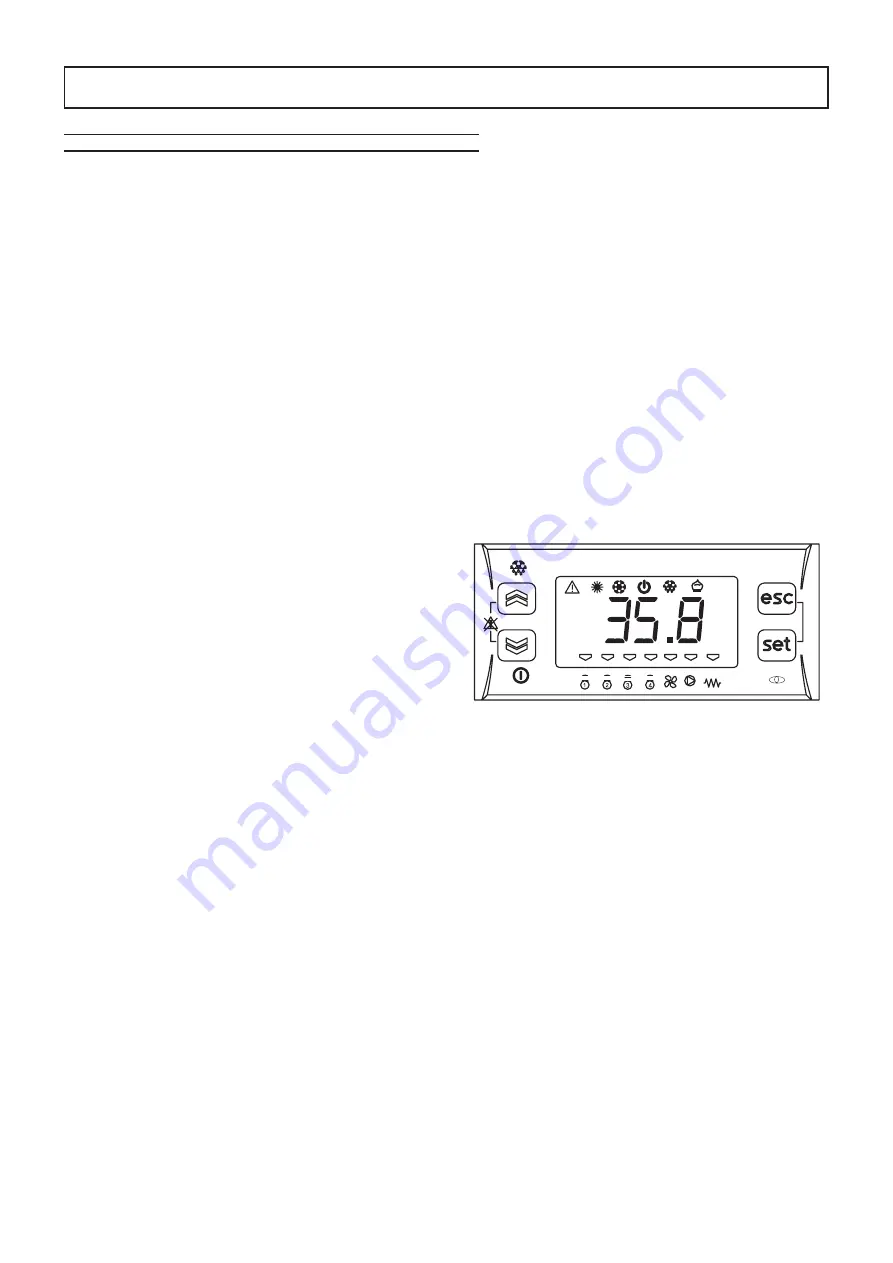
GENERAL SPECIFICATIONS
Description of the components
The complete series of industrial chillers and heat pumps for use in hydronic systems includes
12 constructional sizes
rang
from 53.5 to 200 kW
in the cooling mode.
Main components:
1. Fans.
These are the helical type with scythe-shaped blades to increase the efficiency and reduce the noise level. The fans
are directly coupled to the single-phase motor by means of an external rotor. Thermal protection against operating faults is
installed inside the winding. As standard they are equipped with continuous adjustment of axial fans rotating speed in order
to allow the units to operate both with low outdoor temperature in cooling mode and with high outdoor temperature in heating
mode.
2. Electric control and monitoring panel.
This is housed in a metal casing in which the various electrical components are posi-
tioned on one metal plate.
2a. The power section includes:
•
Main door-locking circuit-breaker.
•
Fuse-holder that can be isolated with protection fuse triad for each compressor.
•
Fuse-holder that can be isolated with protection fuse for compressor oil heaters and antifreeze (if installed).
•
Control conta
ctor for each compressor.
•
Protection fuse for the ventilation unit.
•
Fan speed regulating board.
•
Contactor and magnetothermic switch to protect the pump (if the Hydronic Kit accessory is installed).
•
Pump conta
ctor (if the Hydronic Kit accessory is installed).
•
Phase presence and sequence monitoring device on power supply
2b. The auxiliary section includes:
•
Fuses on the auxiliary transformer.
•
Fuses for fans protection
•
Electromagnetic noise filter
•
Adjusting fan speed board
•
Insulating and safety transformer to power the auxiliary circuit.
2c. The microprocessor monitoring section includes:
•
User interfacing terminal with display.
•
On-off key.
•
Operating mode selector key.
•
Compress
or on-off display
LED
.
•
Operational mode
LED
•
Antifreeze heaters activated indicator
LED
.
•
Fans on-off dislay
LED
•
Pumps on-off display
LED
•
Check-control with fault code display
•
Defro
sting, alarm, economy, stand-by
LED.
•
ON / Stand-by remote - Summer/W
inter (E/I).
Control system main functions:
temperature control of the water produced by the unit, compressor and pump operating hour
counter, timing and cycling of start-ups, input parameters by keyboard, alarms management, dynamic set-point (climatic control),
scheduling and integrative heaters control.
If you installed the hydronic kit these functions are enabled: antifreeze with pump, start-up cycle after prolonged inactivity (anti-
sticking), if the hydronic kit installed has 2 pumps there is a cycling between each pump to ensure an equivalent lifetime, with
inverter modulating hydronic kit the water flow of the plant can be adjusted.
Digital input functions:
low pressure, high pressure, high temperature on compressor supply, phase presence and sequence
monitoring device on power supply, differential water pressure control, compressors thermal protection, fans thermal protection,
pumps thermal protection (only if installed MP accessory), ON/OFF and remote operating mode change, demand limit and
Economy function.
Digital output functions:
compressor start-up, pump start-up (only with MP accessory), plate heat exchanger electrical heater,
remote general alarm, integrative heaters and clean contact on compressors start-up.
Analogic input functions
: in and out water temperature, coil temperature probe, external air temperature probe (if present).
Analogic output functions:
continuous adjustment of axial fans rotating speed, continuous adjustment of pump rotating speed.
°C
MODE
6