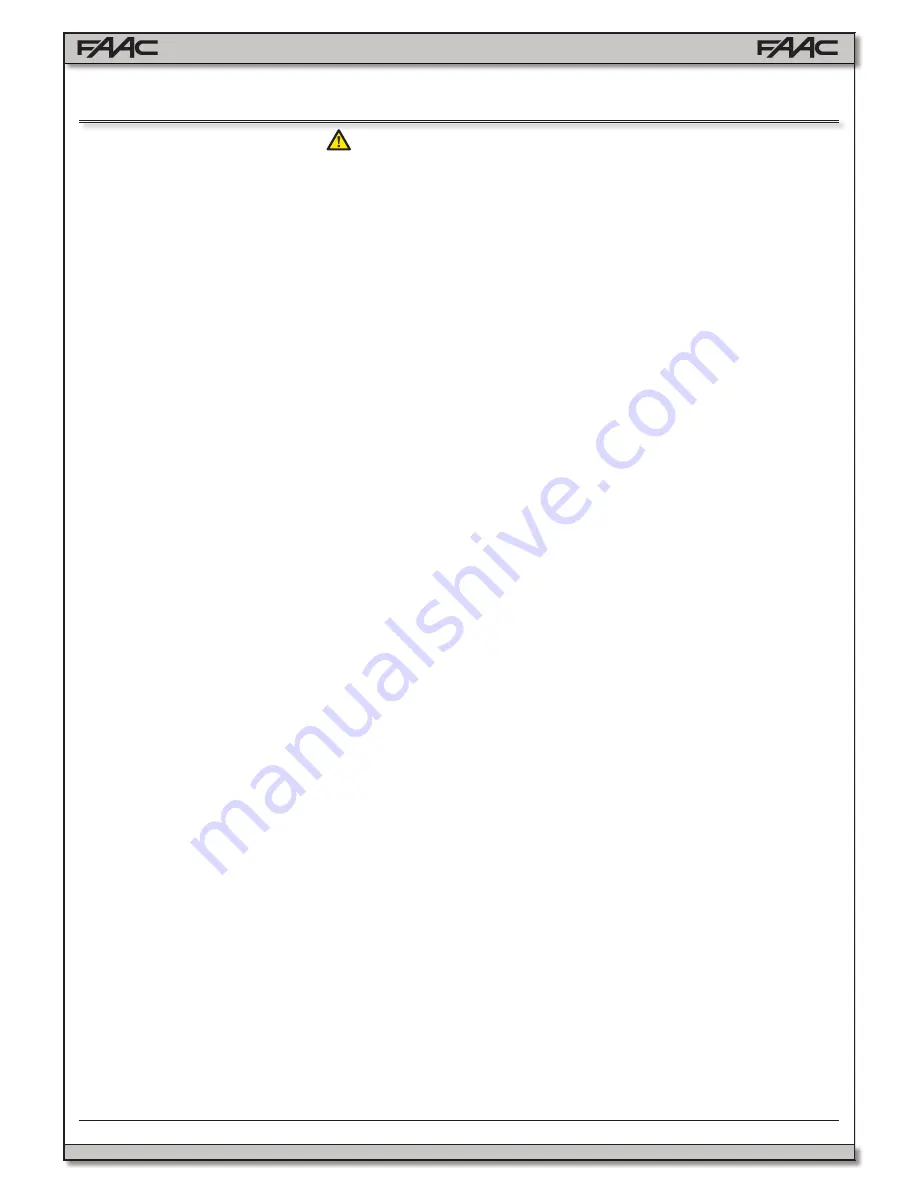
3
FAAC Model S450H 24V Hydraulic Swing Gate Operator
1. Install the gate operator only when the following
conditions have been met:
•
The operator is appropriate for the type and usage
class of the gate.
•
All openings of a horizontal slide gate have been
guarded or screened from the bottom of the gate to
a minimum of 4 feet (1.25 m) above the ground to
prevent a 2.25 inch (55 mm) diameter sphere from
passing through openings anywhere in the gate or
through that portion of the adjacent fence that the
gate covers when in the open position.
•
All exposed pinch points are eliminated or guarded.
•
Guarding is supplied for exposed rollers.
2. The operator is intended for installation on gates used
by vehicles only. Pedestrians must be provided with a
separate access opening.
3. To reduce the risk of entrapment when opening and
closing, the gate must be installed in a location that
allows adequate clearance between the gate and
adjacent structures. Swinging gates shall not open
outward into public access areas.
4. Before installing the gate operator, ensure that the gate
has been properly installed and that it swings freely in
both directions. Do not over-tighten the operator clutch
or pressure relief valve to compensate for a damaged
gate.
5. User controls must be installed at least 6 feet (1.83
m) away from any moving part of the gate and located
where the user is prevented from reaching over, under,
around or through the gate to operate the controls.
Controls located outdoors or those that are easily
accessible shall have security features to prevent
unauthorized use.
6. The Stop and/or Reset buttons must be located within
line-of-sight of the gate. Activation of the reset control
shall not cause the operator to start.
7. All warning signs and placards must be installed
and easily seen within visible proximity of the gate. A
minimum of one warning sign shall be installed on each
side of the gate.
8. For gate operators that utilize a non-contact sensor
(photo beam or the like):
•
See instructions on the placement of non-contact
sensors for each type of application.
•
Exercise care to reduce the risk of nuisance tripping,
such as when a vehicle trips the sensor while the
gate is still moving.
•
Locate one or more non-contact sensors where the
risk of entrapment or obstruction exists, such as at
the reachable perimeter of a moving gate or barrier.
•
Use only FAAC “Photobeam” photoelectric eyes to
comply with UL325.
Important Installation Instructions
WARNING - TO REDUCE THE RISK OF SEVERE
INJURY OR DEATH:
•
READ AND FOLLOW ALL INSTRUCTIONS.
•
Never let children operate or play with the gate
controls. Keep remote controls away from children.
•
Always keep people and objects away from the
gate. NO ONE SHOULD CROSS THE PATH OF A
MOVING GATE.
•
Test the gate operator monthly. The gate MUST
reverse on contact with a rigid object or when an
object activates a non-contact sensor. If necessary,
adjust the force or the limit of travel and then retest
the gate operator. Failure to properly adjust and retest
the gate operator can increase the risk of injury or
death.
•
Use the manual release mechanism only when the
gate is not moving.
•
KEEP GATE PROPERLY MAINTAINED. Have
a qualified service person make repairs to gate
hardware.
•
The entrance is for vehicles only. Pedestrians must
use a separate entrance.
•
SAVE THESE INSTRUCTIONS.
IMPORTANT SAFETY INFORMATION
Important Safety Instructions