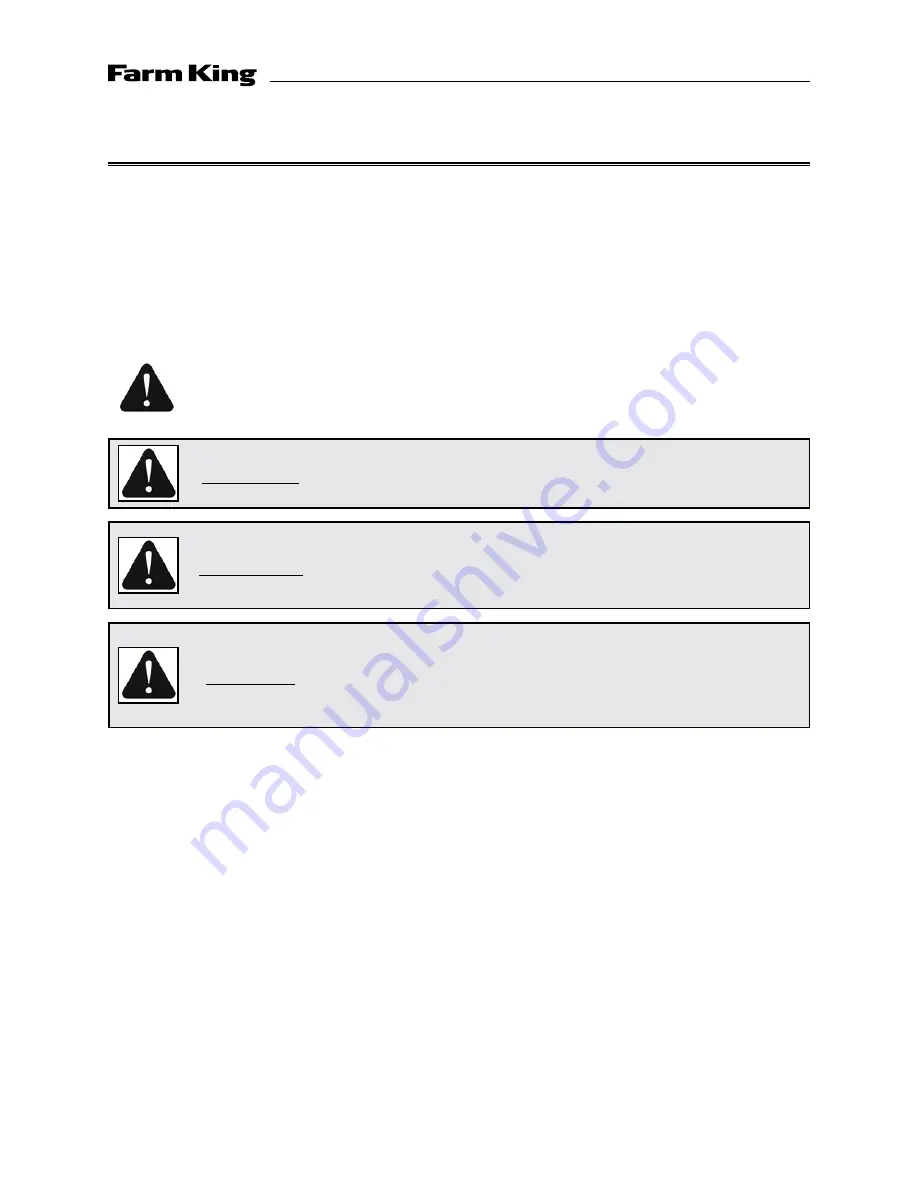
6
Safety - 45 Series Rotary Tiller
Safety
Safety Instructions
Remember, YOU are the key to safety. Good safety practices not only protect you, but also the
people around you. Make these practices a working part of your safety program. Be certain that
everyone operating this equipment is familiar with the recommended operating and maintenance
procedures and follows all the safety precautions. Most accidents can be prevented. Do not risk
injury or death by ignoring good safety practices.
The alert symbol is used throughout this manual. It indicates attention is required and identifies
hazards. Follow the recommended precautions.
The safety alert symbol means…
ATTENTION! BECOME ALERT! YOUR SAFETY IS INVOLVED!
CAUTION
The caution symbol indicates a potentially hazardous situation
that, if not avoided, may result in minor or moderate injury. It
may also be used to alert against unsafe practices.
WARNING
The Warning Symbol indicates a potentially hazardous situation
that, if not avoided, could result in death or serious injury, and
includes hazards that are exposed when guards are removed. It
may also be used to alert against unsafe practices.
DANGER
The Danger Symbol indicates an imminently hazardous situation
that, if not avoided will result in death or serious injury. This
signal word is to be limited to the most extreme situations,
typically for machine components that, for functional purposes,
cannot be guarded.
Summary of Contents for 45 Series
Page 1: ...Operator and Parts Manual 092010 FK366 RotaryTiller 45 Series 60 72 ...
Page 2: ......
Page 20: ...20 Operation 45 Series RotaryTiller Theory of Operation ...
Page 29: ...29 Parts 45 Series RotaryTiller 45 Series RotaryTiller Assembly Drawings ...
Page 30: ...30 Parts 45 Series RotaryTiller ...
Page 34: ...34 Parts 45 Series RotaryTiller PTO Assembly Drawing ...
Page 41: ......