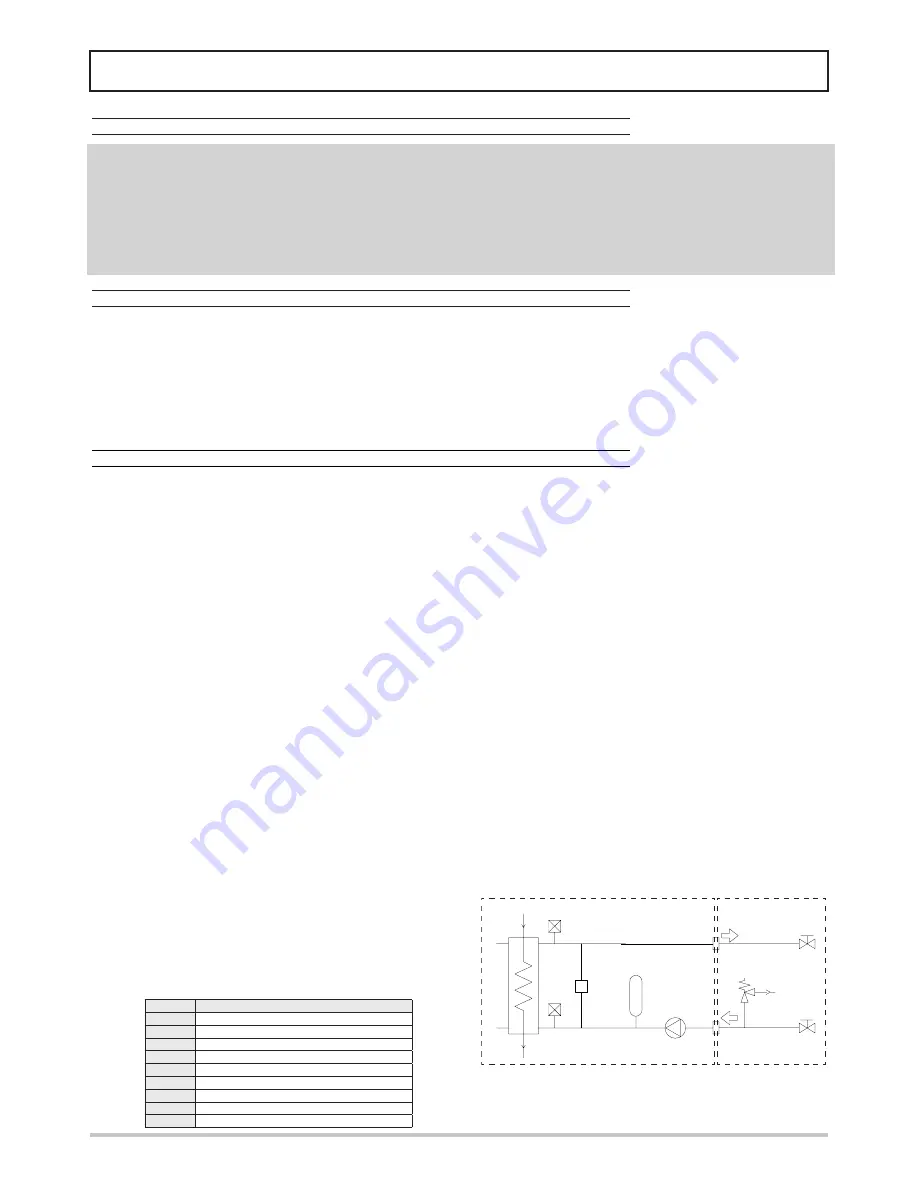
25
HYDRAULIC CONNECTIONS
General rules
A mesh filter (hole Ø<0,5mm for plates heat exchanger) must be installed on the unit’s water inlet otherwise warranty is immediately for-
feited . The filter performs the function of blocking any foreign matter in the system’s plumbing circuit (shavings, machining debris, etc .)
limiting or avoiding possible problems of fouling (that decreases the heat exchange coefficient), erosion, and clogging
The clogging and fouling of the exchanger can lead to a reduction of the water flow rate and . In the case that the exchanger works as
evaporator- of the evaporation temperature: these 2 factors can cause the icing of the exchanger
The icing event leads to the bursting of the exchanger, the inlet of water into the refrigerant circuit and so the necessity of a replacement of
the main components (compressors, filters, expansion valves, . Etc .) and an accurate washing of components as refrigerant pipes, coils,
etc ., practically the rebuilding nearly complete of the refrigerant circuit .
The filter must be maintained clean: this is so necessary verify the cleanness after the unit installation and checking periodically the state .
Protection devices
Standard supply includes a differential pressure switch situated between the water inlet and outlet of the heat exchanger to avoid freezing if
the water flow stops for any reason.
• Standard supply includes an antifreeze heater placed between the external thermal insulation and the shell of the exchanger and controlled
by the main electronic controller of the unit in order to protect the evaporator full of water (but not the pipes) from the winter icing when the
unit is in stand-by mode. The exchanger is protected down to an outdoor air temperature of -20°C.
NOTE the antifreeze protection only worlk if the unit is electrically connected the standby period .
It is recommended to install a water paddle flow switch at
the water inlet of the unit: the water paddle flow switch has to be electrically wired
in series with the differential pressure switch.
It is mandatory to calibrate the trip out of the water paddle flow switch at a water flow rate value higher than the minimum water flow rate
admissible for the exchanger (re. section Pressure Drop).
Tips for a successful installation
For a correct design and installation of the hydraulic plant comply the local laws governing safety matters and sound…
The following information is suggestion for a correct installation of the unit:
• Before connecting the unit to the system wash adequately the pipes using clean water, filling and emptying and cleaning the filters.
Only after that proceed connecting the unit to the system; this operation is crucial to ensure proper start-up without the need to have repeated
stops to clean the filter, with the possible risk of damage to heat exchangers and other components.
• Check by qualified personn
el the quality of the water or of the mixture used; avoid the presence of inorganic salts, biological load (seaweeds,
etc.) suspended solids, dissolved oxygen and the pH. Water with inadequate characteristics can cause a pressure drop increase due to a
rapid fouling of the filter, energy efficiency decrease and corrosive symptom increase that can damage the unit.
• The pipes must have the least possible number of bends to minimize load losses and must be adequately supported in order to prevent the
connections of the unit from being excessively stressed.
• Install on-off valves near components that need to be serviced to isolate them when maintenance work needs to be done and to allow them
to be replaced without having to discharge the system.
• Before isolating the pipes and charging the system, carry out preliminary inspections to make sure that there are no leaks.
• Isolate all the chilled water pipes to prevent condensation from forming along the pipes themselves. Make sure that the material used is the
steam barrier type, failing this, cover the insulation with an appropriate protection. Also make sure that the air venting valves can be accessed
through the insulation.
• Do not forget to install or at least allow for the installation of pressure and temperature reading instruments on the inlet and outlet parts of
the hydraulic circuit. These instruments will allow you to monitor the operation of the system.
• The circuit can be kept under pressure by means of an expansion tank and a pressure reducer. A plant filling unit can also be used in order
to automatically charge the system and keep it at the desired pressure if it drops below a certain pressure value. Install manual or automatic
values in the highest point of the system to eliminate air from the circuit.
Fit manual or automatic valves at the highest point in the circuit in order to vent air from the circuit.
• the water connections are Victaulic-type joints for hooking up to the unit.
The joints allow the pipes to expand due to changes in temperature and in addition the elastomer gasket and the specified play help insulate
and absorb noise and vibration.
• If vibrations dampers are installed under the unit, it is recommended to use flexible couplings before and after the water circulation pump
and near the unit.
• Install on the outlet of the unit a suitable valve able to regulate the water flow.
• Avoid that the weight of the connection pipes pushes on the hydraulic connections of the unit using approved supports.
Check that plant components are suitable to bear the maximum static pressure (it depends on the height of the building).
VP
E
V
SUW
SIW
T
U
O
P
S
N
I
PD
P
S
V
RM
RA
ATTENTION
For units in VP version equipped with expansion vessel is required to
install a safety valve (SET = 3 bar) on the hydraulic circuit. If the unit is
disconnected from the rest of the hydraulic system with shut-off valve or
other equivalent device (eg during maintenance), check that the safety
valve is always connected with the expansion vessel. See diagram:
VP unit version
operation by the
installer
ITEM
DESCRIPTION
P
PUMP
PD
DIFFERENTIAL PRESSURE WATER
RA
SUCTION BALL VALVE
RM
DISCHARGE BALL VALVE
SIW
PROBE WATER INLET
SP
HEAT EXCHANGER
SUW
PROBE WATER OUTLET
VS
SAFETY VALVE
VE
EXPANSION TANK