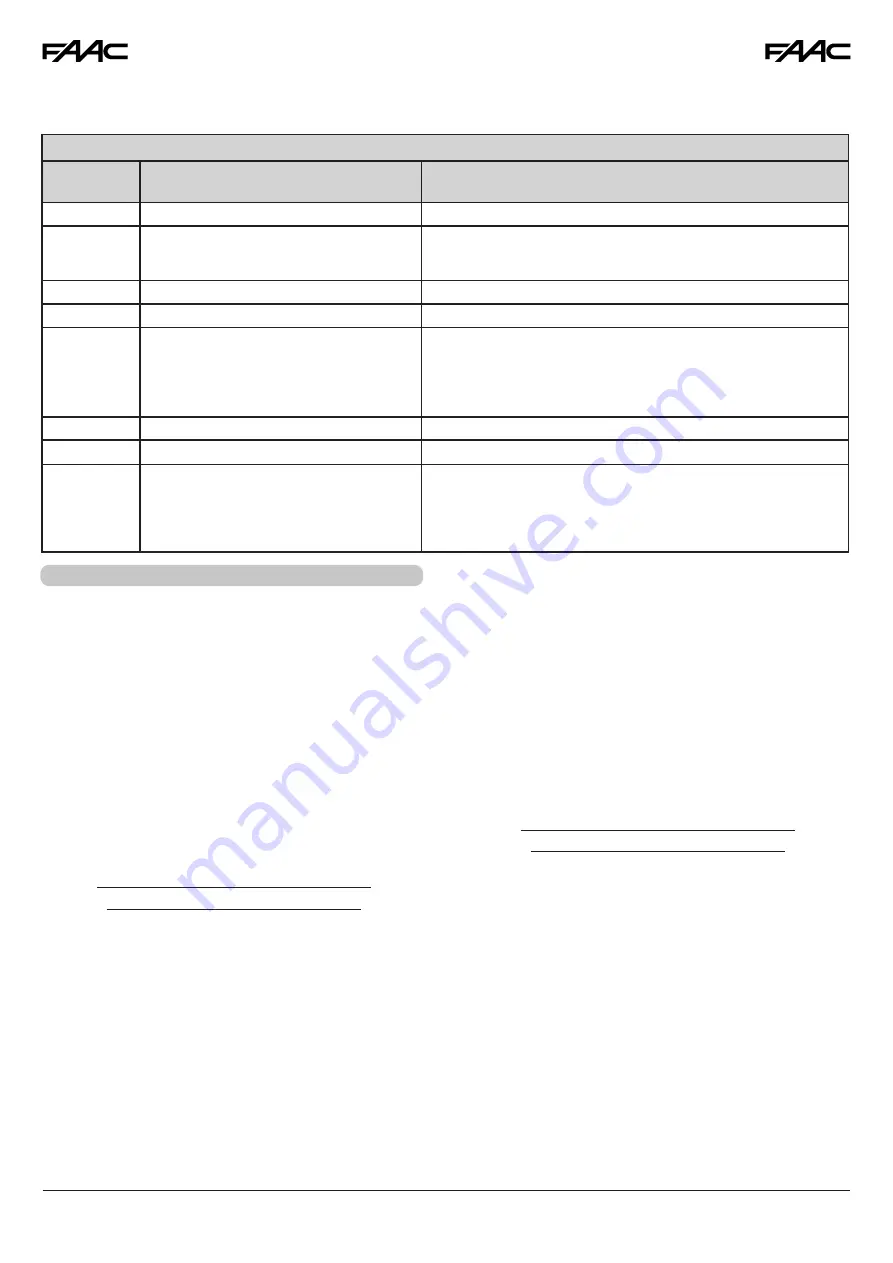
WARNING: If the time learning setup is done automatically then
the slow down points are set by the board on his own
Move the leafs to the mid position
Very important for a good result
1. Press and hold the SETUP button until the SETUP LED lights up,
wait about 3 sec. until it turns off and then release it imme-
diately. NOTE: If you wait too long to release it the manual
set-up will start. The LED will blink during the setup procedure
2. Leaf 2 (if present) starts to move slowly in closing direction,
stopping when it reaches the mechanical stop or FCC2.
3. Leaf 1 begins to move slowly in closing direction, stopping
when it reaches the mechanical stop, or FCC1.
4. Leaf 1 starts to move slowly in opening direction, followed
by leaf 2 (if present)
still slowly
.
5. When they both reach the open mechanical stop or FCA1
and FCA2 they stop and reverse, leaf 2 (if present) automa-
tically starts closing at full speed followed by leaf 1.
6. When they reach the close mechanical stop or FCC1 and
After powering up the board for the first time or when the board
will need it the setup LED will blink at a slow frequency to indicate
that the setup procedure to learn the running times is needed.
The setup can be redone at any time by pressing and holding
the setup button as indicated below. The setup cannot be done
until the safeties and stop inputs are wired.
After the setup first movement, if the leafs are opening instead
of closing you need to reverse the wires going to the motor that
moves in the wrong direction
LED ERROR DISPLAY
NUMBER OF
FLASHES
ERROR CONDITION
SOLUTION
1
OBSTACLE DETECTION
Remove the obstacle, Check force and sensitivity settings
2
BOARD IN SLEEP MODE
(Slow blinking means that the automatic open
in case of power failure function is active)
Verify the presence of AC power
3
MOTOR 1 FAILURE
Inspect wiring to motor. If the wiring is good replace motor 1
4
MOTOR 2 FAILURE
Inspect wiring to motor. If the wiring is good replace motor 2
5
ENCODER on motor 1 or motor 2 error
• Verify the encoder wiring and LED status. If they are correct replace
the encoder
• Verify motor and encoder wire gauge are correct
• Verify operator is not on manual and hydraulic units don’t need
to be bled
6
FAIL SAFE FAILED
Verify the photocells wiring and alignement
7
BOARD THERMAL PROTECTION ACTIVE
Turn off the board and wait until the components cool down
8
MAX RUN TIME REACHED
WITHOUT FINDING THE
POSITIVE STOP (10 min. )
- Verify that the operator manual release is not engaged
- Verify that the board recognizes the mechanical stop, in case redo
the setup procedure
- Verify that the gates slow down before reaching the positive stops. If
they don’t then redo the setup procedure
The diagnostic LED shows only one error condition at a time, with the priority of the below table. In case there is more than
one error once one is eliminated the LED will show the next
FCC2 both leafs stop and leaf 1 restarts automatically
opening at full speed followed by leaf 2 (if present).
7. If you selected an automatic logic the board will wait for
the pause time and then closes the gate automatically.
Otherwise you have to give an OPEN command to close
the gate.
WARNING: If the manual time learning setup is done then the
slow down points must be set by the installer during the proce-
dure.
Slow down is required for proper operation.
Move the leafs to the mid position
Very important for a good result
1. Press and hold the SETUP button until the SETUP LED lights up,
keep it pressed for about 3 sec. until it turns off and keep it
pressed more until the leaf 2 (if present) starts moving slowly.
The LED will blink during the setup procedure
2. Leaf 2 will move in closing direction until it reaches the
mechanical stop or FCC2
3. Leaf 1 starts moving slowly until it reaches the mechanical
stop or FCC1
4. Leaf 1 starts moving in opening direction at the set speed
(trimmer speed).
5. At the point where you want the slowdown to start give
an OPEN A command with the push button or the remote
that is already stored in memory. Leaf 1 starts to slow down
and stops when it reaches the mechanical stop or FCA1.
6. Leaf 2 starts moving in opening direction at the set speed
(trimmer speed)
AUTOMATIC TIME LEARNING
MANUAL TIME LEARNING
6. TIME LEARNING (SET-UP)
22