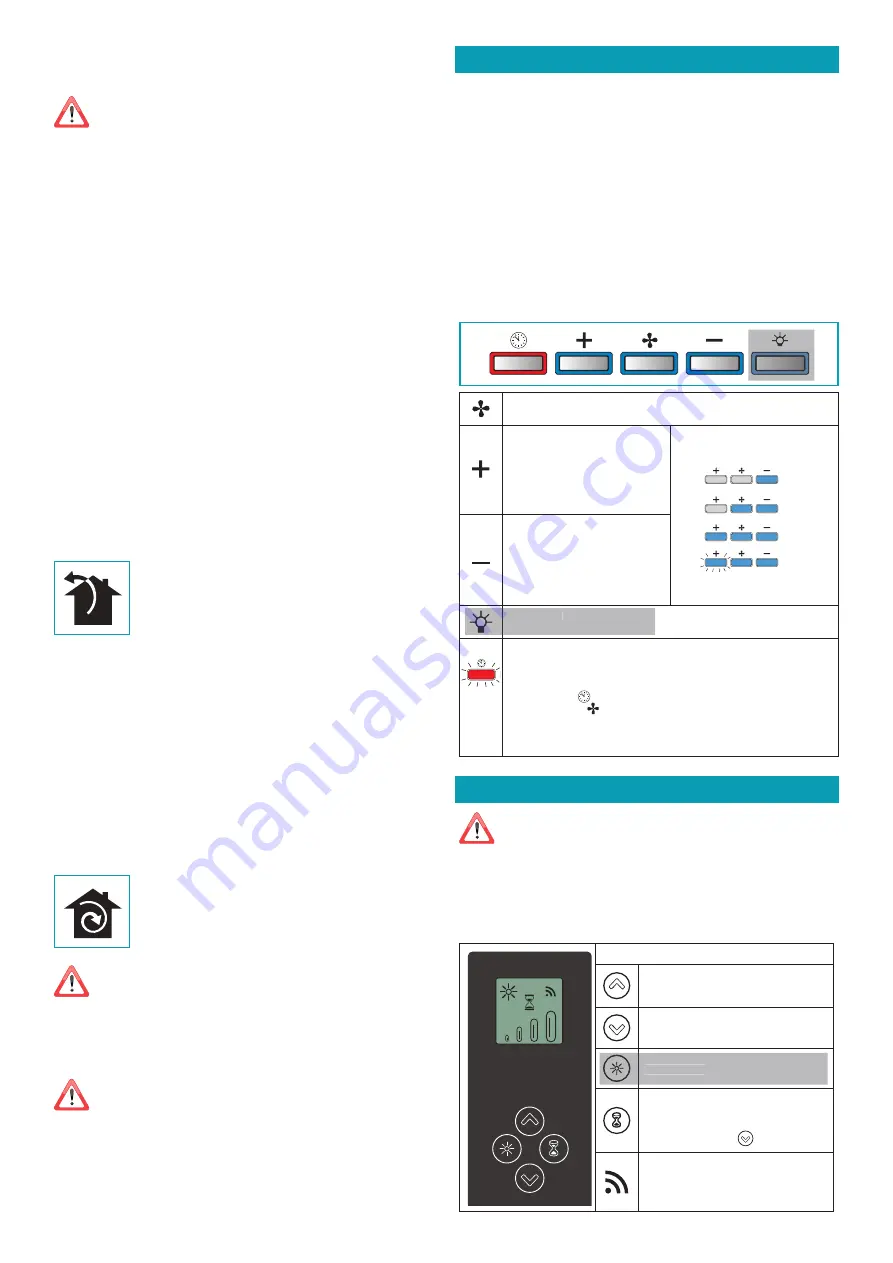
27
ELECTRICAL CONNECTION
(only intended for qualii ed personnel)
Disconnect the equipment from electrical mains power supply before carry-
ing out any operations on the hood.
Ensure that the wires inside the hood are not disconnected or cut:
in the event of damage, contact your nearest Servicing Department.
Refer to qualii ed personnel for electrical connections.
Connection must be carried out in compliance with the provisions of law in force.
Before connecting the hood to the electrical mains power supply, check that:
• voltage supply corresponds with what is reported on the data plate located inside the
hood;
• the electrical system is compliant and can withstand the load (see the technical specii -
cations located inside the hood);
• the power supply plug and cable do not come into contact with temperatures exceed-
ing 70 °C;
• the power supply system is ef ectively and properly connected to earth in compliance
with regulations in force;
• the socket used to connect the hood is within reach.
In case of:
• devices i tted with cables without a plug: the type of plug to use is a ''standardised'' one.
The wires must be connected as follows: yellow-green for earthing, blue for neutral and
brown for the phase. The plug must be connected to an adequate safety socket.
• i xed equipment not provided with a power supply cable and plug, or any other device
that ensures disconnection from the electrical mains, with an opening gap of the con-
tacts that enables total disconnection in overvoltage category III conditions.
Said disconnection devices must be provided in the mains power supply in compliance
with installation regulations.
The yellow/green earth cable must not be cut of by the switch.
The Manufacturer declines all responsibility for failure to comply with the safety regulations.
FUMES DISCHARGE
EXTERNAL EXHAUST HOOD (SUCTION)
In this version the fumes and vapours are discharged outside through
the exhaust pipe.
To this end, the hood outlet i tting must be connected via a pipe, to an
external output.
The outlet pipe must have:
• a diameter not less than that of the hood i tting.
• a slight slope downwards (drop) in the horizontal sections to prevent condensation from
l owing back into the motor.
• the minimum required number of bends.
• the minimum required length to avoid vibrations and reduce the suction performance of
the hood.
You are required to insulate the pipes if it passes through cold environments.
In the presence of motors with 800m
3
/h or higher, a check valve is present to prevent
external air l owing back.
Deviation for Germany:
when the kitchen hood is used at the same time as appliances that are powered by energy other
than electricity, the negative pressure in the room must not exceed 4 Pa (4 x 10-5 bar).
HOOD WITH INTERNAL RECIRCULATION (FILTERING)
In this model, the air passes through an optional i lter unit in the ceiling
to be purii ed and recycled in the environment.
In this version the check valve must not be assembled: remove it if it is on the air
outlet i tting of the motor.
ASSEMBLY INSTRUCTIONS
only intended for qualii ed personnel
The hood can be installed in various coni gurations.
The generic assembly steps apply to all installations; for each case, follow
the specii c steps provided for the required installation.
OPERATION
WHEN TO TURN ON THE HOOD?
Switch on the hood at least one minute before starting to cook to direct fumes and vapours
towards the suction surface.
After cooking, leave the hood operating until complete extraction of all vapours and odours.
By means of the Timer function, it is possible to set auto switch-of function which will allow
the hood to turn of automatically after 15 minutes of operation.
WHICH SPEED IS TO BE SELECTED?
1st speed:
maintains the circulation of clean air with low electricity consumption.
2nd speed:
normal conditions of use.
3rd speed:
presence of strong odours and vapours.
4th speed:
rapid disposal of odours and vapours.
WHEN SHOULD THE FILTERS BE WASHED OR REPLACED?
The metal i lters must be cleaned every 30 hours of operation.
For further details see the
“MAINTENANCE”
chap.
ELECTRONIC PUSHBUTTON PANEL
Motor ON/OFF
Upon start-up, the speed is that stored at the previous operation.
Increase speed from 1 to 4
Speed 4 is only active for a few min-
utes, then speed 3 activates.
The speeds are indicated by the LEDs
on the keys:
Speed 1
Speed 2
Speed 3
Speed 4
("+" LED l ashing)
Reduce speed from 4 to 1
Light on/of
TIMER
(
red LED l ashing)
Auto switch-of after 15 min.
The function deactivates (red LED of ) if:
- The TIMER key (
) is pressed again.
- The ON/OFF key (
) is pressed.
USING THE RADIO CONTROL
WARNINGS!:
Place the hood away from sources of electromagnetic waves (e.g. micro-
wave ovens), which could interfere with the radio control and with the hood
electronics. The maximum operating distance is 5 metres, that may vary according to
the presence of electromagnetic interferences.
Radio control operated at 433.92MHz.
The radio control consists of two parts:
- the receiver built into the hood;
- the transmitter shown here in the i gure.
DESCRIPTION OF TRANSMITTING COMMANDS
UP
Motor switch-on and speed increase from 1
to 4. Speed 4 is only active for a few minutes.
DOWN
Speed decrease and motor switch-of .
Light ON-OFF
TIMER ON:
The motor automatically switch-
es of after 15 min.
The function is automatically disabled if the
motor is switched of (
key)
Command transmission active
Light on/of
Light ON-OFF
(
NO FUNCTION
)
(
NO FUNCTION
)
(
NO FUNCTION
)
Summary of Contents for nube
Page 1: ...INSTALLATION MANUAL falmecau com Nube...
Page 7: ...6 Max 1500 mm 9 mm MEASUREMENTS FOR INSTALLATION...
Page 13: ...12 120 mm x8 x4 1 3 1 2 3 6 Fixing the motor support brackets 6 MOTOR ON HOOD INSTALLATION...
Page 24: ...23 Closing the holding brackets V 3 O K Disassembly 2 1 2 FINAL OPERATIONS...
Page 26: ...25 3 1 2 Repositioning filters and piston and closing the hood 5 FINAL OPERATIONS...
Page 31: ...30 NOTE NOTES...