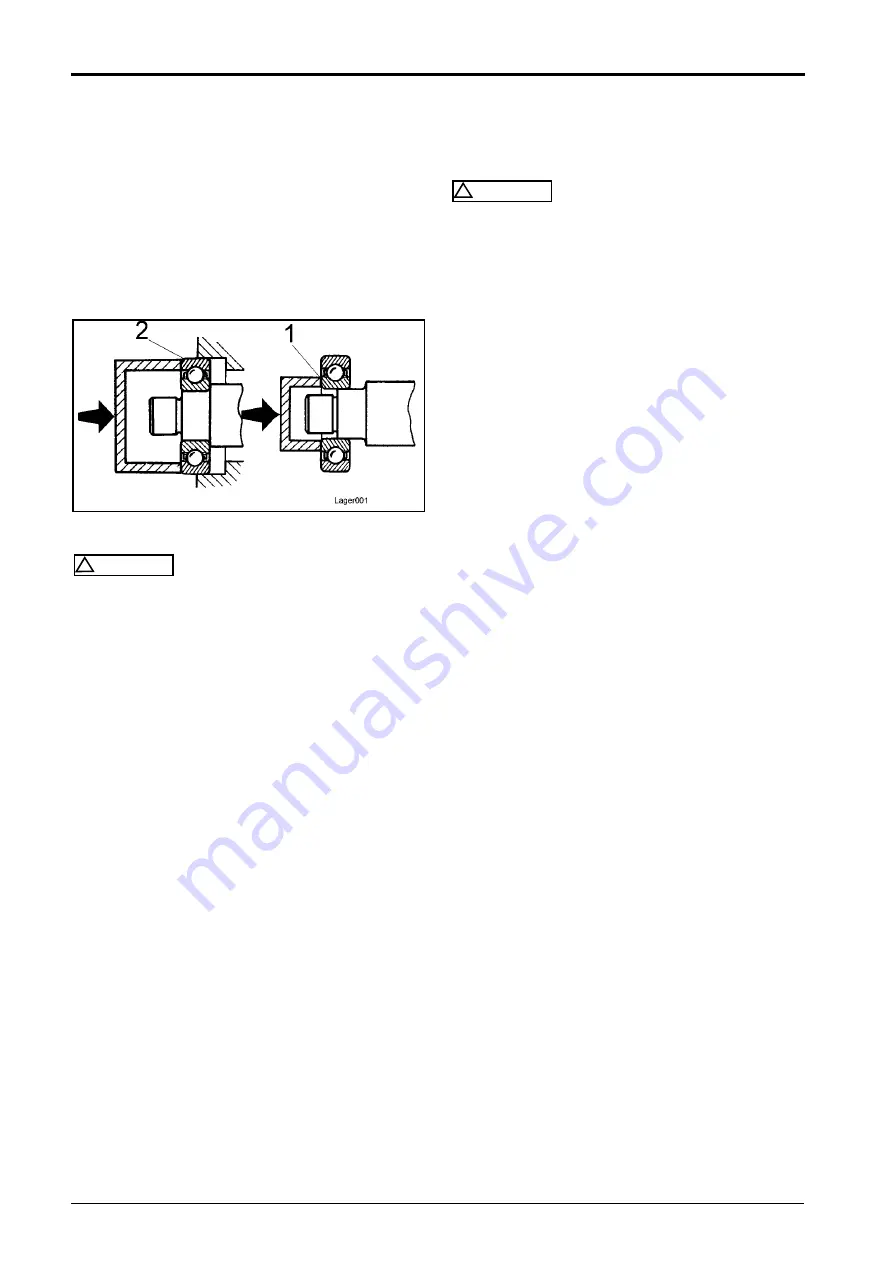
1.3
General repair instructions
BOMAG
24
008 922 89
l
Check shaft and bearing housing for discolouration
or other signs of movement between ball or roller
bearing and seats.
l
Make sure that shaft and housing are free of burrs
before assembling the ball or roller bearing.
l
Always mark the individual parts of separable ball or
roller bearings (e.g. taper roller bearings) to enable
correct reassembling. Never assemble the rollers to
an outer race that has already been used, replace
the complete ball or roller bearing instead.
Fig. 7
!
Caution
When assembling the ball or roller bearing to the
shaft load must only be applied to the inner race 1
(Fig. 7).
When fitting the bearing into the housing load
must only be applied to the outer race (2).
Screws and nuts
Tightening torque
!
Caution
Tighten nuts or screws with the tightening tor-
ques specified in the following tables of tighten-
ing torques. Tightening torques deviating from
the ones in the table are specially mentioned in
the repair instructions.
Damaged screws must under no circumstances
be used any longer. Recutting threads with thread
cutters or taps adversely affects the strength and
leak tightness of the screw joint. Damaged or cor-
roded thread pitches can cause incorrect torque
value readings.
Self-locking nuts must generally be replaced after
disassembly.
The use of screws with too high strength can
cause damage!
l
Nut of a higher strength can generally be used in-
stead of nuts of a lower strength classification.
l
When checking or retightening screw joints to the
specified tightening torque you should first relieve
by a quarter turn and then tighten to the correct
torque.
l
Before tightening you should lightly oil the thread, in
order to ensure low friction movement.
The same
applies for self-locking nuts.
l
Make sure that no oil or grease will enter into blind
tapped bores. The hydraulic power generated when
turning in the screw could cause breakage of the ef-
fected part.
Summary of Contents for BOMAG BW 27 RH-4i
Page 2: ...Find manuals at https best manuals com...
Page 7: ...BOMAG 7 008 922 89 1 General Find manuals at https best manuals com...
Page 32: ...1 4 Tightening torques BOMAG 32 008 922 89...
Page 33: ...BOMAG 33 008 922 89 2 Pneumatic tires rollers...
Page 37: ...BOMAG 37 008 922 89 3 Technical data...
Page 41: ...This as a preview PDF file from best manuals com Download full PDF manual at best manuals com...