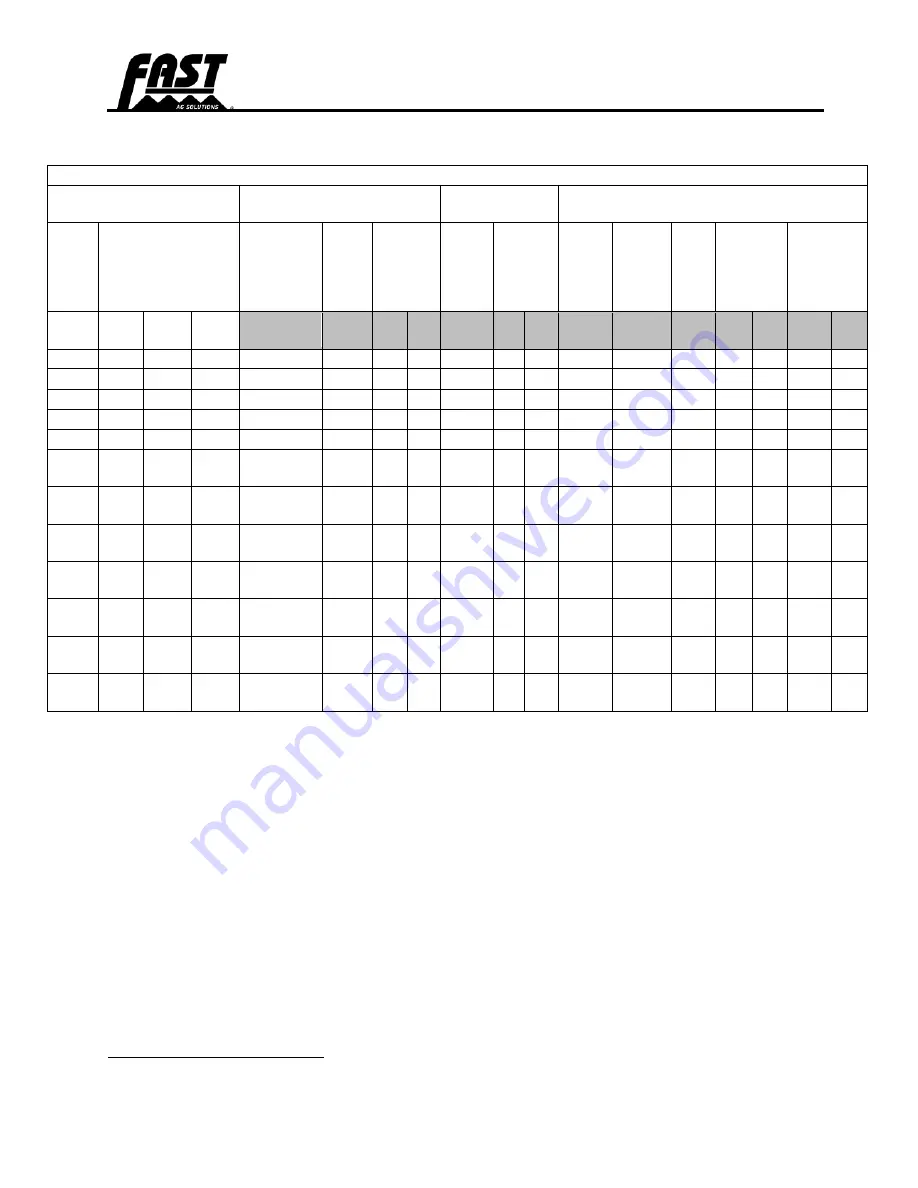
TIGHTENING HARDWARE
TIGHTENING HARDWARE Dry DuraPlacer 9 / 13 / 14 Ton - 40' / 60'
Page 58
SAE Face Seal and O-Ring Stud End Fitting Torque Chart
SAE Face Seal and O-Ring Stud End Fitting Torque Chart - Standard Pressure-Below 27.6 MPA (4,000 PSI)
Nominal Tube OD
Hose ID
O-Ring Face Seal/
Tube Swivel Nut
Bulkhead Jam
Nut Torque
O-Ring Straight, Adjustable, and External
Port Plug Stud Ends
6
Metric
Tube
OD
Inch Tube OD
Thread
Size
Swivel
Nut
Hex
Size
Tube Nut
Swivel
Nut
Torque
Jam
Nut
Hex
Size
Jam Nut
Torque
Thread
Size
Straight
Hex
Size
7
Adj
Lock
Nut
Hex
Size
Steel or
Gray Iron
Torque
Aluminum
or Brass
Torque
8
mm
Dash
Size
in.
mm
in.
in.
N-m
lb.-
ft
N-
m
lb.-
ft
in.
in.
in.
N-m
lb.-
ft
N-m
lb.-ft
5
-3
0.188
4.78
—
—
—
—
—
—
—
3/8-24
5/8
9/16
12
9
8
6
6
-4
0.250
6.35
9/16-18
11/16
16
12
13/16
32
24
7/16-20
5/8
5/8
16
12
11
8
8
-5
0.312
7.92
—
—
—
—
—
—
—
1/2-20
3/4
11/16
24
18
16
12
10
-6
0.375
9.53
11/16-16
13/16
24
18
1
42
31
9/16-18
3/4
3/4
37
27
25
18
12
-8
0.500
12.70
13/16-16
15/16
50
37
1-1/8
93
69
3/4-16
7/8
15/16
50
37
33
25
16
-10
0.625
15.88
1-14
1-1/8
69
51
1-5/16
118
87
7/8-14
1-1/16
1-
1/16
69
51
46
34
20
-12
0.750
19.05
13/16-12
1-3/8
102
75
1-1/2
175
129
11/16-
12
1-1/4
1-3/8
102
75
68
50
22
-14
0.875
22.23
13/16-12
—
102
75
—
175
129
13/16-
12
1-3/8
1-1/2
122
90
81
60
25
-16
1.000
25.40
17/16-12
1-5/8
142
105
1-3/4
247
182
15/16-
12
1-1/2
1-5/8
142
105
95
70
32
-20
1.25
31.75
1-11/16-12
1-7/8
190
140
2
328
242
1-5/8-
12
1-3/4
1-7/8
190
140
127
93
38
-24
1.50
38.10
2-12
2-1/4
217
160
2-3/8
374
276
1-7/8-
12
2-1/8
2-1/8
217
160
145
107
50.8
-32
2.000
50.80
—
—
—
—
—
—
—
2-1/2-
12
2-3/4
2-3/4
311
229
207
153
6
Tolerance is +15%/-20% of mean tightening torque unless otherwise specified.
7
The straight hex wrench sizes listed apply to connectors only and may not be the same as the
corresponding plug of the same thread size.
8
These torques were established using steel plated connectors in aluminum and brass.
Summary of Contents for DP9D
Page 1: ...DP9D DP13D DP14D 40 60 OWNERS MANUAL DRY DURAPLACER OWNERS MANUAL 2023...
Page 2: ...820070 Dry DuraPlacer 9 13 14 Ton 40 60 2023 09 27...
Page 7: ...Dry DuraPlacer DP9D DP13D DP14D Page v...
Page 29: ...SAFETY SAFETY Dry DuraPlacer 9 13 14 Ton 40 60 Page 13 Wing C B A A C B A B A B...
Page 30: ...SAFETY SAFETY Dry DuraPlacer 9 13 14 Ton 40 60 Page 14 Main Frame Wheel and Tracks...