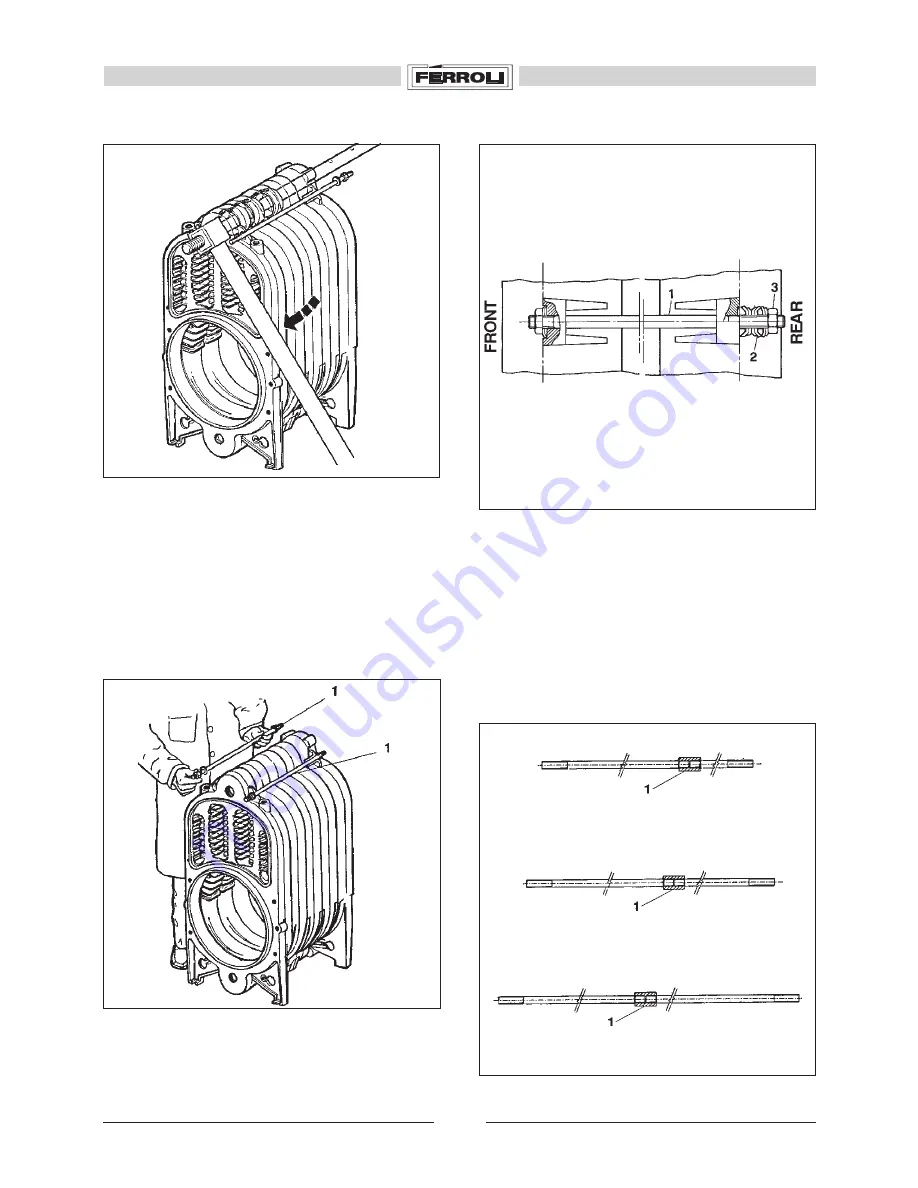
8
GN2
ROD GN2 12 ELEM. LG. TOT. 1290
ROD GN2 12 ELEM. LG. TOT. 1290
ROD GN2 14 ELEM. LG. TOT. 1510
Fig. 16
Fig. 13
4.07 (Figs 11 - 12 - 13) Insert rod 1 between the two
elements, mount nut 3 on the threaded end, place stop
pin 2 on the hole of the rod near the pair of elements then
clamp the unit together using a N
°
4 wrench until the
two elements have been perfectly joined together.
4.08 Proceed as described in the previous paragraph
until all the elements forming the boiler unit have been
mounted.
Fig. 14
4.09 (Figs 14 - 15 - 16) Mount the four rods «1», the
Belleville washers «2» as shown in fig. 15 and finally
torque nuts «3».
Fig. 15
Mounting the rods with the Belleville washers.
NOTE: The Belleville washers must be mounted in an
opposed way as shown in the diagram while the nuts
must be fixed in order to prevent them from being
crushed.
For GN2 boilers with 12 - 13 - 14 elements, mount the
rods with sleeve part 1, remembering to fully tighten the
sleeve thread on both sides.