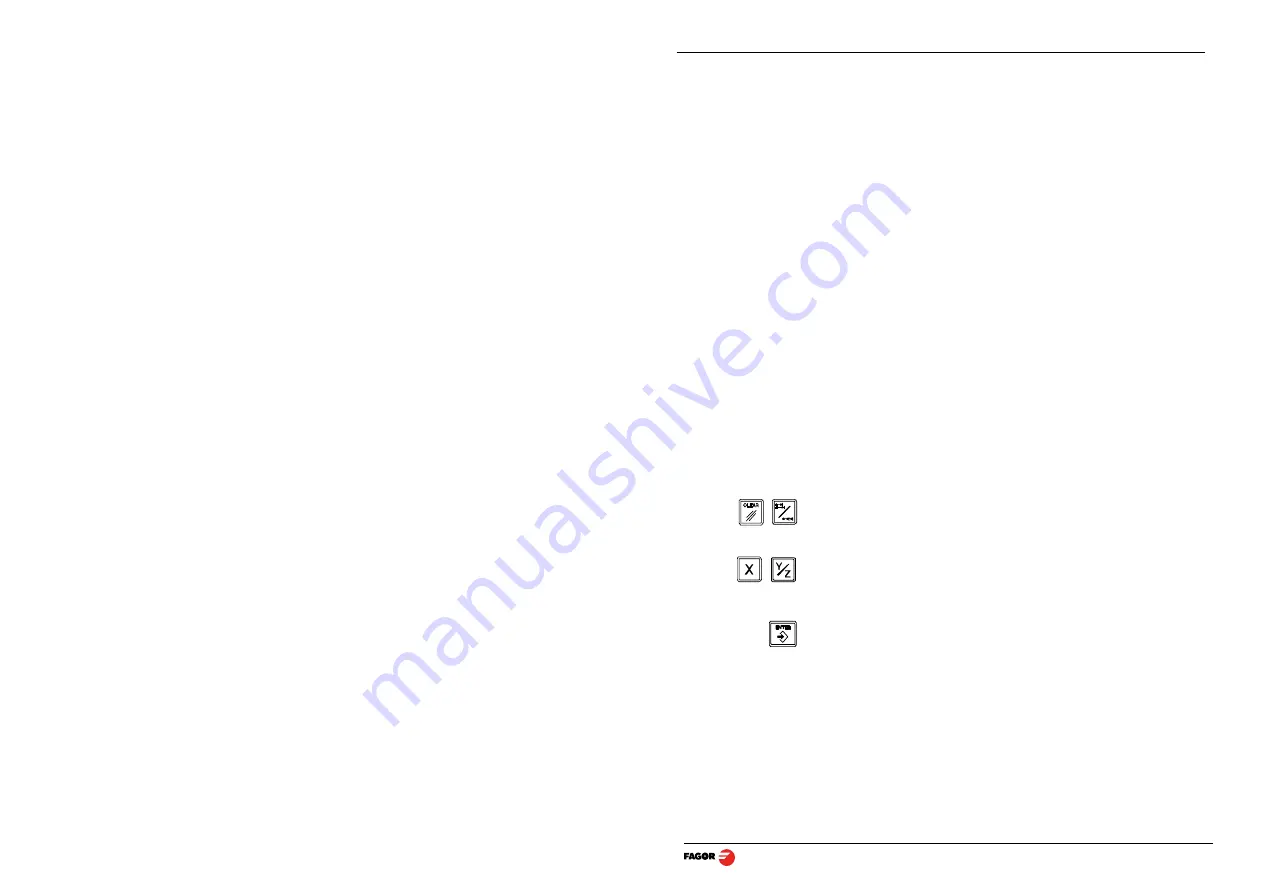
V0703 - 10i / 20i - Installation/Operation - DRO operation - (7/29)
2.3 Machine Reference selection and search
Although it is not absolutely necessary, it is recommended to use the
reference marks (Io) of the feedback system in order to set a machine zero
point.
This allows the user to reference the machine axes and restore the work
coordinates after having turned the dro off, moved the machine while the dro
was off, for safety or for any other reason.
Fagor linear encoders have reference marks every 50 mm all along its length.
In order to use these marks properly, choose an area on the axis, for example
in the middle of the measuring length or at one end. Approach this area and
carry out the home search. Once the reference mark has been found, mark
this area with a marker or sticker in order to carry out the home search in the
same area in later occasions and make sure that you are using the same
machine zero point (home).
Fagor also offers encoders with distance-coded reference marks every 20, 40
or 100 mm. When using these distance-coded reference marks, there is no
need to move to the 0 position to find the references, simply move a distance
equal to the gap between marks (20, 40 or 100 mm depending on the linear
encoder)
When using an absolute encoder, there is no need to search for the reference
marks (home).
The dro stores in its internal memory work coordinates such as machine zero,
absolute and incremental.
2.3.1 Home search sequence
For encoders with regular reference marks, move the axis to the home area.
Access or exit the home search mode.
The axis displays blink showing
" r "
if the axis has not been homed or
" r on"
if it has been homed.
Select the axis to be referenced (homed)
The selected axis blinks until a reference mark is detected. The reference
signal presets the axis display automatically with the value of PAR10, 0.000
mm by default.
If the encoder does not have a reference mark, move the axis to the desired
position and press this key.