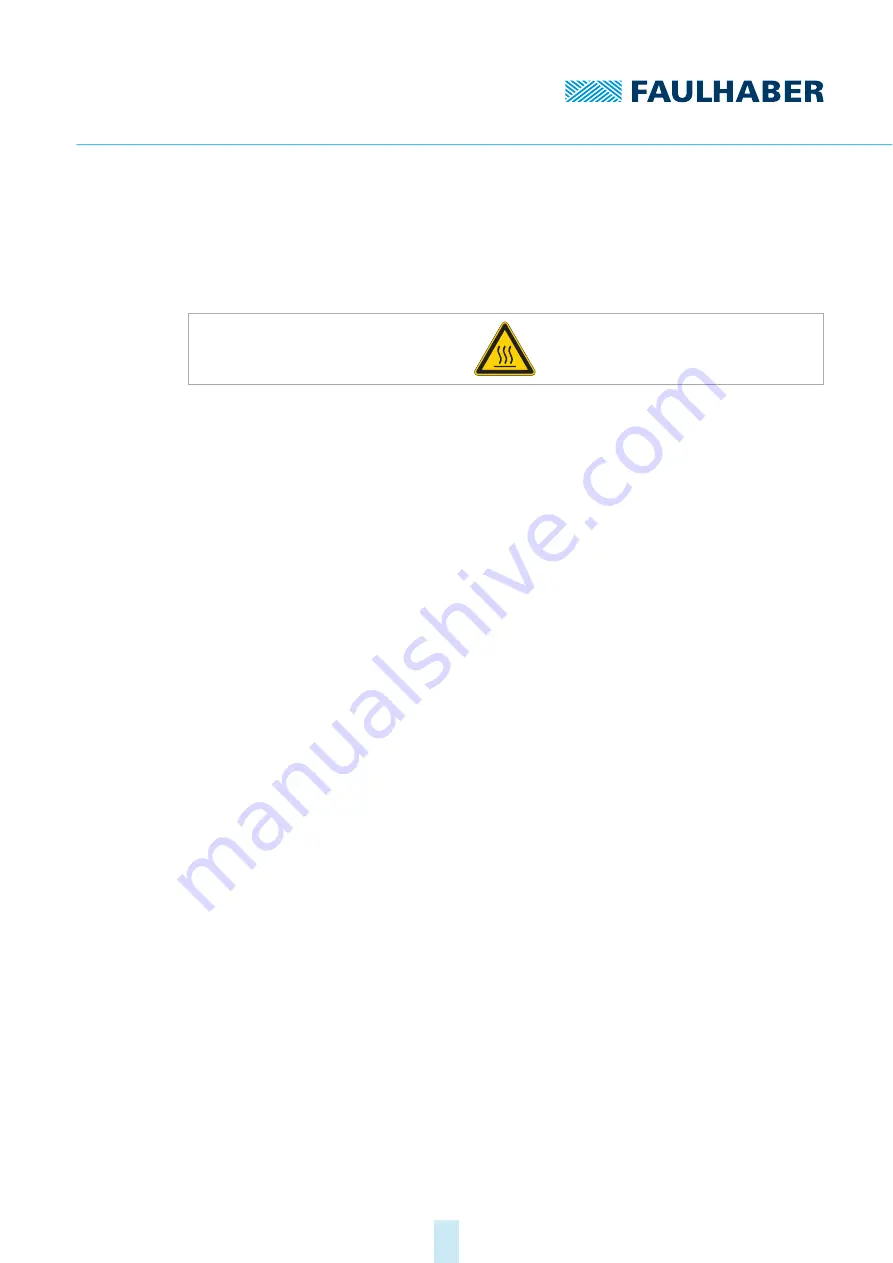
1st edition, 9.04.2024
7000.05073, 1st edition, 9.04.2024
7000.05073
Safety
10
2.2.3
Heat development
Active components may cause the MCS to heat up. If touched, there is a risk of burning.
Protect the MCS against being touched and cool sufficiently.
If necessary, affix a suitable warning sign in the immediate vicinity of the MCS.
Fig. 1:
Suitable warning sign acc. to DIN EN ISO 7010
2.3
Environmental conditions
Select the installation location so that clean dry air is available for cooling the MCS.
Select the installation location so that the air has unobstructed access to flow around
the MCS.
When installed within housings and cabinets take particular care to ensure adequate
cooling of the MCS.
Select a power supply that is within the defined tolerance range.
Protect the MCS against heavy deposits of dust, in particular metal dust and chemical
pollutants.
Protect the MCS against humidity and wet.
Summary of Contents for 2232 BX4 IMC
Page 1: ...WE CREATE MOTION Technical Manual Motion Control System MCS 2232 BX4 IMC 2250 BX4 IMC EN...
Page 38: ...1st edition 9 04 2024 7000 05073 1st edition 9 04 20247000 05073 Additional documents 38...
Page 39: ...1st edition 9 04 2024 7000 05073 1st edition 9 04 20247000 05073 Additional documents 39...