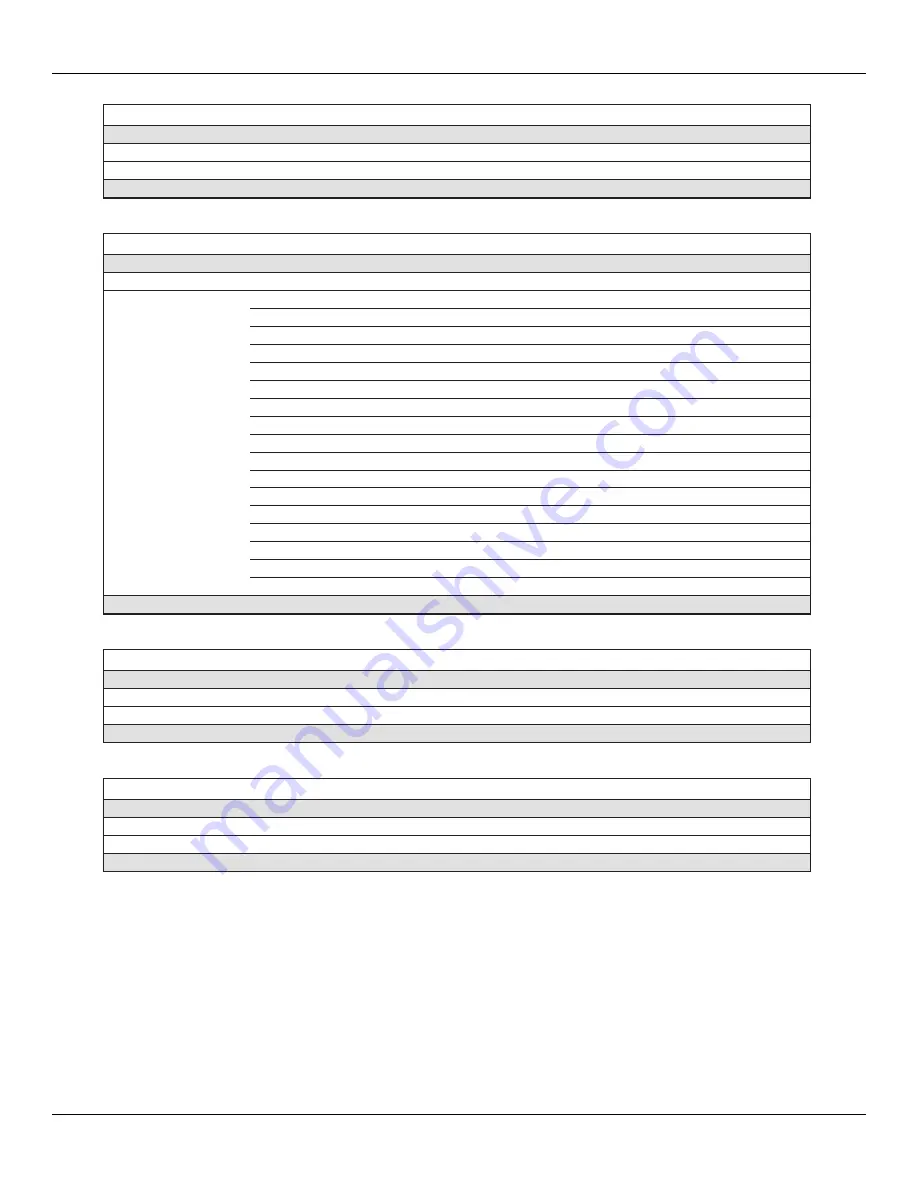
OPERATION
ST100A Series Flow Meter
64
Fluid Components International LLC
Command 20: Read Long Tag
Byte
Format
Description
Request Data Bytes
None
Response Data Bytes
0–31
Latin-1
Long Tag
Response Codes
See
, for response code list.
Command 21: Read Unique Identifier Associated with Long Tag
Byte
Format
Description
Request Data Bytes
0–31
Latin-1
Long Tag
Response Data Bytes
0
Unsigned-8
254
1–2
Enum
Expanded Device Type
3
Unsigned-8
Minimum Number Of Preambles From Master to Slave
4
Unsigned-8
HART Protocol Revision Number: 7
5
Unsigned-8
Device Revision Number
6
Unsigned-8
Software Revision Number
7
Unsigned-5
(Most Significant 5 Bits) Hardware Revision Level: 1
7
Enum
Physical Signaling Code: 00 = Bell 202 Current (4-20 mA)
8
Bits
Flags: (Unused)
9–11
Unsigned-24
Device ID
12
Unsigned-8
Minimum Number Of Preambles From Slave to Master
13
Unsigned-8
Maximum Number of Device Variables
14–15
Unsigned-16
Configuration Change Counter
16
Bits
Extended Field Device Status
17–18
Enum
Manufacturer ID Code: 166
DEC
/00A6
HEX
(FCI)
19–20
Enum
Private Label Distributor Code
21
Enum
Device Profile = 1 “HART Process Automation Device”
Response Codes
See
, for response code list.
Command 22: Write Long Tag
Byte
Format
Description
Request Data Bytes
0–31
Latin-1
Long Tag
Response Data Bytes
0–31
Latin-1
Long Tag
Response Codes
See
, for response code list.
Command 38: Reset Configuration Changed Flag
Byte
Format
Description
Request Data Bytes
0–1
Unsigned-16
Configuration Change Counter
Response Data Bytes
0–1
Unsigned-16
Configuration Change Counter
Response Codes
See
, for response code list.
Summary of Contents for ST100A Series
Page 1: ......
Page 115: ...ST100A Series Flow Meter APPENDIX A DRAWINGS Fluid Components International LLC 107 ...
Page 116: ...APPENDIX A DRAWINGS ST100A Series Flow Meter 108 Fluid Components International LLC ...
Page 117: ...ST100A Series Flow Meter APPENDIX A DRAWINGS Fluid Components International LLC 109 ...
Page 118: ...APPENDIX A DRAWINGS ST100A Series Flow Meter 110 Fluid Components International LLC ...
Page 119: ...ST100A Series Flow Meter APPENDIX A DRAWINGS Fluid Components International LLC 111 ...
Page 120: ...APPENDIX A DRAWINGS ST100A Series Flow Meter 112 Fluid Components International LLC ...
Page 121: ...ST100A Series Flow Meter APPENDIX A DRAWINGS Fluid Components International LLC 113 ...
Page 122: ...APPENDIX A DRAWINGS ST100A Series Flow Meter 114 Fluid Components International LLC ...
Page 123: ...ST100A Series Flow Meter APPENDIX A DRAWINGS Fluid Components International LLC 115 ...
Page 124: ...APPENDIX A DRAWINGS ST100A Series Flow Meter 116 Fluid Components International LLC ...
Page 125: ...ST100A Series Flow Meter APPENDIX A DRAWINGS Fluid Components International LLC 117 ...
Page 126: ...APPENDIX A DRAWINGS ST100A Series Flow Meter 118 Fluid Components International LLC ...
Page 127: ...ST100A Series Flow Meter APPENDIX A DRAWINGS Fluid Components International LLC 119 ...
Page 128: ...APPENDIX A DRAWINGS ST100A Series Flow Meter 120 Fluid Components International LLC ...
Page 129: ...ST100A Series Flow Meter APPENDIX A DRAWINGS Fluid Components International LLC 121 ...
Page 130: ...APPENDIX A DRAWINGS ST100A Series Flow Meter 122 Fluid Components International LLC ...
Page 131: ...ST100A Series Flow Meter APPENDIX A DRAWINGS Fluid Components International LLC 123 ...
Page 132: ...APPENDIX A DRAWINGS ST100A Series Flow Meter 124 Fluid Components International LLC ...
Page 133: ...ST100A Series Flow Meter APPENDIX A DRAWINGS Fluid Components International LLC 125 ...
Page 134: ...APPENDIX A DRAWINGS ST100A Series Flow Meter 126 Fluid Components International LLC ...
Page 135: ...ST100A Series Flow Meter APPENDIX A DRAWINGS Fluid Components International LLC 127 ...
Page 136: ...APPENDIX A DRAWINGS ST100A Series Flow Meter 128 Fluid Components International LLC ...
Page 137: ...ST100A Series Flow Meter APPENDIX A DRAWINGS Fluid Components International LLC 129 ...
Page 138: ...APPENDIX A DRAWINGS ST100A Series Flow Meter 130 Fluid Components International LLC ...
Page 139: ...ST100A Series Flow Meter APPENDIX A DRAWINGS Fluid Components International LLC 131 ...
Page 140: ...APPENDIX A DRAWINGS ST100A Series Flow Meter 132 Fluid Components International LLC ...
Page 141: ...ST100A Series Flow Meter APPENDIX A DRAWINGS Fluid Components International LLC 133 ...
Page 142: ...APPENDIX A DRAWINGS ST100A Series Flow Meter 134 Fluid Components International LLC ...
Page 167: ...ST100A Series Flow Meter APPENDIX E CUSTOMER SERVICE Fluid Components International LLC 159 ...
Page 168: ...APPENDIX E CUSTOMER SERVICE ST100A Series Flow Meter 160 Fluid Components International LLC ...