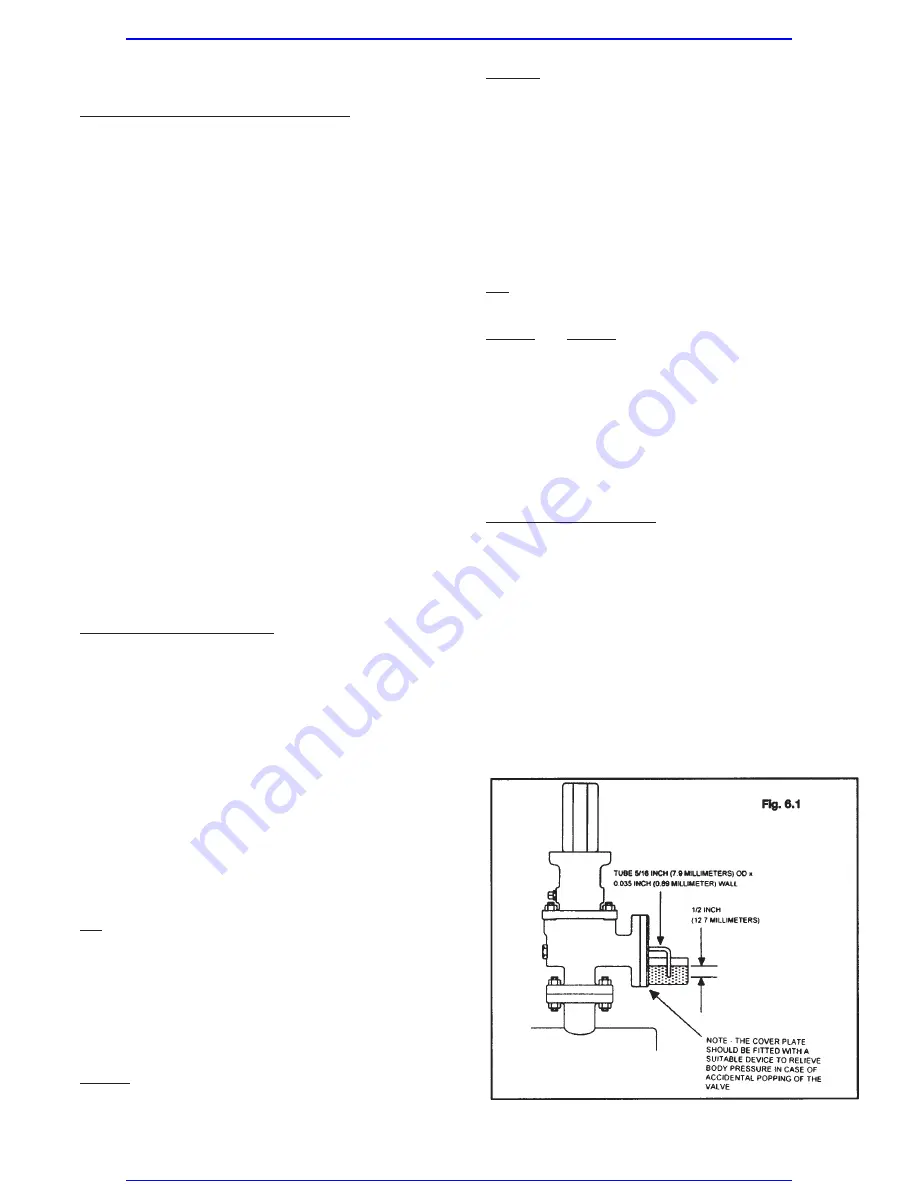
WATER - Before starting the seat tightness test, the outlet
body bowl shall be filled with water, and the valve shall be
allowed to stabilize with no visible flow from the valve out-
let. The valve shall be observed for 1 minute at the test
pressure. There shall be no visible leakage at the valve
outlet.
Soft Seated Valves:
Soft seated valves shall be tested at 95% of set pressure
when set above 100 psig; they shall be tested at 5 psig
below set pressure when the set pressure is less than or
equal to 100 psig.
AIR - There shall be no leakage (zero bubbles) using the
test method outlined above.
STEAM and WATER - There shall be no visible leakage at
the valve outlet.
2. If any valve fails to meet leakage requirements, it shall
be reworked.
3. Assemble appropriate cap construction after leak tight-
ness has been verified. If valve type is open lever, no
back pressure test is required. Plain cap and packed
lever valves must be back pressure tested as outlined
in the next section.
BACK PRESSURE TEST
1. This test applies to all valves designed for discharge to
a closed system (plain or packed lever cap construc-
tion) with inlet sizes larger than 1 nps.
2. The secondary pressure zone of the valve shall be test-
ed with air or other suitable gas at a pressure of at least
30 psi. The valve should be pressurized at the outlet
with shop air or other means. A soap solution or other
suitable solution shall be applied to all connections
which are potential leakage paths (i.e., body/bonnet
connection, cap/bonnet connection, packed lever
assembly/cap connection). No leakage is acceptable.
3. If leakage is detected at any location, the valve shall be
reworked.
6. Setting & Testing
TESTING AND SETTING PROCEDURE
1. Mount the valve on the test stand. Use air as the test
medium for air, gas and vapor or flashing service appli-
cations. Set valves for saturated steam service on satu-
rated steam. Valves for steam service set with air
should include temperature compensation. The name-
plate provides “Cold Differential Test Pressure.” Set
valves for liquid service on water.
2. Hold the stem tightly and tighten (turn clockwise) the
spring adjusting screw to increase the spring force.
Make sure the stem does not rotate while loading the
spring.
3. Slowly raise the test drum pressure and observe the
opening point. The set pressure on air or steam is the
“pop point” while on water it is the first continuous flow.
4. If necessary reduce the test drum pressure and adjust
the spring adjusting screw. Repeat this until the valve
opens at the required pressure, designated as “Cold
Differential Test Pressure.” At the desired setting, torque
the jam nut to 25 ft. lbs. and assemble cap and gasket
for tightness testing. Check set point once more after
locking jam nut.
Never adjust the spring setting when the pressure
under the valve is near its popping point, as the body
seat and disc seat might score and/or gall. Always
lower the pressure in the valve at least 25 percent
below popping pressure before making adjustments.
This will put a loading on the seat surfaces, and pre-
vent rotation and damage.
SEAT TIGHTNESS TESTING
WARNING:
The valve must be checked for seat leak-
age after the set pressure has been checked. Excessive
leakage could lead to fouled or inoperable valves, serious
product loss and could be hazardous to personnel and
equipment.
1. The valve can be tested for tightness on the test stand
by increasing vessel pressure to the required test pres-
sure and observing the valve outlet for evidence of
leakage. The following is an overview of the test proce-
dures used.
Metal Seated Valves:
Metal seated valves shall be tested at 90% of set pressure
when the set pressure is greater than 50 psig; they shall
be tested at 5 psig below set pressure when the set pres-
sure is less than or equal to 50 psig.
AIR - A 5/16 O.D. x 0.035 wall thickness copper tube or
equivalent immersed no more than 1/2 deep in water shall
be connected to the valve outlet. See Figure 6.1. Seal all
other potential leakage paths with suitable fixtures (i.e.,
cap, plugs) so that seat leakage can be detected at the
outlet. Before starting the bubble count, test pressure shall
be applied for a minimum of 1 minute. The valve shall then
be observed for leakage for at least 1 minute. The leakage
rate shall not exceed 40 bubbles per minute.
STEAM - Test pressure shall be applied for 3 minutes
before the seat tightness test. The valve shall be observed
for leakage for at least 1 minute. There shall be no visible
or audible leakage at the valve outlet.
7
▲
!
Visit www.boighill.com to request a quote.
Visit www.boighill.com to request a quote.