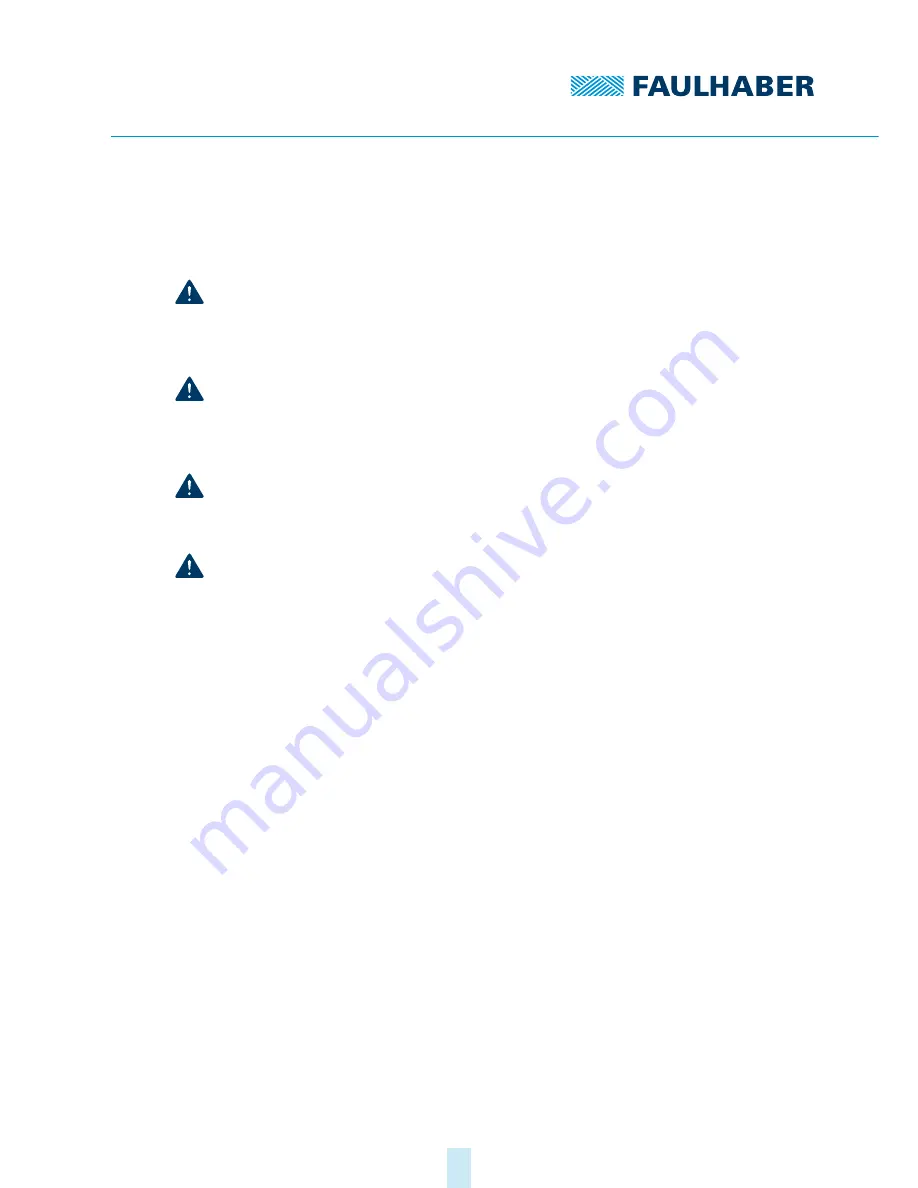
3rd edition, 6-11-2017
7000.05057, 3rd edition, 6-11-2017
7000.05057
Installation
20
4.2
Electrical connection
4.2.1
Instructions for the electrical connection
NOTICE!
Electrostatic discharges to the Motion Controller connections can damage the electronic
components
Observe the ESD protective measures.
NOTICE!
Electrostatic discharges to the Speed Controller connections can damage the electronic
components
Observe the ESD protective measures.
NOTICE!
Incorrect connection of the wires can damage the electronic components.
Connect the wires as shown in the connection assignment.
NOTICE!
A short-term voltage peak during braking can damage the power supply or other con-
nected devices.
For applications with high load inertia, the FAULHABER Braking Chopper of the BC
5004 series can be used to limit overvoltages and thereby protect the power supply. For
more detailed information see the data sheet for the Braking Chopper.
The Motion Controller contains a PWM output stage for controlling the motors. Power
losses arising during operation and alternating electrical fields arising due to the pulsed
control of the motors, must be dissipated and damped by appropriate installation.
Connect the Motion Controller to a grounding system. This should be done preferably
by mounting it on an earthed baseplate, or alternatively by connecting it to an earthed
mounting rail.
Make sure that potential equalisation is present between all coupled parts of the sys-
tem. This applies even if the Motion Controller and motor are mounted separately.
If several electrical devices or controllers are networked by means of RS232 or CAN,
make sure that the potential difference between the earth potentials of the various
parts of the system is less than 2 V.
The cross-section of the required potential equalisation conductors between the various
parts of the system is specified in VDE 100 and must satisfy the following conditions:
At least 6 mm
2
Larger than half the cross-section of the supply conductor