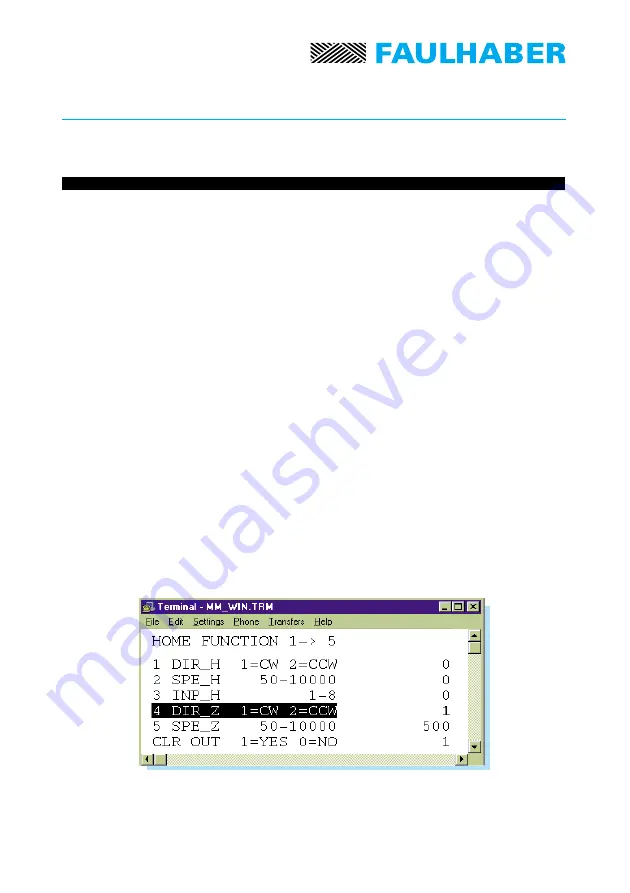
25
Specifications subject to change without notice
Program example
Description of the application
For this example, using the MCBL 3603 we want to control the rotation of the Brushless
DC-Servomotor type 3564 K 024 B. The speed and position are measured by the HEDS 5540
(2 channel, 500 lines with Z index) encoder.
The motor shaft should make 5 CW rotations (a total of 1’800
°
) in 5 seconds at a maximum
speed of 61.5 rpm. Once the 5 rotations have been completed, the motor should stop for 2
seconds and then make 3 CCW rotations in 0.5 seconds at a maximum speed of 450 rpm.
The second displacement is performed using both relative and absolute positioning.
The home (starting) position is defined using the encoder Z index.
Input sequence
This particular sequence can be subdivided into four distinct phases:
•
Starting position
(home)
•
First displacement
(index 1)
•
Waiting time
WT
•
Second displacement
(index 2)
How to enter the program data
It is important to remember that the motion controller works using the encoder line
information. In other words, the displacement/movement, speed and acceleration
parameters are entered in lines, lines/second and lines/second
2
respectively.
As already indicated, the motion controller’s internal electronics multiply the encoder
resolutions by 4.
The first step is to define the parameters of the various separate phases.
Definition of the home (starting) position
This instruction is given via the HOME FUNCTION menu
If, as in this case, the home function is executed using the encoder Z index, the first 3 lines
are set at zero as above. In this example, the Z index is found by rotating the motor shaft
CW at a speed of 125 lines/second. Once this position has been reached, all outputs are
cleared.
13. Typical program example