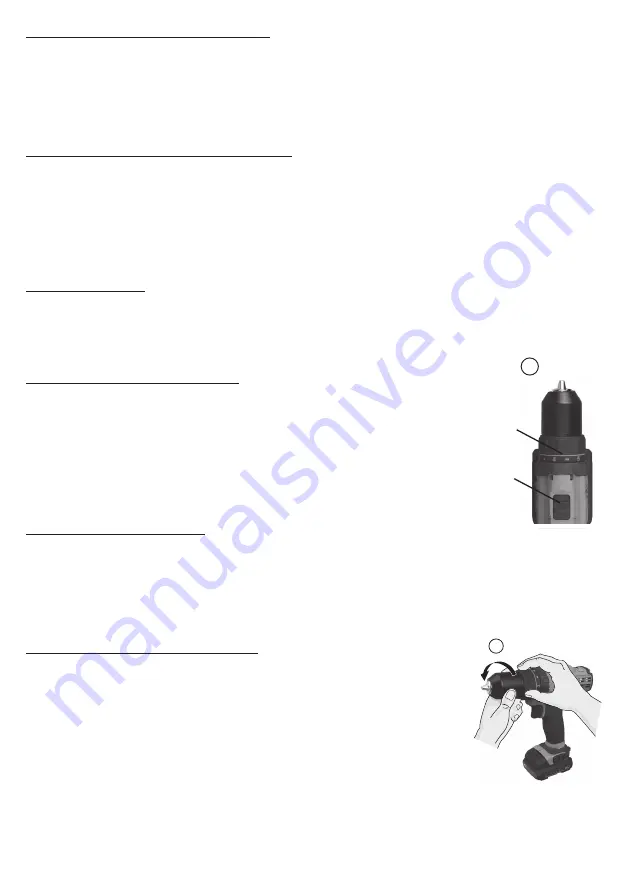
24
Variable Speed Trigger Switch (Fig. 2)
To turn the tool on, squeeze the trigger switch (A). To turn the tool off, release the trigger switch. Your tool is equipped with a brake. The
chuck will stop when the trigger switch is fully released. The variable speed switch enables you to select the best speed for a particular
application. The more you squeeze the trigger, the faster the tool will operate. For maximum tool life, use variable speed only for starting
holes or fasteners.
NOTE:
Continuous use in variable speed range is not recommended. It may damage the switch and should be avoided.
Forward/Reverse Control Button (Fig. 2)
A forward/reverse control button (B) determines the direction of the tool and also serves as a lock off button.
To select forward rotation
,
release the trigger switch and depress the forward/reverse control button on the right side of the tool.
To select reverse
, depress the
forward/reverse control button on the left side of the tool. The center position of the control button locks the tool in the OFF position. When
changing the position of the control button, be sure the trigger is released.
NOTE:
The fi rst time the tool is run after changing the direction of rotation, you may hear a click on start up. This is normal and does not
indicate a problem.
Worklight (Fig. 2)
There is a worklight (C) located under the torque adjustment collar (D). The worklight is activated when the trigger switch is depressed if the
trigger remains depressed, the worklight will remain on.
NOTE:
The worklight is for lighting the immediate work surface and is not intended to be used as a fl ashlight.
Torque Adjustment Collar (Fig. 3)
The torque adjustment collar (D) is clearly marked with numbers and a drill bit symbol. The collar should be rotated
until the desired setting is located at the top of the tool. Locators are provided in the collar to eliminate the guess
work when selecting fastening torque. The higher the number on the collar, the higher the torque and the larger the
fastener which can be driven. To lock the clutch for drilling operations, move to the drill bit position.
NOTE:
When using the drill/driver for drilling holes, be sure that the torque adjusting collar is set so the fi gure
of the drill is aligned with the center line on the top of the tool. Failure to do this will allow the clutch to slip while
attempting to drill.
Dual Range Gearing (Fig. 3)
The dual range feature of your driver/drill allows you to shift gears for greater versatility. To select the low speed, high torque setting, turn
the tool off and permit to stop. Slide the gear shifter (E) forward (towards the chuck). To select the high speed, low torque setting, turn the
tool off and permit to stop. Slide the gear shifter back (away from chuck).
NOTE:
Do not change gears when the tool is running. If you are having trouble changing gears, make sure that the dual range gear
shifter is either completely pushed forward or completely pushed back.
Keyless Single Sleeve Chuck (Fig. 5)
Your tool features a keyless chuck with one rotating sleeve for one-handed operation of the chuck. To insert
a drill bit or other accessory, follow these steps.
1. Lock the trigger in the OFF position as previously described.
2. Grasp the black sleeve of the chuck with one hand and use the other hand to secure the tool.
Rotate the sleeve counterclockwise far enough to accept the desired accessory.
3. Insert the accessory about 3/4” (19 mm) into the chuck and tighten securely by rotating the
chuck sleeve clockwise with one hand while holding the tool with the other. Your tool is equipped
with an automatic spindle lock mechanism. This allows you to open and close the chuck with one
hand.
To release the accessory, repeat step 2 above.
WARNING:
Do not attempt to tighten drill bits (or any other accessory) by gripping the front part of the chuck and turning the tool
on. Damage to the chuck and personal injury may result. Always lock off trigger switch when changing accessories.
Be sure to tighten chuck with one hand on the chuck sleeve and one hand holding the tool for maximum tightness.
3
D
E
5
Summary of Contents for CL3.P10J
Page 117: ...117 1 2 RCD RCD EL...
Page 118: ...118 3 off on 4 5...
Page 119: ...119 6 CCA V W watt Hz hertz min no I I min RPM IPM BPM A...
Page 120: ...120 FACOM 40 C 105 F on li ion 15 FACOM...
Page 121: ...121 FACOM 2 230V 1 1 2 H 1 3 H 1...
Page 122: ...122 1 18 24 C 65 F 75 F 4 5 C 40 F 40 5 C 105 F 2 3 4 18 24 C 65 F 75 F 5 6...
Page 124: ...124 FACOM EN 60335 FACOM 3A 1mm2 30 FACOM D C A F 2 E B G H E I...
Page 125: ...125 4 H G 2 A 2 B OFF 2 C D 3 D 3 E 4 H G 3 D E...
Page 126: ...126 5 1 OFF 2 3 19 3 4 2 OFF 6 D E 1 6 4 1 4 Torx 6 7 6 4 1 4 off off 5 6 7 E D E D...
Page 142: ...142 CL3 BA1015 CL3 CH1018...