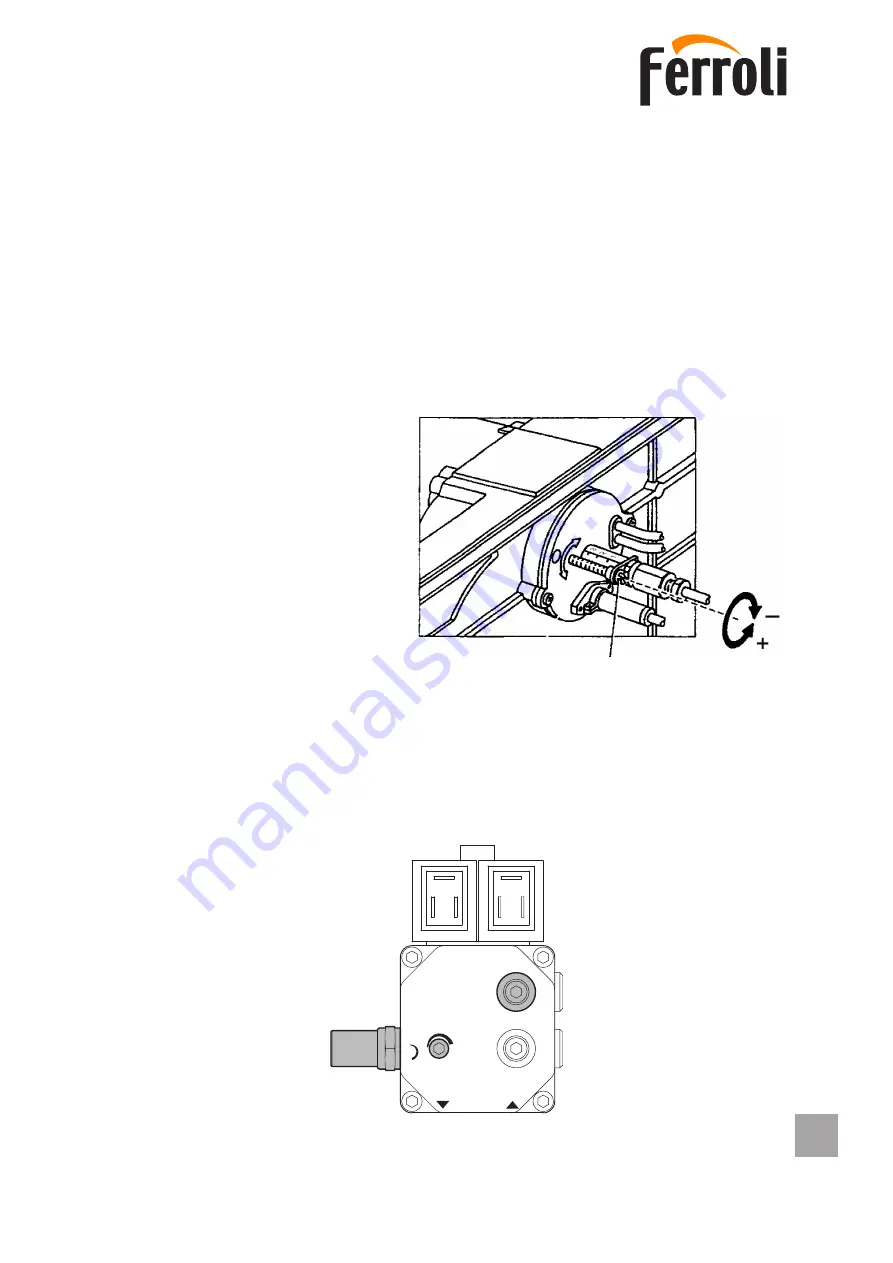
31
UK
NOZZLE HOLDER ADJUSTMENT
The special shape of the draught tube
and the diffuser, the position of which is
adjustable even
when the burner is working, allows
optimisation of combustion parameters
right across the burner flowrate range
and even in critical working conditions.
Turning the screw
A
clockwise results
in the advancement of the nozzle port
and a smaller flow of air around the de
-
flector disc. Turning the screw counter
-
clockwise increases the passage of air.
PUMP PRESSURE ADJUSTMENT
Pump pressure is calibrated at the factory at 10 bar for the 1st stage and 18 bar for the 2nd
stage. However, should it be necessary, pressure can be adjusted by turning the screw (
P1
)
for the 1st stage, and screw (
P1
) for the 2nd stage. To check the obtained pressure fit a pres
-
sure gauge on the pressure take-off point (
P
).
N.B.
With a scale range of up to 30 bar the working range of the pump is min 7 - max 14 bar.
P
-
+
P1
P2
-
+
RECOMMENDATIONS TO PROPERLY SET THE GEARED MOTOR
The geared motor is set upon testing as follows:
Red cam:
is set on approx 90°-120°
Orange cam:
is set on approx 25°÷50°.
Black cam:
is set in such a way that the 2nd stage valve opens when the air shut-off valve
is at 60°÷80°.
Blue cam:
is set on 0°
Changes to this calibration during installation are legible even when the burner is in operation
by acting on the adjusting screws of the cams. Tightening the screws increases the angle
and positioning of the cams.
A