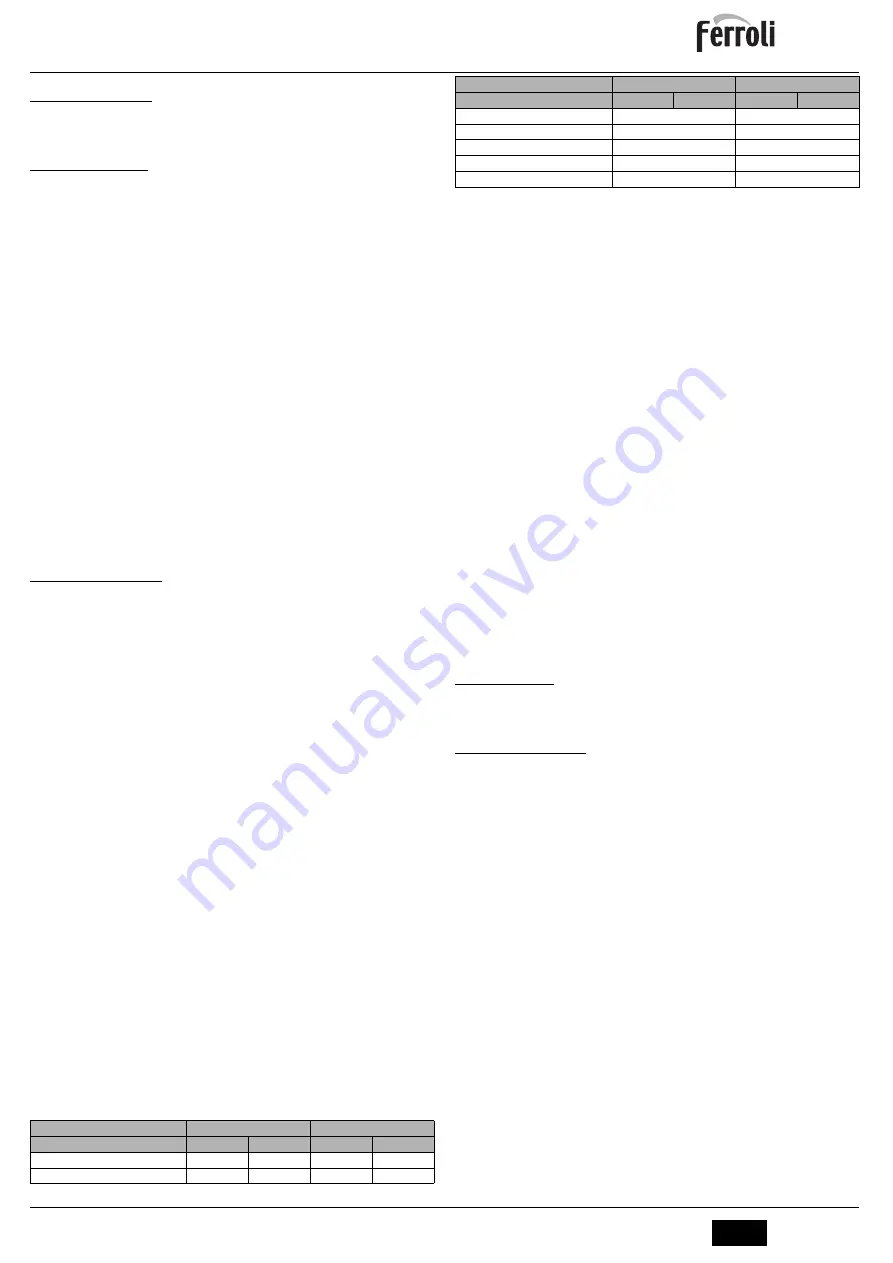
DIVACONDENS D PLUS F 24
41
EN
cod. 3541P653 - Rev. 01 - 03/2021
3. INSTALLATION
3.1 General Instructions
BOILER INSTALLATION MUST ONLY BE PERFORMED BY QUALIFIED PERSON-
NEL, IN ACCORDANCE WITH ALL THE INSTRUCTIONS GIVEN IN THIS TECHNICAL
MANUAL, THE PROVISIONS OF CURRENT LAW, THE PRESCRIPTIONS OF NA-
TIONAL AND LOCAL STANDARDS AND THE RULES OF PROPER WORKMANSHIP.
3.2 Place of installation
B
The combustion circuit is sealed with re-
spect to the place of installation and there-
fore the unit can be installed in any room
except in a garage. The place of installa-
tion must be sufficiently ventilated to pre-
vent the creation of dangerous conditions
in case of even small gas leaks. Otherwise
there may be a risk of suffocation and in-
toxication or explosion and fire. This safe-
ty precaution is required by EEC Directive
No. 2009/142 for all gas units, including so-
called sealed chamber units.
The unit is designed to operate in a partially protected place, with a minimum tempera-
ture of -5°C. If provided with the special antifreeze kit, it can be used with a minimum tem-
perature down to -15°C. The boiler must be installed in a sheltered place, for instance
under the slope of a roof, inside a balcony or in a protected recess.
The place of installation must be free of flammable materials, objects and dusts or cor-
rosive gases.
The boiler is arranged for wall mounting and comes as standard with a hooking bracket.
Wall fixing must ensure stable and effective support for the generator.
A
If the unit is enclosed in a cabinet or mounted alongside, there must be suffi-
cient space for removing the casing and for normal maintenance activities
3.3 Plumbing connections
Important
B
The safety valve outlet must be connected to
a funnel or collection pipe to prevent water
spurting onto the floor in case of overpressure
in the heating circuit. Otherwise, if the dis-
charge valve cuts in and floods the room, the
boiler manufacturer cannot be held liable.
B
Before making the connection, check that the
unit is arranged for operation with the type of
fuel available and carefully clean all the sys-
tem pipes.
Carry out the relevant connections according to the diagram in and the symbols on the
unit.
Note:
The unit is equipped with an internal bypass in the heating circuit.
System water characteristics
A
DIVACONDENS D PLUS F 24
boilers are suitable for installation in heating
systems with non-significant entry of oxygen (ref. systems "case I" EN14868).
A physical separator (e.g. plate heat exchanger) must be provided in systems
with continuous entry of oxygen (e.g. underfloor systems without antidiffusion
pipes or open vessel), or intermittent (less than 20% of system water content).
The water within a heating system must have the characteristics required by
UNI 8065, and comply with laws and regulations in force and the provisions of
EN14868 (protection of metallic materials against corrosion).
The filling water (first filling and subsequent replenishment) must be clear, with
the hardness indicated in the table below and treated with chemical condition-
ers that prevent encrustations, corrosive or aggressive phenomena on metals
and plastics, the formation of gas, and the proliferation of bacterial or microbial
masses in low temperature systems.
The water contained in the system must be checked periodically (at least twice
a year during the seasons of use, as required by UNI8065) and possibly have
a clear appearance and must comply with the limits given in the following table.
It must contain chemical conditioners in a concentration sufficient to protect the
system for at least one year. Bacterial or microbial loads must not be present
in low temperature systems.
Only use conditioners, additives, inhibitors and antifreeze liquids declared by
the producer suitable for use in heating systems and that do not cause damage
to the heat exchanger or other components and/or materials of the boiler and
system.
Chemical conditioners must ensure complete deoxygenation of the water, con-
tain specific protection for yellow metals (copper and its alloys), anti-fouling
agents for scale, neutral pH stabilizers and, in low-temperature systems, spe-
cific biocides for use in heating systems.
Recommended chemical conditioners:
SENTINEL X100 and SENTINEL X200
FERNOX F1 and FERNOX F3
The unit is equipped with a frost protection system that activates the boiler in
heating mode when the system delivery water temperature falls below 6°C. The
device is not active if the power and/or gas supply to the unit is turned off. If nec-
essary, for system protection use a suitable antifreeze liquid that meets the
same requirements as set out above and provided for by UNI 8065.
In the presence of adequate chemical/physical system and feed water treat-
ments and related high cyclicity controls able to ensure the required parame-
ters, for industrial process applications the product can be installed in open-
vessel systems with vessel hydrostatic height able to ensure compliance with
the minimum operating pressure indicated in the product technical specifica-
tions.
The presence of deposits on the boiler exchange surfaces due to non-
compliance with the above requirements will involve non-recognition of
the warranty.
Frost protection system, antifreeze liquids, additives and inhibitors
If necessary, the use of antifreeze liquids, additives and inhibitors is allowed, only and
exclusively if their manufacturer guarantees that the products are suitable for use and do
not cause damage to the boiler’s heat exchanger.or other components and/or materials
of the boiler and system. It is prohibited to use generic antifreeze liquids, additives or in-
hibitors that are not expressly suitable for use in heating systems and compatible with
the materials of the boiler and system
3.4 Gas connection
The gas must be connected to the relevant connection (see ) in conformity with the cur-
rent standards, using a rigid metal pipe or a continuous surface flexible s/steel tube and
installing a gas cock between the system and boiler. Make sure all the gas connections
are tight.
3.5 Electrical connections
ATTENTION
B
BEFORE CARRYING OUT ANY OPERA-
TION REQUIRING REMOVAL OF THE CAS-
ING, DISCONNECT THE BOILER FROM
THE ELECTRIC MAINS WITH THE MAIN
SWITCH.
NEVER TOUCH THE ELECTRICAL COM-
PONENTS OR CONTACTS WITH THE MAIN
SWITCH TURNED ON! DANGER OF ELEC-
TRIC SHOCK WITH RISK OF INJURY OR
DEATH!
B
The unit must be connected to an efficient
grounding system in accordance with applica-
ble safety regulations. Have the efficiency and
suitability of the grounding system checked by
professionally qualified personnel; the Manu-
facturer declines any liability for damage
caused by failure to ground the system.
The boiler is pre-wired and equipped with a
three-core connection cable to the electric line
EXISTING SYSTEM
NEW SYSTEM
WATER PARAMETER
P < 150 kW
P > 150 kW
P < 150 kW
P > 150 kW
Total filling water hardness (°F)
<10
<5
<10
<5
Total system water hardness (°F)
<15
<10
<10
<5
PH
7 < Ph < 8.5
7 < Ph < 8.5
Copper Cu (mg/l)
Cu < 0.5 mg/l
Cu < 0.5 mg/l
Iron Fe (mg/l)
Fe < 0.5 mg/l
Fe < 0.5 mg/l
Chlorides (mg/l)
Cl < 30 mg/l
Cl < 30 mg/l
Conductivity (µS/cm)
< 200 µS/cm
< 200 µS/cm
EXISTING SYSTEM
NEW SYSTEM
WATER PARAMETER
P < 150 kW
P > 150 kW
P < 150 kW
P > 150 kW
Summary of Contents for DIVACONDENS D PLUS F 24
Page 107: ......