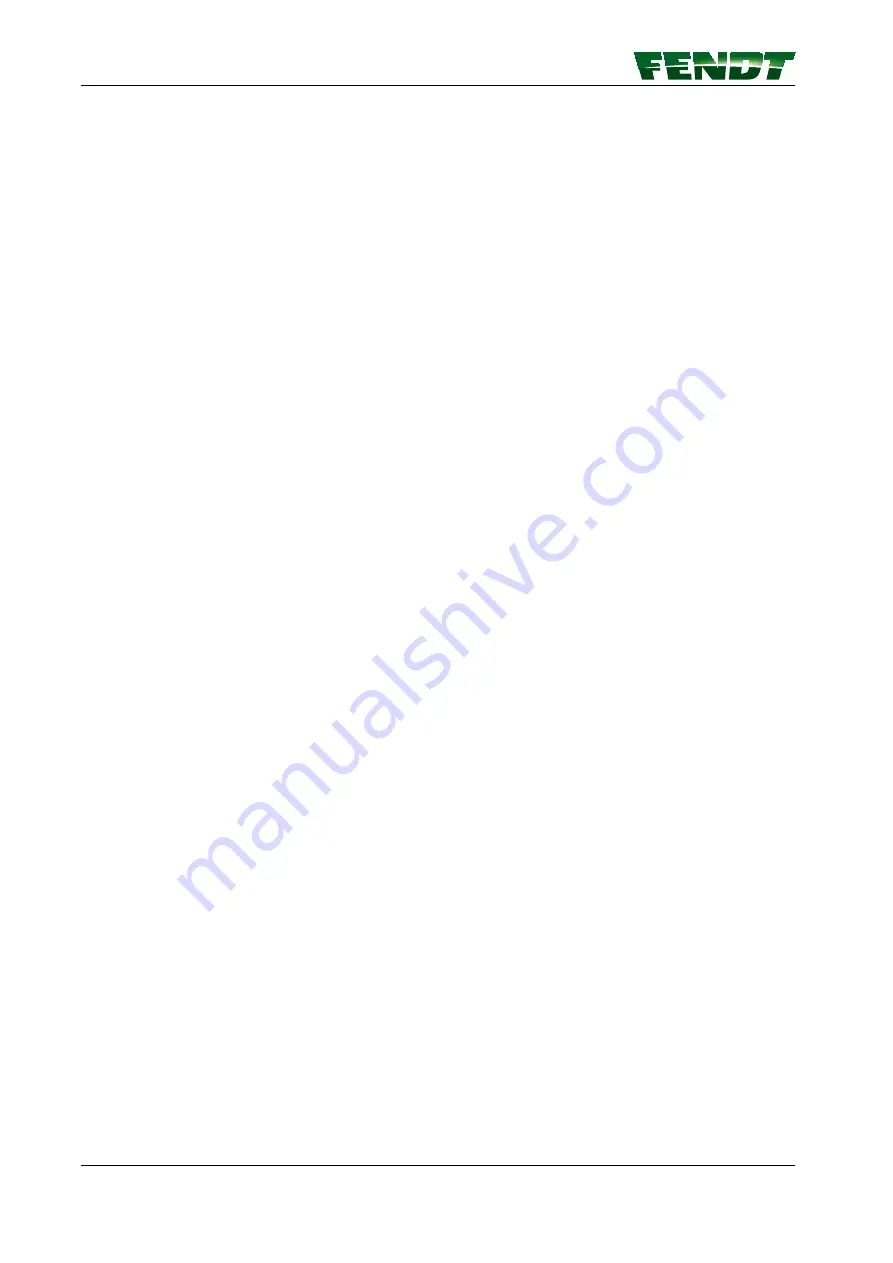
• Always check the brakes before driving.
• Adjustments and repairs to the brake system must be carried out in specialist workshops or by
approved brake repair technicians.
• It must not be possible to brake individual wheels when driving (lock pedals)!
4. Working on the engine
• After switching the engine off, wait 30 seconds before carrying out any work on the fuel system.
• Only start the engine once all safety guards have been attached and nobody is standing in the danger
area.
• Never let the engine run in enclosed spaces with no exhaust gas suction system.
• Cleaning, maintenance and repair work may only be carried out once the engine is switched off and
secured to prevent it starting.
• Injection pipes and high-pressures lines must not be deformed.
• Any damaged injection pipe or high-pressure line must be replaced.
• Do not loosen any injection pipes for high-pressure fuel lines while the engine is running.
• Before carrying out checks to the running engine, always perform a visual check of all high-pressure
components. Suitable protective clothing (e.g. protective goggles) should be worn while doing this.
Leaks indicate potential sources of danger for workshop personnel.
• In the event of leaks to the high-pressure fuel system, always remain out of range of any possible fuel
spray to avoid serious injury.
• Even when no leaks to the high-pressure fuel system can be detected, workshop personnel should
avoid the immediate danger area and wear suitable protective clothing (such as protective goggles)
when carrying out checks to the running engine and during the first test run.
• Smoking is forbidden while carrying out work to the fuel system.
• Do not work in the proximity of sparks or naked flames.
• Never disconnect an injector while the engine is running.
5. Working on the PTO
• Always switch off the engine before fitting or removing the drive shaft. PTO in "0" position!
• When working on the PTO, allow no-one in the vicinity of the rotating PTO or drive shaft.
• Make sure drive shaft and PTO are equipped with shield pipes and protective funnels.
• After deactivating the PTO, it is possible that parts on the mounted implement may continue to run. In
this case, do not get too close to the implement. Work may only be carried out to the implement when
nothing is moving!
• When the drive shaft is removed, cover the PTO shaft with its protective cap.
• Nobody should be in the cab when installing and removing the drive shaft.
Operation of controls for the tractor and mounted implements by people in the cab, especially children,
may result in severe or fatal injury.
6. Working on the front loader
• Before undertaking maintenance work, lower the front loader to the ground, switch off the engine and
remove the ignition key.
• In the event of a collapsed pipe rupture feature, support the load before starting repair work, and slowly
retract the cylinder.
• Check hydraulic hoses and pipes for signs of damage and aging regularly and replace with genuine
spare parts in good time.
• Following installation and repairs, operate the tractor for a short time, then retighten all nuts and bolts
and check them regularly.
• Retighten eccentric bolt for front loader attachment, if necessary.
Disposal
The work described in the operator's manual and workshop manual includes replacing parts, fuel and
lubricants. These renewed parts/fuel/lubricants must be stored, transported and disposed of in accordance
1. Overall system/tractor
1-6
FENDT 800 Vario S4
X990.005.530.013