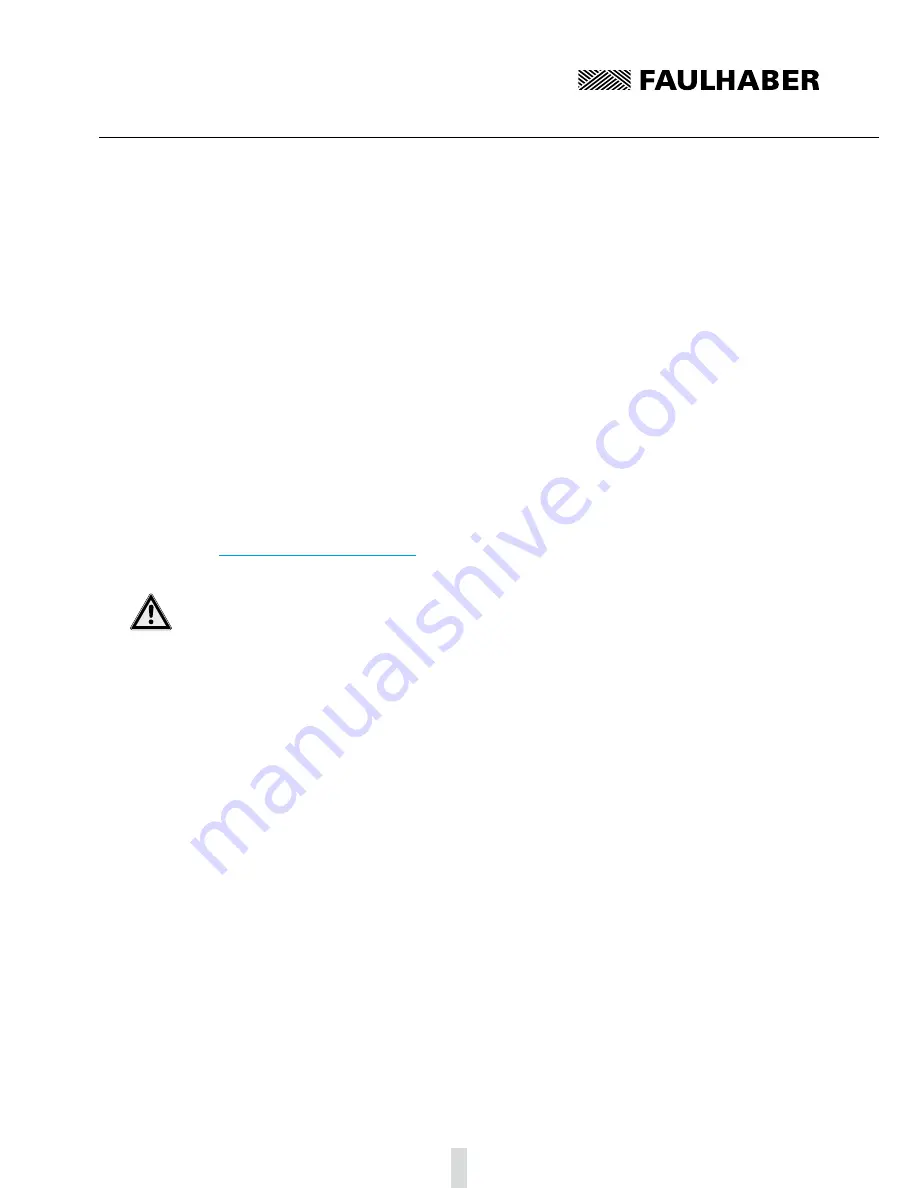
28
Functional Description
4
Motor with SC speed controller
4.3
PWM operation
If Untarget is specified as the voltage at the motor it is operated with speed control. The speed is
controlled by pulse width modulation (PWM), i.e. the motor tries to achieve a constant speed under
fluctuating load.
Due to the technical requirements of the motor with SC speed controller, assuming the allowable
maximum housing temperature is adhered to, the maximum possible continuous torque in PWM
mode may be lower than under full control. The maximum thermally allowable continuous current
reduces accordingly.
4.3.2 Configuration
The control parameters of the speed controller integrated in the motor can be individually adjusted
to the respective application via a PC. This requires a programming adapter which can be ordered se-
parately as well as a version of the FAULHABER Motion Manager PC software suitable for the speed
controller.
The software is available on request or from the FAULHABER homepage
http://www.faulhaber-group.com
.
CAUTION!
Risk of damage
Before starting up, check the parameters configured in the control and if necessary adjust to the con-
nected motor. Incorrectly set values can cause fatal damage to the motor and / or the speed controller.
In particular, the following parameters must be correctly set:
Duration and maximum current value,
Generator voltage constant k
E
and connected resistance R,
Controller parameter.
The servomotor is equipped with digital Hall sensors, with which the commutation signals can be
determined. The actual speed value is determined via the time interval between the edges of the
hall sensor signals.
Preset default basic parameters:
Due to the resolution of the digital hall sensors, speeds from approx. 250 rpm can be stably
controlled.
PWM frequency at the power output stage: approx. 96 kHz.
2-quadrant operation with function for quick speed reduction: The motor windings are short-
circuited for faster transition from higher to lower speeds.