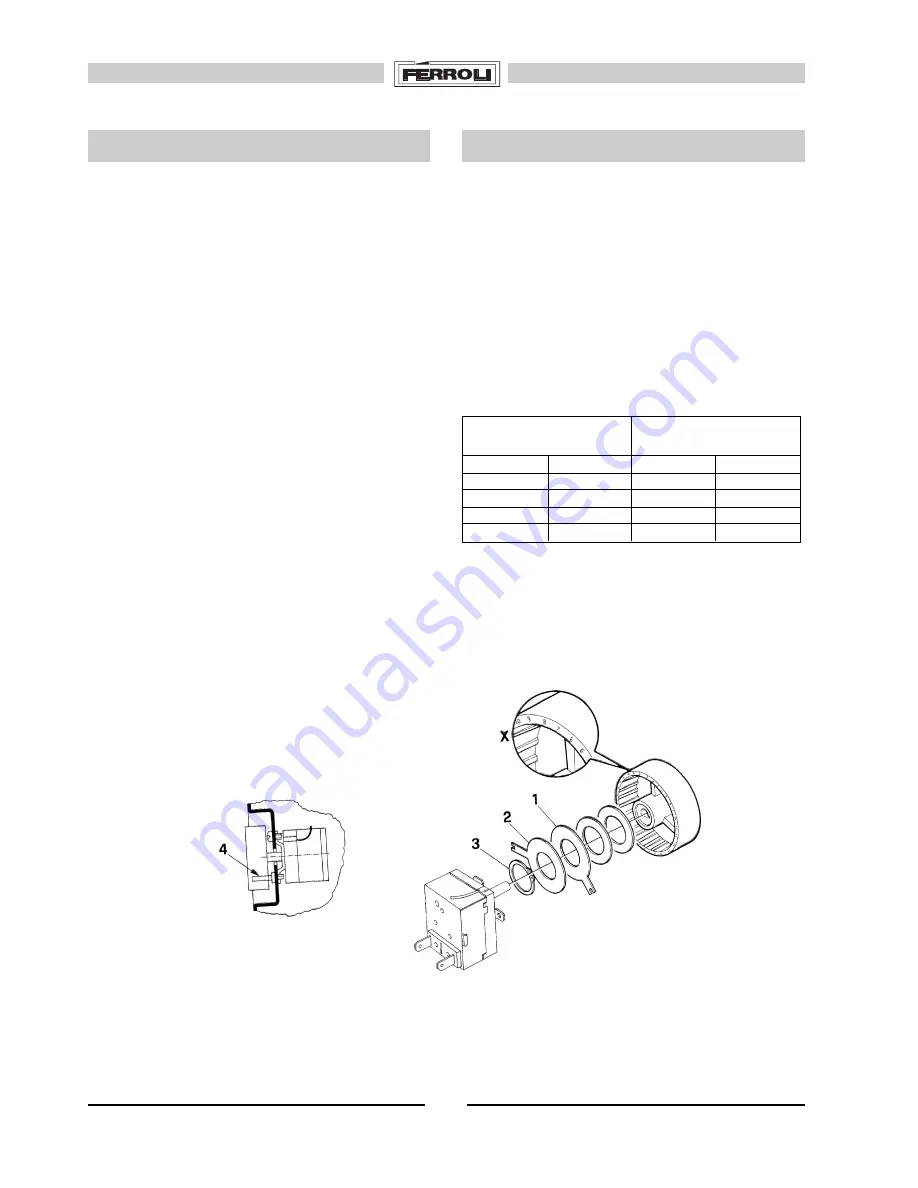
24
GN3
MINIMUM VALUE
MAXIMUM VALUE
X
°
C
X
°
C
26
30
12
80
24
40
14
70
21
50
17
60
19
60
19
50
16
70
22
40
INSPECTIONS
ADJUSTEMENTS
Before initial ignition
Before initial ignition, it is advisable to check that:
a) the system has been filled at the correct pressure and
is well vented;
b) there are no water or fuel leaks;
c) the electrical power supply is correct;
d) the entire fumes duct has been correctly built, that it is
not too near and does not pass through inflammable
parts;
e) that there are no inflammable substances near the
appliance;
f) that the burner is proportional to boiler capacity;
g) the water on-off valves are open.
Burner
Burners fuelled with heating oil or gas, with blown air for
pressurized furnaces, can all be used so long as their
operative characteristics are suitable for the size of the
boiler furnace and its overpressure. The burner must be
chosen according to the Manufacturer’s instructions, in
compliance with fuel consumptions, pressures and the
length of the combustion chamber.
Burners with two flames must have a primary flame
corresponding to at least 50% of the boiler rating.
Boiler efficiency and correct burner operation particularly
depend on accurate adjustments.
NOTE:
Before starting the boiler, always check that the burner
door and smokebox are tight.
Thermostat positioning (fig. 51)
The thermostats are preset in the factory to a minimum
value of 30
°
C and a maximum value of 90
°
C. Proceed in
the following way to vary the regulating range of these
limit values:
a) Remove the thermostat knob.
b) Demount locking circlip 3 and stops 1 and 2.
c) Re-position stops 1 and 2 in their relative housings
marked “X”, corresponding to the required temperature
range (see table).
d) Remount the knob on the thermostat, checking that
prong 4 is between the two knob stops.
Fig. 51