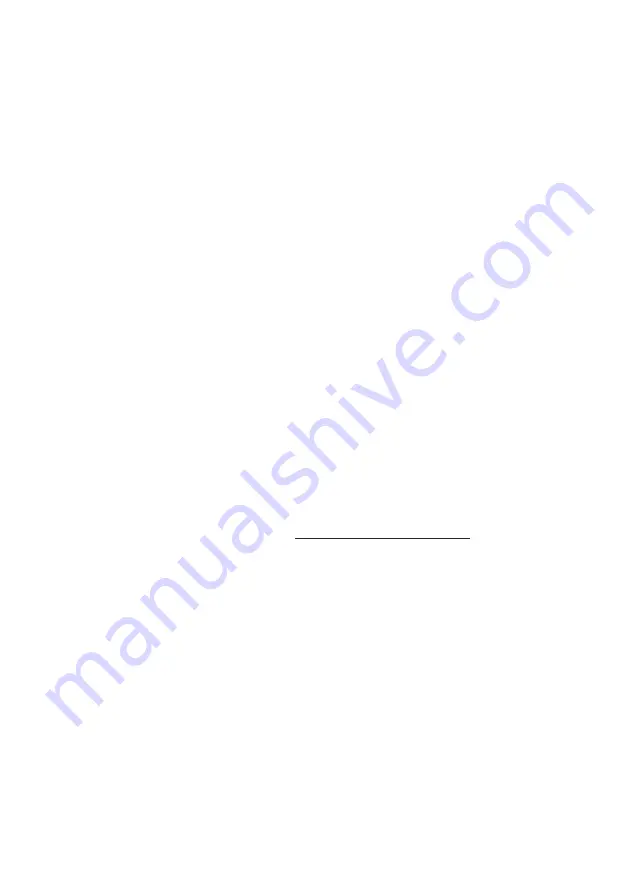
11
6. Interpretation of the results on forming fabrics
The high accuracy of Feltest Caliper Profilers has the advantage that
even small dynamic changes in the forming fabric can be measured.
For example, due to high fabric tension the caliper can decrease up
to 0.04 mm in SSB fabrics. And even more on single and double
layer forming fabrics.
To get a feeling for the degree of caliper change due to fabric
tension, measure the same fabric at two positions with different
tension. For example just after the drive roll
(relatively low fabric
tension)
and at a safe distance before the breast roll
(relatively high
fabric tension)
.
Most suppliers of forming fabrics recommend a minimum caliper
for their products. Usually the thinnest spot determines when a
forming fabric must be replaced.
This spot often can be found within 30 cm from the wire edge;
because of wear caused by the edges of foils, poorly positioned
stops on suction boxes, etc. etc..
Rest potential [%] = caliper(run) – caliper(min) x 100%
caliper(min)
Note:
Above calculation doesn’t take into account from which side the
fabric has lost material. Usually forming fabrics have more material
at the machine side to withstand abrasion; The warp, which gives
the fabric it’s strength, is usually located on the paper side. Hence,
a caliper decrease is much more serious if the material is lost on the
paper side then when it would be lost from the roll side! Visual
inspection during a stop is required.