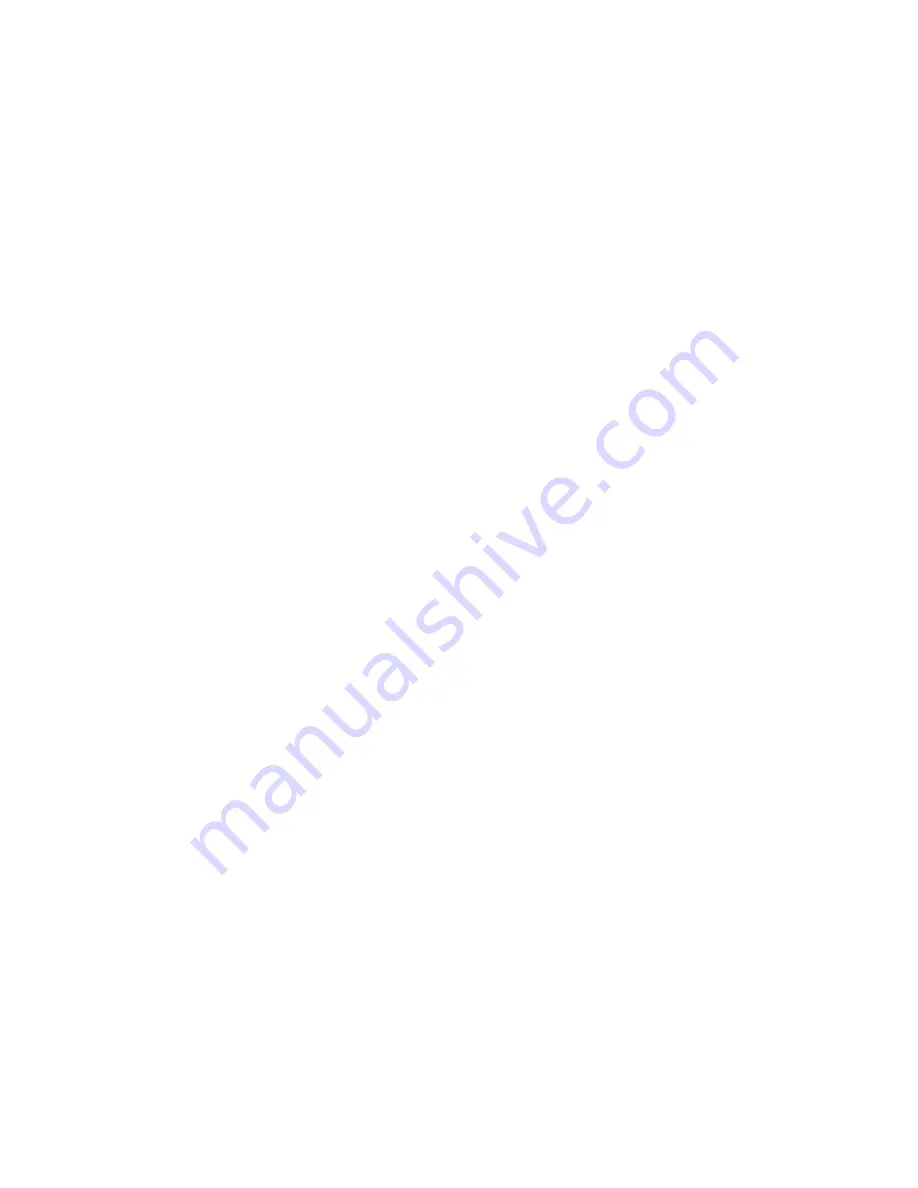
22
B.
Safety Considerations of Pressure Systems
Safe operation of pressurized equipment requires the pressurizing system be properly maintained.
Specific procedures for the safe use of pressure regulators are listed below:
1. Never subject a regulator to inlet pressure greater than its rated inlet pressure, as shown on
the regulator body.
2. Never use the regulator for gases other than those for which it is intended.
3. All connections to the regulator must be clean. Remove oil, grease, or other contaminants
from external surfaces of the regulator and metal connecting parts.
4. Before attaching regulator to the cylinder, remove any dirt or foreign matter that may be in the
cylinder valve outlet by wiping with a clean, lint free cloth.
CAUTION
THE VALVE ON THE CYLINDER MAY BE OPENED MOMENTARILY TO
BLOW THE OUTLET CLEAN. MAKE SURE THE CYLINDER OPENING
IS POINTED AWAY.
5. Never pressurize a regulator that has loose or damaged parts or is in questionable condition.
Never loosen or attempt to tighten a connection or a part until the gas pressure has been
relieved. Under pressure, gas can dangerously propel a loose part.
6. Before transporting gas cylinders remove regulator and recap cylinder.
7. Keep cylinder hand wheel or wrench on open cylinder valve at all times, for prompt emergency
cutoff.
8. Check regulator and all connections for leaks after installation, periodically thereafter, and
after any service in which parts or connections were disconnected and reconnected, using a
soap solution around fittings to find small leaks. Bubbles will indicate a leak.
C.
Regulator Troubleshooting
The primary causes of regulator problems are leaking fittings or faulty pins and seats.
Rarely does a diaphragm rupture. If a regulator will not hold pressure:
1. Check for leakage around fittings.
Pressure the system and look for escaping gas in the form of bubbles. This can be
done by applying soap suds to the possible leak area, or the regulator assembly,
except for the gauge, may be submerged in water. Repair by dis-assembling and
applying tape thread sealant.
2. A faulty pin and seat will usually be evidenced by leakage through the regulator to
the down stream side as opposed to external leakage. Check for bubbles coming
out of the regulator when it is supposed to be shut off.
3. Dirt or sample contamination in regulator.