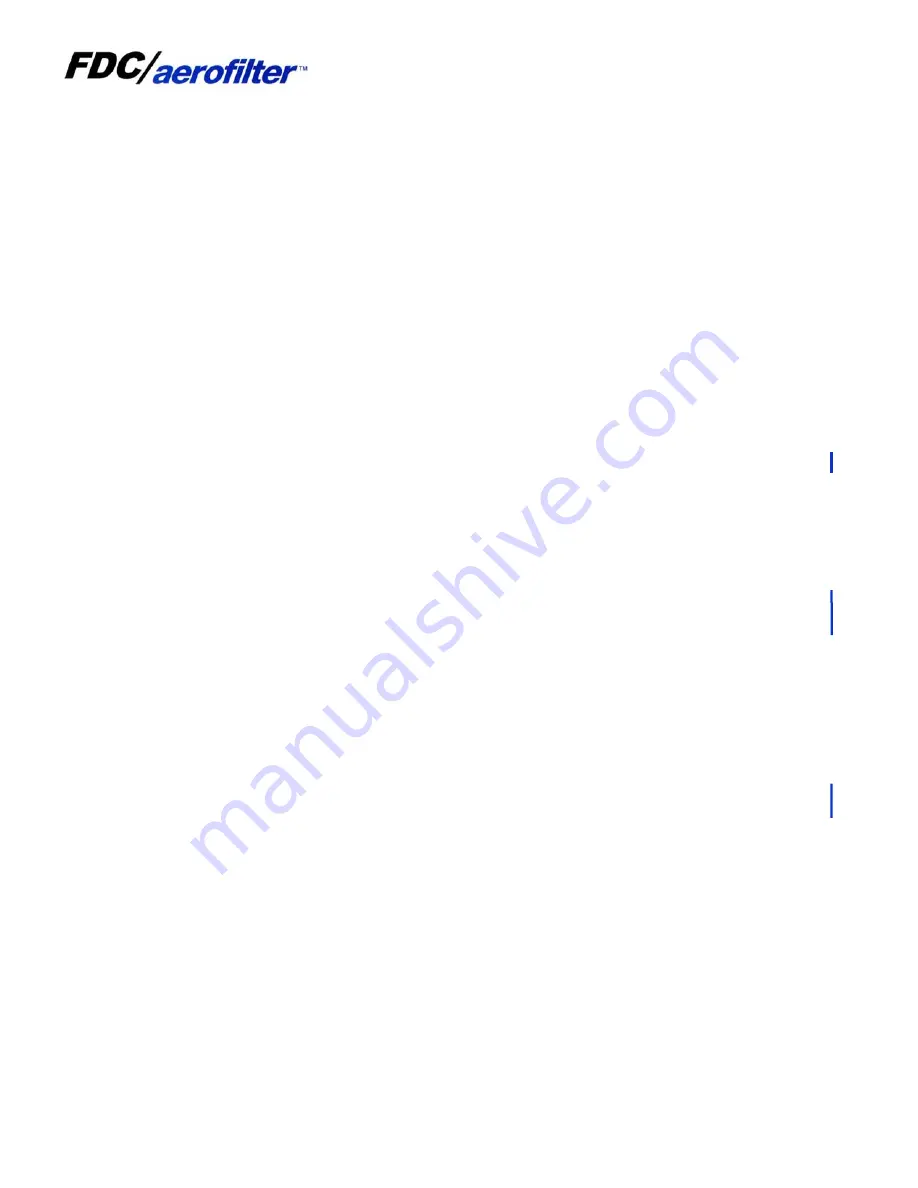
ICA
1500-SERIES-ICA-1
Revision A - 01/22/2009
Page
10
of
15
Instructions for
Continued Airworthiness
4.4 Inspection of Element (Severe Conditions)
In these conditions it may be necessary clean and inspect the elements more
frequently than recommended in Section 3. Elements used in such conditions should
be replaced if element filter media or fine mesh screen is severely degraded. They
may be cleaned and serviced as many times as required during the element life.
Regardless of the actual time in service of the elements, the physical condition of the
element, when exposed to these harsh conditions, must remain the most important
factor used to determine the serviceability of the element.
At each cleaning carefully inspect the elements as follows:
a)
Inspect the fine mesh on the forward surface of the element pleats. Complete
erosion of more than .50 in. is cause for element rejection.
b)
Inspect the course mesh on the aft surface of the element. Any evidence of
mesh wire wear or general signs of mesh breakage or deterioration are cause for
element rejection.
c)
After cleaning and before re-oiling, hold the element up to a light and check for
holes in the element material greater than .020 (it is normal to observe pinholes
in the filter media particularly at the pleat folds. These pinholes will not allow the
passage of dirt once the element is oiled). Close the holes if present using a fine
pick to reposition the media material to cover the hole. Numerous holes in the
media greater than 0.030 will reduce the filtration efficiency and are cause for
element rejection.
d)
Check the condition of the element assembly:
•
Frames for security
•
Aft element latch brackets for wear and loose rivets
•
Forward element Camloc receptacles for security and loose rivets.
Defects found are to be rectified. Consult FDC Engineering in the event any
repair cannot be performed using standard practices.
When operating in the most severe conditions it is highly recommended that an
additional serviceable, pre-oiled element be available. This will allow continued
service while the dirty element is being cleaned, inspected and re-oiled.
4.5 Inspection of Element (Normal Conditions)
At each 100 ±10 hours of operation or upon activation of the low inlet pressure warning
light:
•
Remove the elements and inspect in accordance with paragraphs
4.4 a, b, c & d
.
•
Elements should be replaced after 1500 hours in service. Service life may be
extended upon consultation with and approval of FDC Engineering.