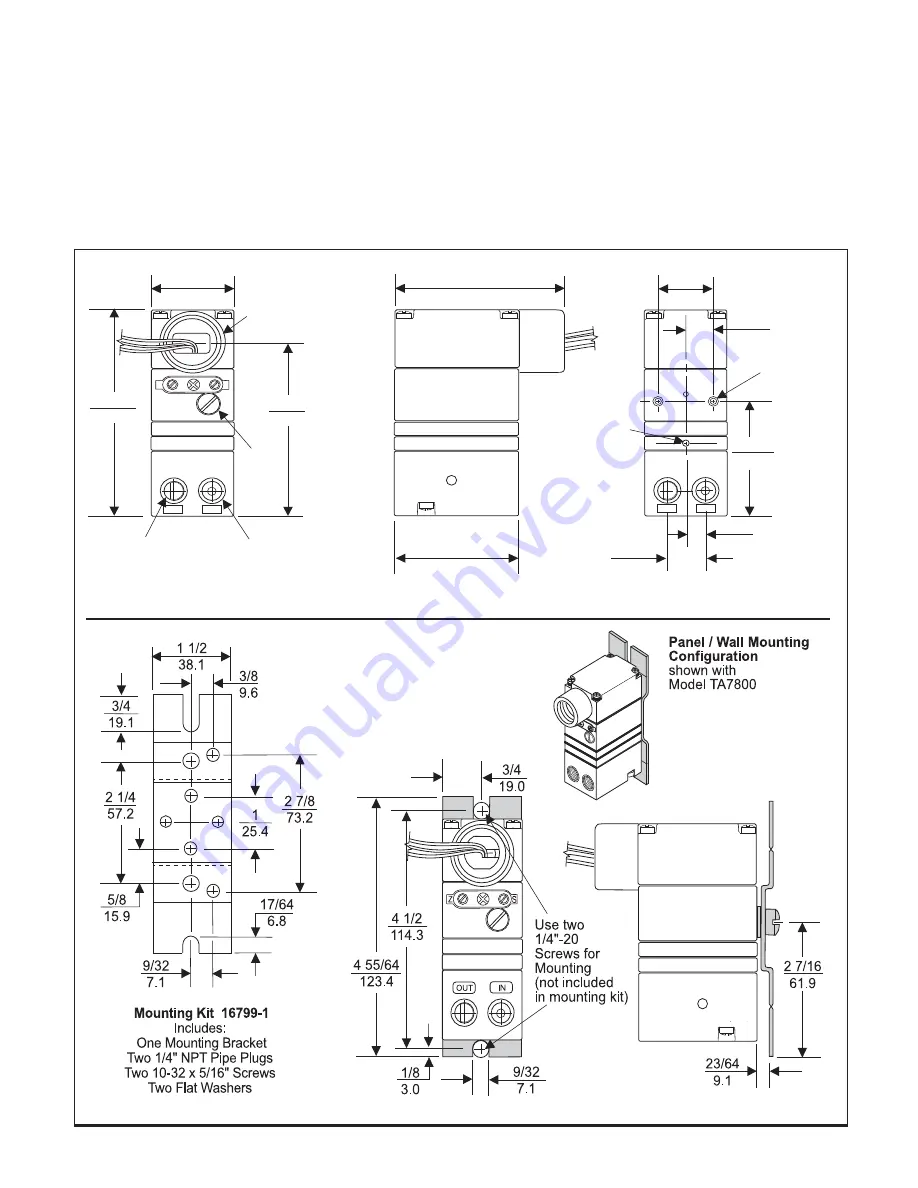
INSTALLATION
You can mount the Model T7800 on a flat surface using two
10-32 Screws. For more information, see Figure 2.
The Model T7800 ships from the factory with Mounting Kit
16799-1 for Panel or Wall Mounting and Mounting Bracket
Kit 16893-1 for Din Rail Mounting. For more information, see
Figure 3 and Figure 7.
An optional mounting kit, 19254-1, is available to install the
unit on a 2" pipe. For more information, see Figure 8.
ATEX Directive- Special Conditions for Safe Use
The enclosure is manufactured from aluminum alloy. In rare
cases, igntion sources due to impact and friction sparks
could occur. This shall be considered when the equipment
is installed in locations that specifically require Group II,
category 1G equipment.
NOTE: The TR7800 transducer is designed for use
with the TR Rack Kit. Physically, it is the same
as the TT7800 (Terminal Block) unit except
that the terminal block has been rotated to the
back. For more information, see Figure 6.
1/2-14
NPT
OUT
Z
IN
S
3 23/32
94.5
3 5/32
80.3
1/2
12.7
25/32
19.7
25/64
9.8
1
25.4
OUT
IN
2 3/64
51.8
Use two
10-32
Screws for
mounting
3 3/64
77.5
2 1/4
57.1
1 33/64
38.7
Orifice
Inlet
Outlet
Vent
Figure 3.
Mounting Kit 16799-1
(included with unit)
Figure 2.
TA7800 Outline Dimensions
3