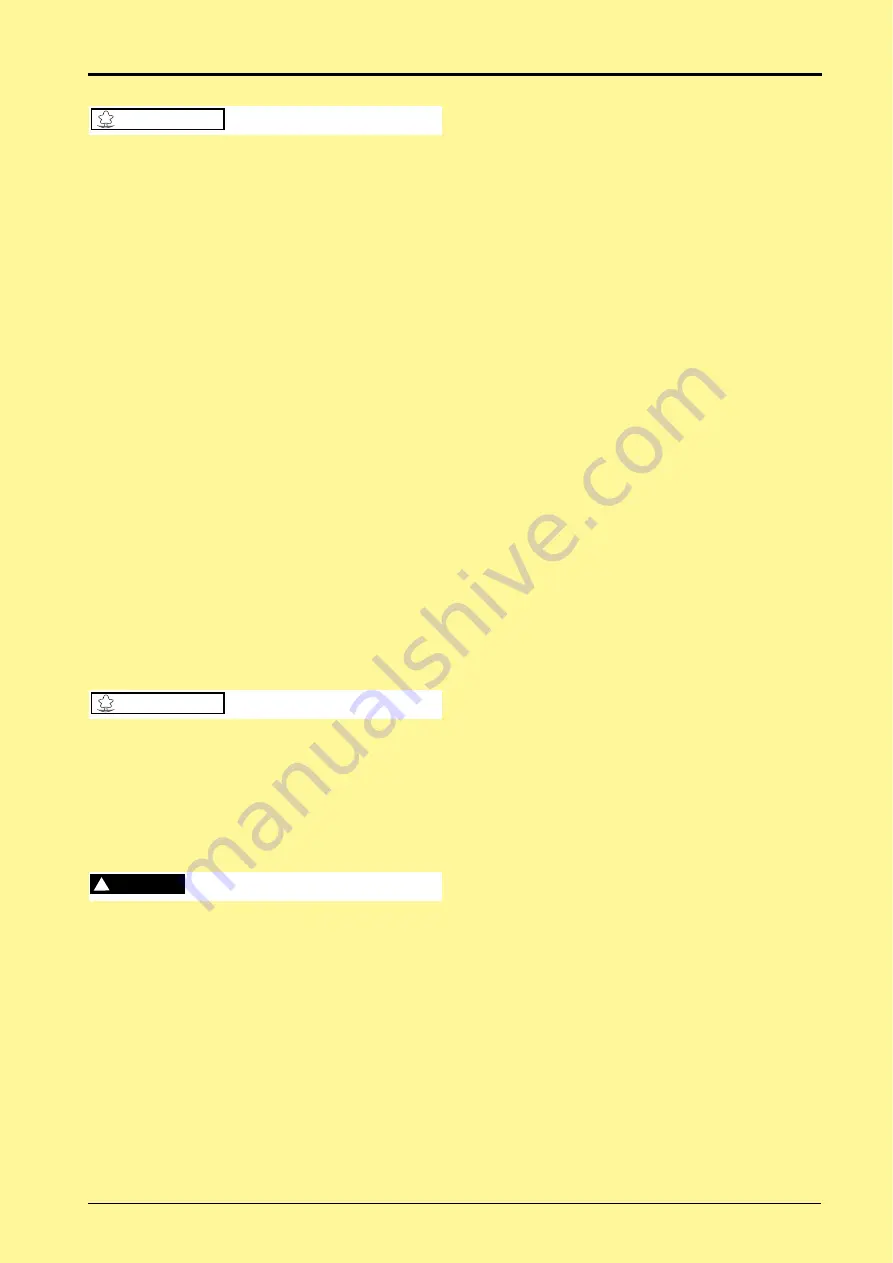
Safety regulations
BOMAG
13
008 916 89
1.2
Environment
It is strictly prohibited to drain off oil into the soil,
the sewer system or into natural waters. Old oil
must be disposed of according to applicable envi-
ronmental regulations. If in doubt you should con-
sult your local authorities.
Hydraulics
l
Always relieve the pressure in the hydraulic system
before disconnecting any lines. Hydraulic oil escap-
ing under pressure can penetrate the skin and
cause severe injury.
l
Always make sure that all screw fittings have been
tightened properly and that hoses and pipes are in
mint condition before pressurizing the system
again.
l
Hydraulic oil leaking out of a small opening can
hardly be noticed, therefore please use a piece of
cardboard or wood when checking for leaks. When
injured by hydraulic oil escaping under pressure
consult a physician immediately, as otherwise this
may cause severe infections.
l
Do not step in front of or behind the drums, wheels
or crawler tracks when performing adjustment work
in the hydraulic system while the engine is running.
Block drums, wheels or crawler tracks with wedges.
Reattach all guards and safety installations after
all work has been completed.
Environment
It is strictly prohibited to drain off oil into the soil,
the sewer system or into natural waters. Oil oil
must be disposed of according to applicable envi-
ronmental regulations. If in doubt you should con-
sult your local authorities.
Fuels
!
Danger
Repair work shall only performed by appropriately
trained personnel or by the after sales service of
BOMAG.
Follow the valid accident prevention instructions when
handling fuels.
The following notes refer to general safety precau-
tions for danger free handling of fuel.
Fuel vapours not only are easily inflammable, but also
highly explosive inside closed rooms and toxic; dilu-
tion with air creates an easily inflammable mixture.
The vapours are heavier than air and therefore sink
down to the ground. Inside a workshop they may eas-
ily become distributed by draft. Even the smallest por-
tion of spilled fuel is therefore potentially dangerous.
l
Fire extinguishers charged with FOAM, CO
2
GAS
or POWDER must be available wherever fuel is
stored, filled in, drained off, or where work on fuel
systems is performed.
l
The vehicle battery must always be disconnected,
BEFORE work in the fuel system is started. Do not
disconnect the battery while working on the fuel
system. Sparks could cause explosion of the fuel
fumes.
l
Wherever fuel is stored, filled, drained off or where
work on fuel systems is carried out, all potential ig-
nition sources must be extinguished or removed.
Search lights must be fire proof and well protected
against possible contact with running out fuel.
Hot fuels
Please apply the following measures before draining
of fuel to prepare for repair work:
l
Allow the fuel to cool down, to prevent any contact
with a hot fluid.
l
Vent the system, by removing the filler cap in a well
ventilated area. Screw the filler cap back on, until
the tank is finally emptied.
Synthetic rubber
Many O-rings, hoses, etc. are made of synthetic ma-
terial, a so-called fluorocarbon elastomer. Under nor-
mal operating conditions this material is safe and does
not impose any danger to health.
However, if this material becomes damaged by fire or
extreme heat, it may decompose and form highly
caustic hydrofluoric acid, which can cause severe
burns in contact with skin.
l
If the material is in such a state it must only be
touched with special protective gloves. The protec-
tive gloves must be disposed of according to appli-
cable environmental regulations immediately after
use.
l
If the material has contacted the skin despite these
measures, take off the soiled clothes and seek
medical advice immediately. In the meantime cool
and wash the affected area of skin over a sufficient
time with cold water or lime water.
Poisonous substances
Some of the fluids and substances used are toxic and
must under no circumstances be consumed.
Skin contact, especially with open wounds, must be
avoided.
These fluids and substances are, amongst others,
anti-freeze agents, hydraulic oils, fuels, washing addi-
tives, refrigerants, lubricants and various bonding
agents.
Summary of Contents for BOMAG BW 226 DH-4
Page 2: ...Find manuals at https best manuals com...
Page 8: ...Table of Contents BOMAG 8 008 916 89 Find manuals at https best manuals com...
Page 9: ...BOMAG 9 008 916 89 1 General Find manuals at https best manuals com...
Page 34: ...1 4 Tightening torques BOMAG 34 008 916 89...
Page 35: ...BOMAG 35 008 916 89 2 BOMAG single drum rollers...
Page 42: ...2 1 BOMAG single drum rollers BOMAG 42 008 916 89...
Page 43: ...BOMAG 43 008 916 89 3 Technical data...
Page 48: ...3 1 Technical data BOMAG 48 008 916 89...
Page 49: ...BOMAG 49 008 916 89 4 Maintenance...
Page 51: ...This as a preview PDF file from best manuals com Download full PDF manual at best manuals com...