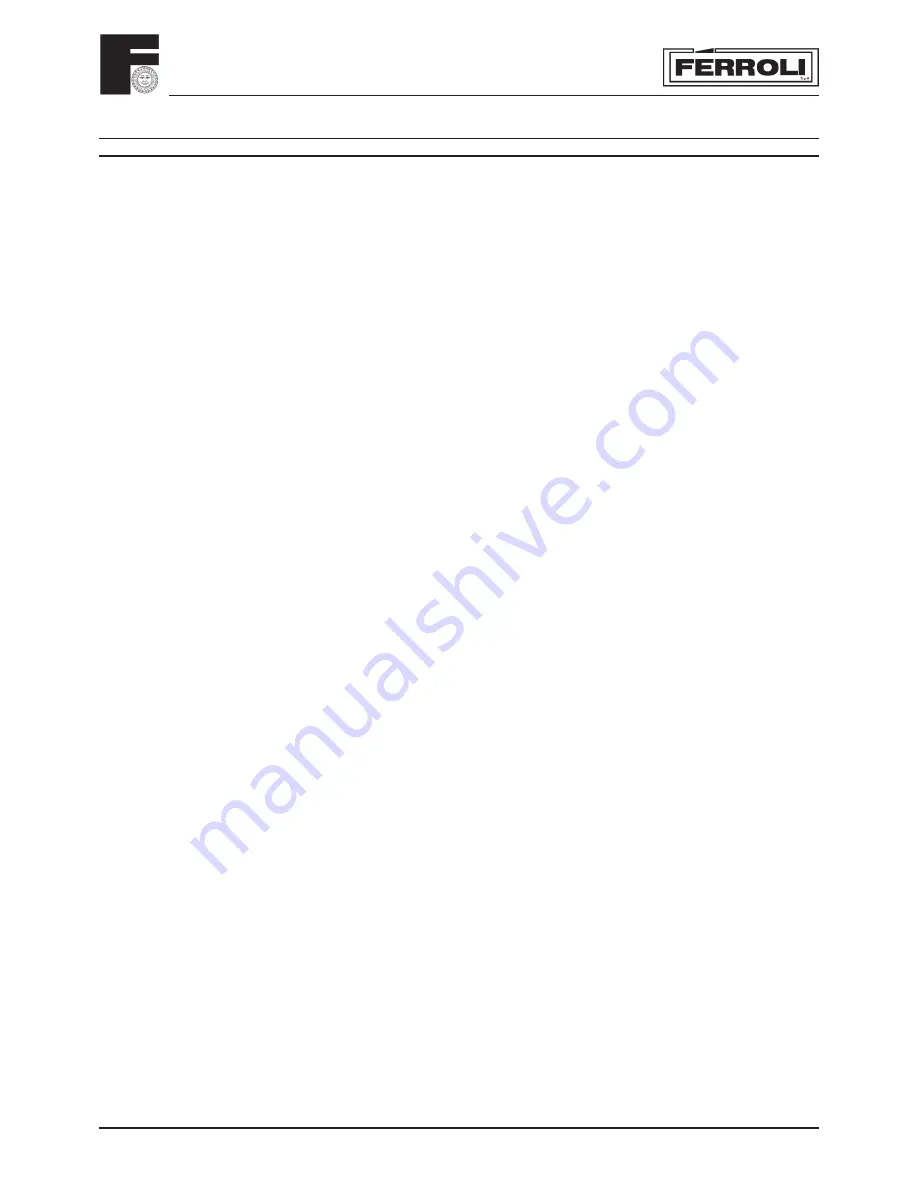
TEMPRA 24
28
4. COMMISSIONING AND TESTING
4.01 Checks to be carried out before starting up for the first time
When starting the boiler up for the fi rst time check:
• that the gate valves between the boiler and central heating systems are open;
• that the central heating system is fi lled and vented;
• that there are no gas or water leaks from the central heating system or boiler;
• that the electric connections are correct and the earth wire of the boiler is connected to an effi cient earthing
installation and a 3amp. fuse is fi tted to the isolator;
• that there are no fl ammable liquids or materials near the boiler;
4.02 Starting up the boiler
• Open the gas cock upstream of the boiler.
• Vent air present in the pipe upstream of the gas valve.
• Turn on electrical supply to the boiler.
• Rotate the ON-OFF RESET switch (fi g. 2 - part 98) into the ON position.
• Check inlet working gas pressure, burner pressures and gas rate.
Turn the knob 63 (fi g. 2) to the “Winter” position. Set the knob above 50°C and set the room thermostat
(if fi tted) to maximum. The burner ignites and the boiler starts to function automatically, controlled by
its control and safety devices.
In “Summer” position the boiler is always shut down.
Note -
If after completing the start-up procedure correctly, the burners fail to ignite and the boiler shut down
warning lights up, wait about 15 seconds then rotate the knob 98 (fi g. 2) against spring pressure to the RESET
position and release it. The reset electronic control unit will repeat the start-up cycle.
Note -
In central heating mode after resetting the boiler will go into it 2 minute delay before starting up again. If after
a second attempt the burners still fail to ignite, consult the paragraph “Troubleshooting”.
Note -
If there is a power failure while the boiler is in operation, the burners automatically go out and
re-ignite when the power returns.
4.03 Shutting down
Close the boiler isolation gas cock and turn off the electricity to the boiler.
Important:
If the boiler is not to be used for lengthy periods during the winter, to avoid frost damage, you are
recommended to drain the water from the circuits (domestic hot water and central heating). Alternatively, drain the
domestic hot water system only and add special anti-freeze to the central heating system.
4.04 Checks and controls after first start-up
• Check there are no leaks in the gas and water circuits.
• Check correct boiler start up by carrying out start up and shut down tests using the boiler stat.
• Check the integrity of the air-fl ue pipes during boiler operation.
• Check that the gas consumption indicated on the meter corresponds to that given in Technical Data (page 5).
• Check that water is circulating correctly. Balance the radiators to ensure that the fl ow and return
differential does not exceed 20°C.
• Check that the gas valve modulates correctly during the central heating phase.
• Determine the combustion effi ciency and the composition of the fl ue gases (refer to 6.04)
• If any of the above are not correct refer to Technical Data (page 5). Adjustment (refer to 5) and Fault fi nding.