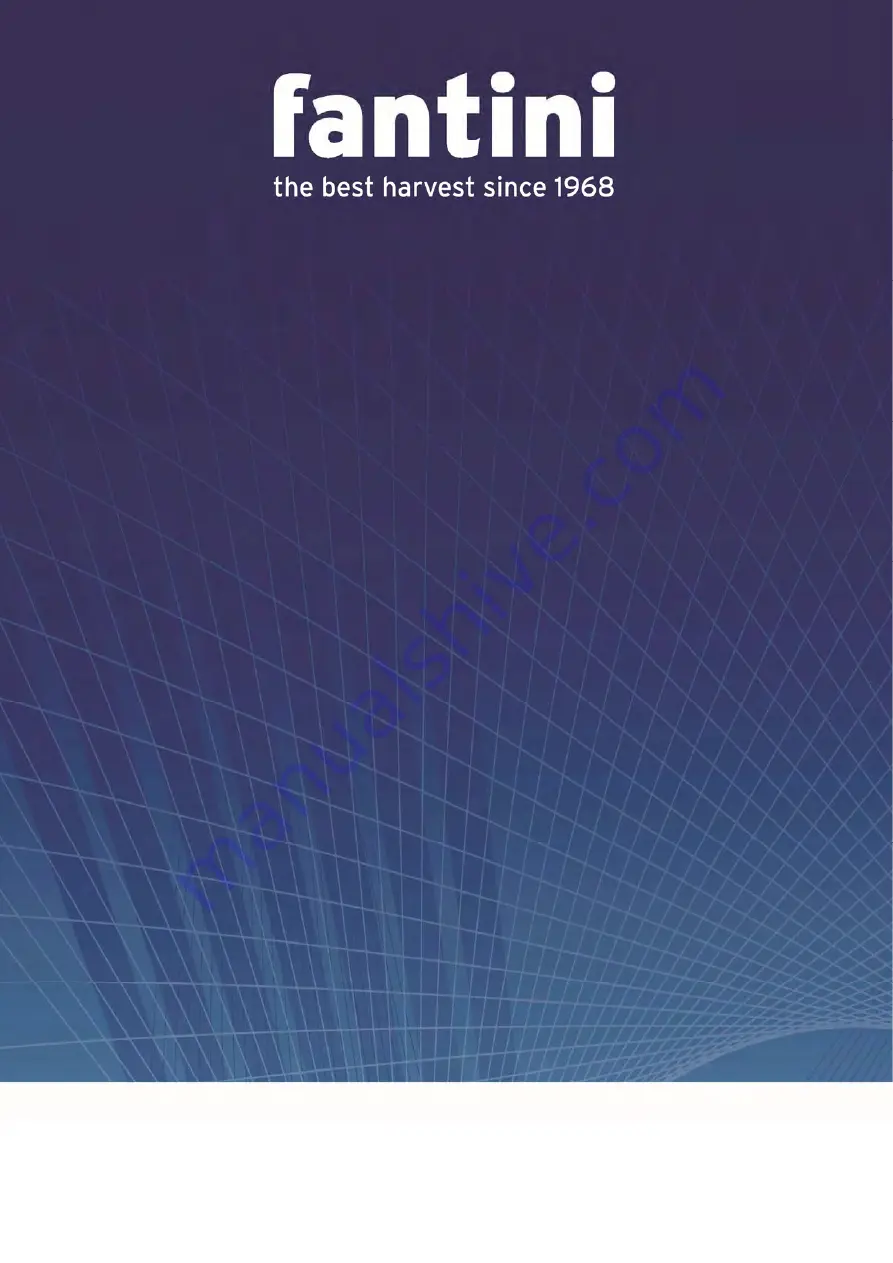
Use and maintenance manual for fixed or folding corn harvesting header
EDITION 01/2016
1
USE AND MAINTENANCE
MANUAL
CORN HEADER
L03 – LH3
Read
this
manual
carefully
and
thoroughly
before
the
use
and
maintenance
operations
of
your
header.
Store
the
manual
in
a
safe
and
secure
place
for
future
reference.
For
any
question
related
to
this
manual
contact
your
distributor
or
visit
the
website:
www.fantini
-na
.com
FANTINI
NORTH AMERICA
15526 90th Street NE
Drayton, ND 58225
P 1-800-454-3875