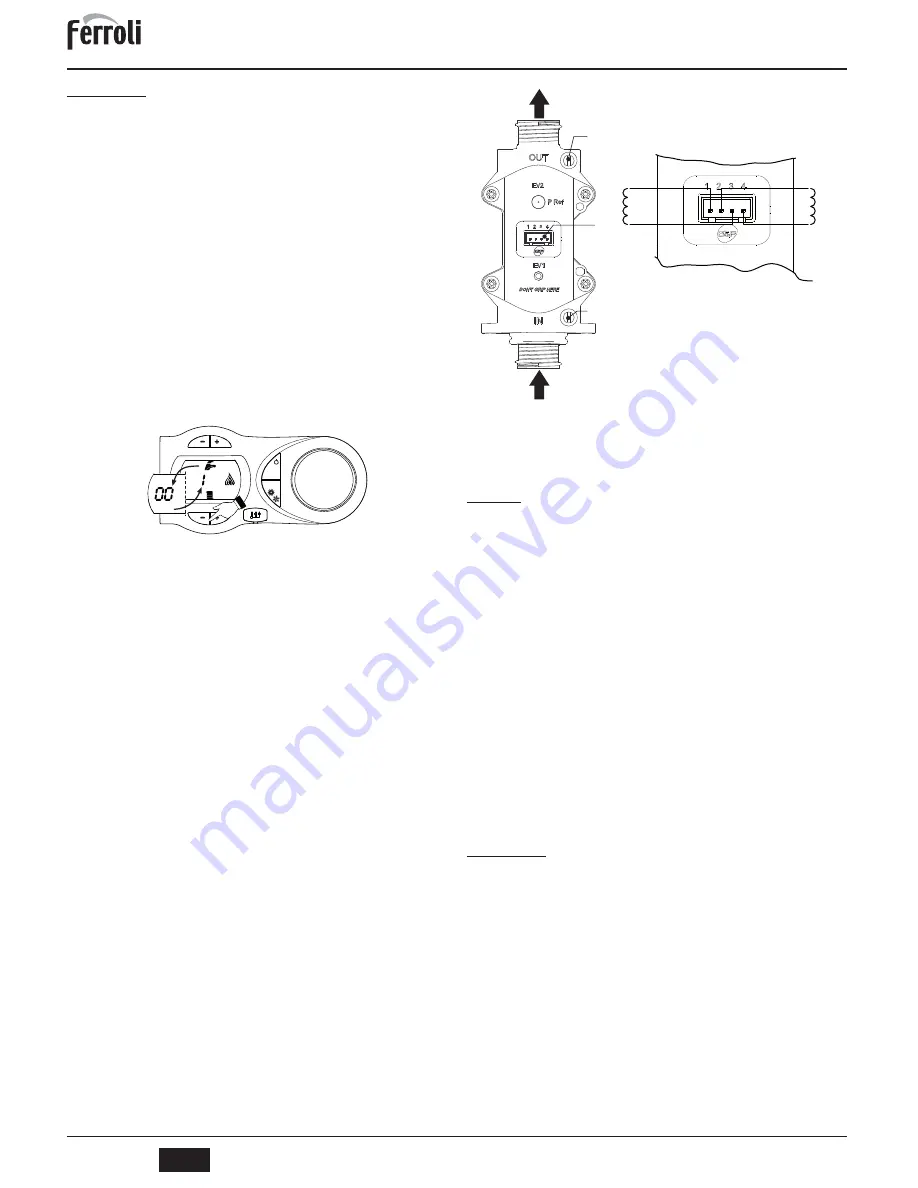
DIVAtech F 32 D
36
(1
cod. 3541A770 -
10
/2011 (Rev. 00)
4. SERVICE AND MAINTENANCE
4.1 Adjustments
Gas conversion
The unit can operate on natural gas or LPG and is factory-set for use with one of these
two gases, as clearly shown on the packing and on the dataplate. Whenever a gas dif-
ferent from that for which the unit is arranged has to be used, the special conversion kit
will be required, proceeding as follows:
1.
Replace the nozzles at the main burner, fitting the nozzles specified in the technical
data table in cap. 5, according to the type of gas used
2.
Modify the parameter for the type of gas:
•
put the boiler in standby mode
•
press the DHW buttons details 1 and 2 - fig. 1 for 10 seconds: the display shows
“
b01
“ blinking.
•
Press the DHW buttons fig. 1 (details 1 and 2 -
) to set parameter 00
(for nat-
ural gas operation) or
01
(for LPG operation).
•
press the DHW buttons details 1 and 2 - fig. 1 for 10 seconds.
•
the boiler will return to standby mode
3.
Adjust the minimum and maximum pressures at the burner (ref. relevant para-
graph), setting the values given in the technical data table for the type of gas used
4.
Apply the sticker contained in the conversion kit, near the dataplate as proof of the
conversion.
TEST mode activation
Press the heating buttons (details 3 and 4 - fig. 1) together for 5 seconds to activate the
TEST
mode. The boiler lights at the maximum heating power set as described in the fol-
lowing section.
The heating and DHW symbols (fig. 14) flash on the display; the heating power will be
displayed alongside.
fig. 14 - TEST mode (heating power = 100%)
Press the heating buttons (details 3 and 4 - fig. 1) to increase or decrease the power
(min.=0%, max.=100%).
Press the DHW button
"-"
(detail 1 - fig. 1) and boiler power is immediately adjusted to
min. (0%). Press the DHW button
"+"
(detail 2 - fig. 1) and boiler power is immediately
adjusted to max. (100%).
If the TEST mode is activated and enough hot water is drawn to activate the DHW mode,
the boiler remains in TEST mode but the 3-way valve goes to DHW.
To deactivate the TEST mode, press the heating buttons (details 3 and 4 - fig. 1) for 5
seconds.
The TEST mode is automatically disabled in any case after 15 minutes or on stopping of
hot water drawing (if enough hot water is drawn to activate the DHW mode).
Pressure adjustment at the burner
Since this unit has flame modulation, there are two fixed pressure settings: minimum and
maximum, which must be those given in the technical data table according to the type of
gas.
•
Connect a suitable pressure gauge to the pressure point
"B"
downstream of the
gas valve.
•
Activate the TEST mode (see cap. 4.1).
•
Press the Eco/Comfort button for 2 seconds to access the gas valve Calibration
mode.
•
The card goes to the setting “q02”; displaying the actually saved value, by pressing
the DHW buttons .
•
If the pressure gauge reading is different from the nominal maximum pressure, pro-
ceed by increases/decreases of 1 or 2 units of parameter “q02” by pressing the
DHW buttons : the value is stored after each modification; wait 10 seconds for the
pressure to stabilise.
•
Press the heating button “-” (ref. 3 - fig. 1).
•
The card goes to the setting “q01”; displaying the actually saved value, by pressing
the DHW buttons .
•
If the pressure gauge reading is different from the nominal minimum pressure, pro-
ceed by increases/decreases of 1 or 2 units of parameter “q01” by pressing the
DHW buttons : the value is stored after each modification; wait 10 seconds for the
pressure to stabilise.
•
Recheck both adjustments by pressing the heating buttons and adjust them if nec-
essary by repeating the above procedure.
•
Press the Eco/Comfort button for 2 seconds to return to the TEST mode.
•
Deactivate the TEST mode (see cap. 4.1).
•
Disconnect the pressure gauge.
Heating power adjustment
To adjust the heating power, switch the boiler to TEST mode (see sec. 4.1). Press the
heating buttons detail 3 - fig. 1 to increase or decrease the power (min. = 00 - max. =
100). Press the
reset
button within 5 seconds and the max. power will remain that just
set. Exit TEST mode (see sec. 4.1).
4.2 Startup
Before lighting the boiler
•
Check the seal of the gas system.
•
Check correct prefilling of the expansion tank.
•
Fill the water system and make sure all air contained in the boiler and the system
has been vented.
•
Make sure there are no water leaks in the system, DHW circuits, connections or boil-
er.
•
Check correct connection of the electrical system and efficiency of the earthing sys-
tem.
•
Make sure the gas pressure for heating is that required.
•
Make sure there are no flammable liquids or materials in the immediate vicinity of
the boiler
Checks during operation
•
Switch the unit on.
•
Check the tightness of the fuel circuit and water systems.
•
Check the efficiency of the flue and air/fume ducts while the boiler is working.
•
Make sure the water is circulating properly between the boiler and the systems.
•
Make sure the gas valve modulates correctly in the heating and domestic hot water
production stages.
•
Check correct boiler lighting by performing various tests, turning it on and off with
the room thermostat or remote control.
•
Make sure the fuel consumption indicated on the meter matches that given in the
technical data table in cap. 5.
•
Make sure that with no demand for heating, the burner lights correctly on opening a
hot water tap. Check that in heating mode, on opening a hot water tap, the heating
circulating pump stops and there is regular production of hot water.
•
Make sure the parameters are programmed correctly and carry out any required
customisation (compensation curve, power, temperatures, etc.).
4.3 Maintenance
Periodical check
To ensure correct operation of the unit over time, have qualified personnel carry out a
yearly check, providing for the following:
•
The control and safety devices (gas valve, flow meter, thermostats, etc.) must func-
tion correctly.
•
The fume exhaust circuit must be perfectly efficient.
(Sealed chamber boiler: fan, pressure switch, etc. -The sealed chamber must be
tight: seals, cable glands, etc.)
(Open chamber boiler: anti-backflow device, fume thermostat, etc.)
•
The air-fume end piece and ducts must be free of obstructions and leaks
•
The burner and exchanger must be clean and free of deposits. For possible cleaning
do not use chemical products or wire brushes.
•
The electrode must be properly positioned and free of scale.
eco
comfort
reset
II
II
II
I I
I I I I I I
II
II
II
II
II
II
II
I I
I I I I I I
II
II
II
II
fig. 15 - Gas valve
A
- Upstream pressure point
B
- Downstream pressure point
I
- Gas valve electrical connection
R
- Gas outlet
S
- Gas inlet
fig. 16 - Gas valve connection
TYPE SGV100
Pi max 65 mbar
24 Vdc - class B+A
R
B
I
A
S
~ 65
Ω
~ 24
Ω
Summary of Contents for DIVAtech F 32D
Page 31: ......
Page 79: ......
Page 80: ...FERROLI S p A Via Ritonda 78 a 37047 San Bonifacio Verona ITALY www ferroli it ...