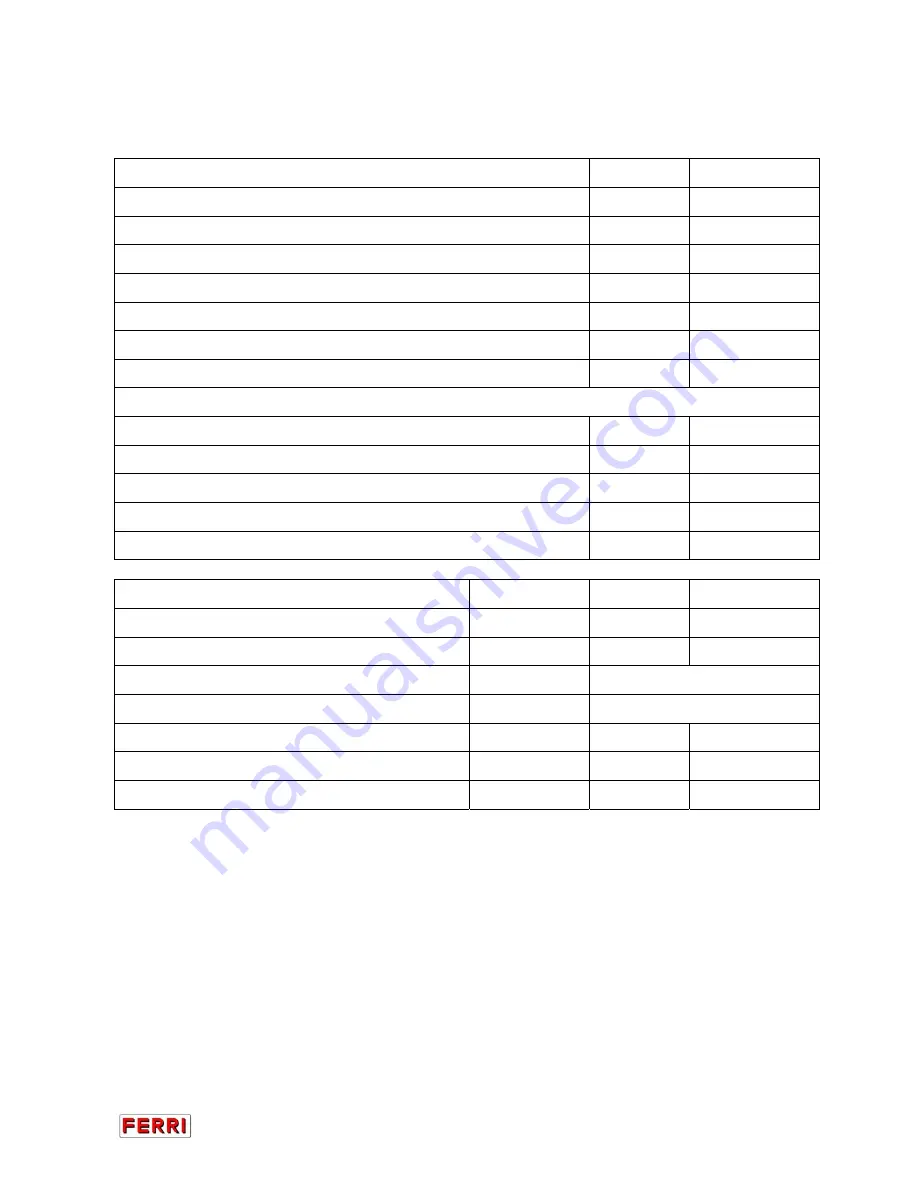
7
2.2
Technical specifications
(Tab. 1)
TAB. 1
FLAIL HEDGE MOWER
MOD.
TKD 54
Min. tractor required power
HP (Kw)
90/100 (74/66)
Min. tractor required weight
Kg. (lbs)
4400 (9500)
PTO speed
rpm
1000
Voltage of the electrical system
volt
12
Max. absorbed power
HP (Kw)
73 (53)
Standard weight of the machine
Kg. (lbs)
1645 (3553)
Attachment to the tractor
Cat.
II
HYDRAULIC SYSTEM
Hydraulic oil
Lt (gal)
105
Intake filter
micron
10
Return filter
micron
30
Max. arm pressure
Bar (PSI)
200 (3300)
Max. flail head pressure
Bar (PSI)
280 (4060)
FLAIL HEAD
MOD.
TNP 125
TNCD 120
Width of cut
Cm (in)
125 (49)
110 (43)
Flail head weight
Kg. (lbs)
386 (833)
325 (715)
Head movement
°
235°
Rotor speed
rpm
3000
Multi-use flails
N.
44+22
36+18
Articulated “Y” flails
N.
60+30
48+24
Hammer blades
N.
22
18