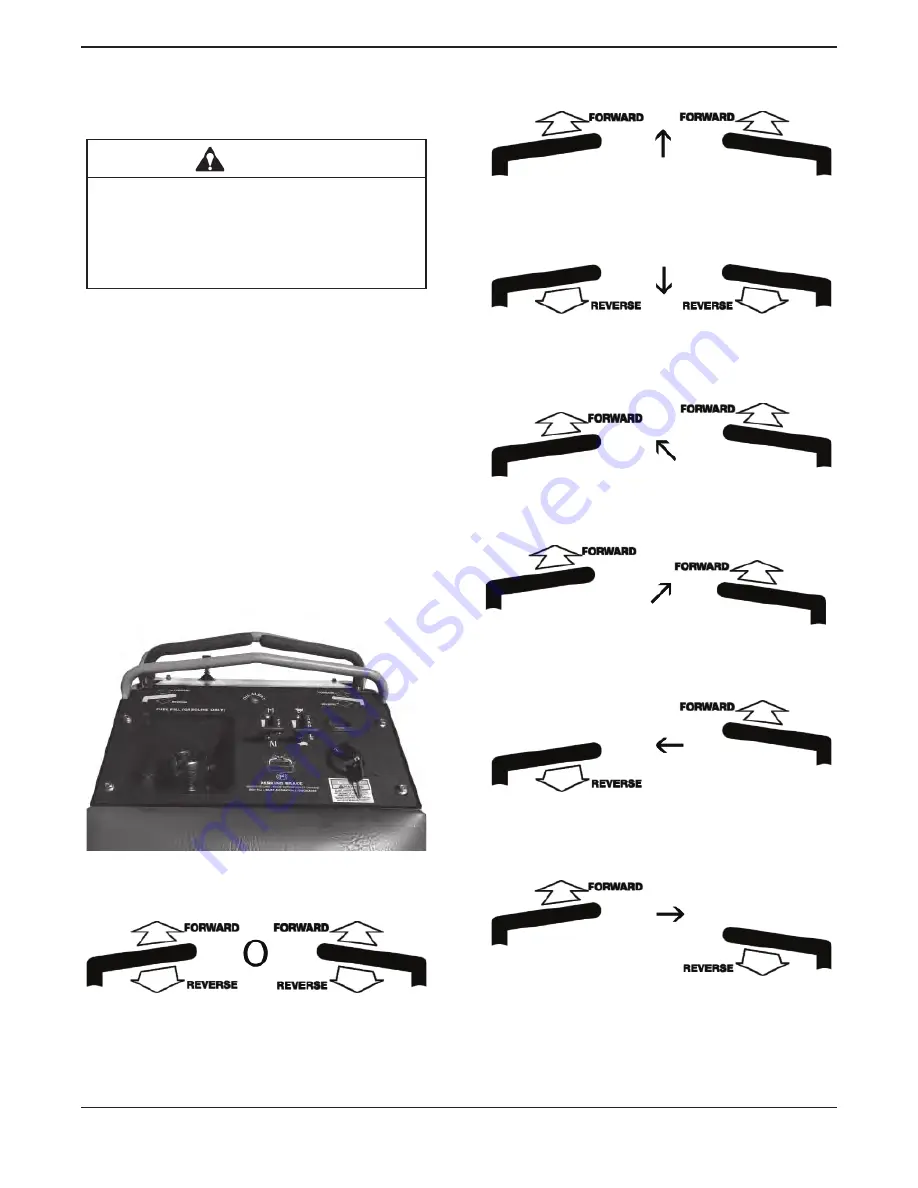
Not for
Reproduction
18
ferrismowers.com
Operation
Using the Hydrostatic Motion Controls
CAUTION
Avoid injury! Learn the proper use of the
motion control levers and practice at low
throttle until becoming profi cient and com-
fortable with the operation of the machine.
DO NOT
move motion control levers from FORWARD
to REVERSE or REVERSE to FORWARD position
rapidly. Sudden direction changes could cause loss
of control or damage the machine.
The functions of the hydrostatic motion control levers
are:
•
Forward and reverse movement.
•
Steering.
•
Acceleration and Deceleration.
•
Stopping.
This photo shows the hydrostatic control levers are in
the NEUTRAL position.
This is the NEUTRAL position.
This is the FORWARD travel position. The travel
speed is dependant on how far forward the controls
are pushed.
This is the REVERSE travel position. The travel
speed is dependant on how far rearward the controls
are pulled.
For a gentle left turn, Push the right motion control
lever further forward than the left motion control lever.
For a gentle right turn, Push the left motion control
lever further forward than the right motion control le-
ver.
For a sharp left turn, Pull the left motion control lever
rearward and push the right motion control lever for-
ward.
For a sharp right turn, Push the left motion control le-
ver forward and pull the right motion control lever rear-
ward.