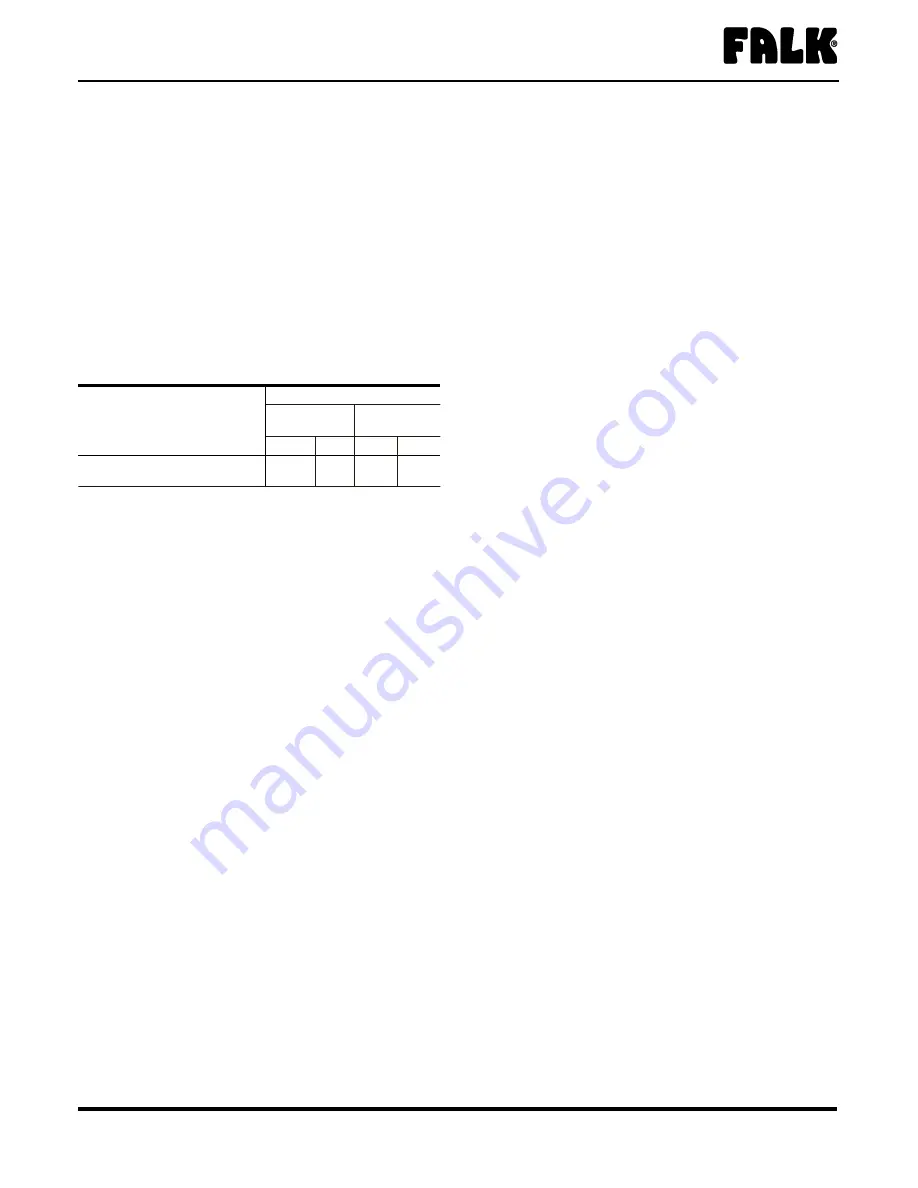
VISCOSITY (IMPORTANT) —
The proper grade for R & O and
EP lubricants is found in
. For cold climate conditions refer
to
and the “Synthetic Lubricant” paragraphs. Select
a lubricant which has a pour point at least 10
°
F (5.5
°
C) below the
expected minimum ambient starting temperature. Usable
temperature ranges can sometimes be widened if specific
application conditions are known.
If a gear drive operates in a typical indoor environment where
the ambient temperature is within 70
°
F to 125
°
F (21
°
C to
52
°
C), the oil viscosity should be increased one AGMA grade
above that shown for the 50
°
F to 125
°
F(10
°
C to 52
°
C) range.
That is, an AGMA Number 6 or 7 should be substituted for a 5
or 6 respectively, under this ambient condition.
OIL PUMPS —
When selecting a lubricant for a gear drive
equipped with an oil pump, cold temperature oil viscosity is
important. Lubricant viscosity at start-up generally should not
exceed 1725 cSt (8,000 SSU). When exceeding this viscosity,
pump cavitation is possible, preventing oil circulation. A sump
heater may be required or it may be possible to use a lower
viscosity oil to minimize pump cavitation, consult the Factory.
Petroleum Based Lubricants
Industrial type
petroleum based rust and oxidation inhibited (R & O ) gear
lubricants are the most common and readily available general
purpose gear lubricants.
EXTREME PRESSURE (EP) LUBRICANTS
—
For
highly loaded gear drives or drives loaded in excess of original
estimates, industrial type petroleum extreme pressure lubricants
are preferred. The EP lubricants currently recommended are of
the sulphur-phosphorus type.
WARNING:
EP LUBRICANTS IN FOOD PROCESSING INDUSTRY
— EP lubricants may contain toxic substances and should not be
used in the food processing industry without the lubricant
manufacturers’ approval.
Lubricants which meet USDA “H1”
classification are suitable for food processing applications.
CAUTION:
EP LUBRICANTS & INTERNAL BACKSTOPS — Do
not use EP lubricants or lubricants with anti-wear additives or
lubricant formulations including sulfur, phosphorus, chlorine,
lead derivatives, graphite or molybdenum disulfides in units
equipped with internal cartridge type backstops. Some lubricants
may contain anti-wear additives. Lubricants in
do contain several of these additives.
Synthetic Lubricants
Synthetic lubricants of the polyalphaolefin type are
recommended for cold climate operation, high temperature
applications, extended temperature range (all season) operation
and/or extended lubricant change intervals. The proper viscosity
grade of synthetic lubricant is given in
WARNING
:
SYNTHETIC LUBRICANTS IN FOOD PROCESSING
INDUSTRY — Synthetic lubricants may contain toxic substances
and should not be used in the food processing industry without
the lubricant manufacturers’ approval. Lubricants which meet
USDA “H1” classification are suitable for food processing
applications.
CAUTION
:
SYNTHETIC LUBRICANTS & INTERNAL BACKSTOPS
— Synthetic lubricants may be used in gear drives with internal
backstops operating only in cold temperatures -30
°
to +50
°
F
(-34
°
to +10
°
C). Mobil SHC 624 and SHC 626 provide proper
backstop action under these conditions. Other synthetic
lubricants may also be acceptable. DO NOT use synthetic
lubricants in units with backstops operating in ambient
temperatures above 50
°
F (10
°
C).
Oil Levels
Prior to filling gear drives, remove the inspection cover and flood
the oil troughs with a generous flow of oil to the bearings. Fill the
drive with oil to the level indicated on the oil dipstick. Approximate
oil capacities are given on the drive nameplate.
Lubricant Changes
OIL ANALYSIS REPORT—
Checking oil condition at regular
intervals is recommended. In the absence of more specific limits,
the guidelines listed below may be used to indicate when to
change oil:
1. Water content is greater than 0.05% (500 ppm).
2. Iron content exceeds 150 ppm.
3. Silicon (dust/dirt) exceeds 25 ppm.
4. Viscosity changes more than 15%.
PETROLEUM LUBRICANTS —
For normal operating
conditions, change gear oils every 6 months or 2500 operating
hours, whichever occurs first. If the drive is operated in an area
where temperatures vary with the seasons, change the oil
viscosity grade to suit the temperature, refer to
Lubricant suppliers can test oil from the drive periodically and
recommend economical change schedules.
SYNTHETIC LUBRICANTS —
Synthetic lube change intervals
can be extended to 8000-10,000 hours depending upon
operating temperatures and lubricant contamination. Laboratory
analysis is recommended for optimum lubricant life and gear
drive performance. Change lube with change in ambient
temperature, if required. Refer to
The Falk Corporation, a Sundstrand Company, P.O. Box 492, Zip 53201-0492
148-050
3001 W. Canal St., Zip 53208-4200, Milwaukee, WI USA Telephone: 414-342-3131
April 1999
Fax: 414-937-4359 e-mail: [email protected] web: www.falkcorp.com
Supersedes 4-89
Installation & Maintenance Instructions
•
Enclosed Gear Drives
(Page 4 of 8) Sizes 1080–1195 & 2050–2235
•
Types GHB, Y, YB & YBX
TABLE 2 — Viscosity Grade Recommendations
for R & O or EP Lubricants
Output RPM
Normal Climates
15
°
to 60
°
F
(-9
°
to +16
°
C)
50
°
to 125
°
F
(10
°
to 52
°
C)
ISO-VG AGMA ISO-VG AGMA
Output RPM Below 80
150 4 320 6
Output RPM 80 & Above
150 4 220 5