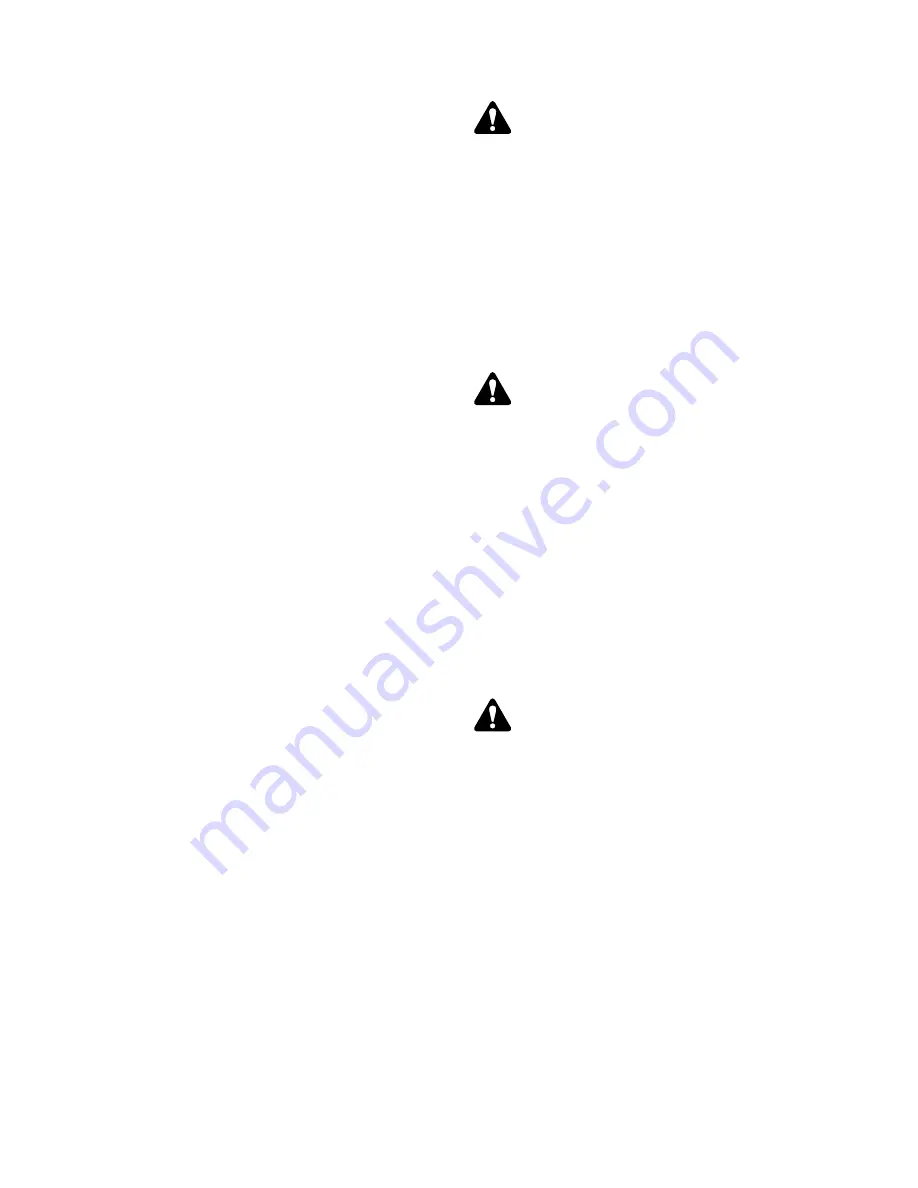
Not for
Reproduction
8
Maintenance and Storage
• Always observe safe refueling and fuel handling practices
when refueling the unit after transportation or storage.
• Always follow the engine manual instructions for storage
preparations before storing the unit for both short and
long term periods.
• Always follow the engine manual instructions for proper
start-up procedures when returning the unit to service.
• Never store the machine or fuel container inside where
there is an open flame, such as in a water heater. Allow
unit to cool before storing.
• If equipped with a fuel shut off valve, shut off fuel while
storing or transporting.
• Do not store fuel near flames or drain indoors.
• Keep all hardware tight and keep all parts in good
working condition. Replace all worn or damaged decals.
• Never tamper with safety devices. Check their proper
operation regularly.
• Disengage the spreader spinner, set the parking brake,
stop the engine, remove the ignition key, and disconnect
spark plug wire. Wait for all movement to stop before
adjusting, cleaning or repairing.
• Clean grass and debris from moving parts, drives,
mufflers, and engine to prevent fires. Clean up oil or fuel
spillage.
• Let engine cool before storing and do not store near
flame.
• Stop and inspect the equipment if you strike an object.
Repair, if necessary, before restarting.
• Park machine on level ground. Never allow untrained
personnel to service machine.
• Use jack stands to support components when required.
• Carefully release pressure from components with stored
energy.
• Disconnect the battery cables from the battery and
remove spark plug wire before making any repairs.
Disconnect the negative battery terminal first and the
positive terminal last. Reconnect positive terminal first
and negative terminal last.
• Keep hands and feet away from moving parts. If possible,
do not make adjustments with the engine running.
• Charge batteries in an open well ventilated area, away
from spark and flames. Unplug charger before connecting
or disconnecting from battery. Wear protective clothes
and use insulated tools.
• Check brake operation frequently. Adjust and service as
required.
• Use only factory authorized replacement parts when
making repairs.
• Always comply with factory specifications on all settings
and adjustments.
• Only authorized service locations should be utilized for
major service and repair requirements.
• Never attempt to make major repairs on this unit unless
you have been properly trained. Improper service
procedures can result in hazardous operation, equipment
damage and voiding of manufacturer’s warranty.
WARNING
Units with hydraulic pumps, hoses, or motors:
Hydraulic
fluid escaping under pressure may have sufficient force to
penetrate skin and cause serious injury. If foreign fluid is
injected into the skin it must be surgically removed within
a few hours by a doctor familiar with this form of injury or
gangrene may result. Keep body and hands away from
pin holes or nozzles that eject hydraulic fluid under high
pressure. Use paper or cardboard, and not hands, to search
for leaks. Make sure all hydraulic fluid connections are tight
and all hydraulic hoses and lines are in good condition
before applying pressure to the system. If leaks occur, have
the unit serviced immediately by your authorized dealer.
WARNING
Stored energy device.
Improper release of springs can result in serious personal
injury. Springs should be removed by an authorized
technician.
• Always disengage the spreader spinner and close the
hopper gate before maintenance or storage.
• Empty the fertilizer hopper before lifting or tilting the
machine for maintenance or storage.
Safety Decals and Icons
Read the safety decals before operating your unit. The
cautions and warnings are for your safety. Understand and
follow all safety decals to avoid a personal injury or damage
to the unit.
WARNING
If any safety decals become worn or damaged, and
cannot be read, order replacement decals from your
local dealer.