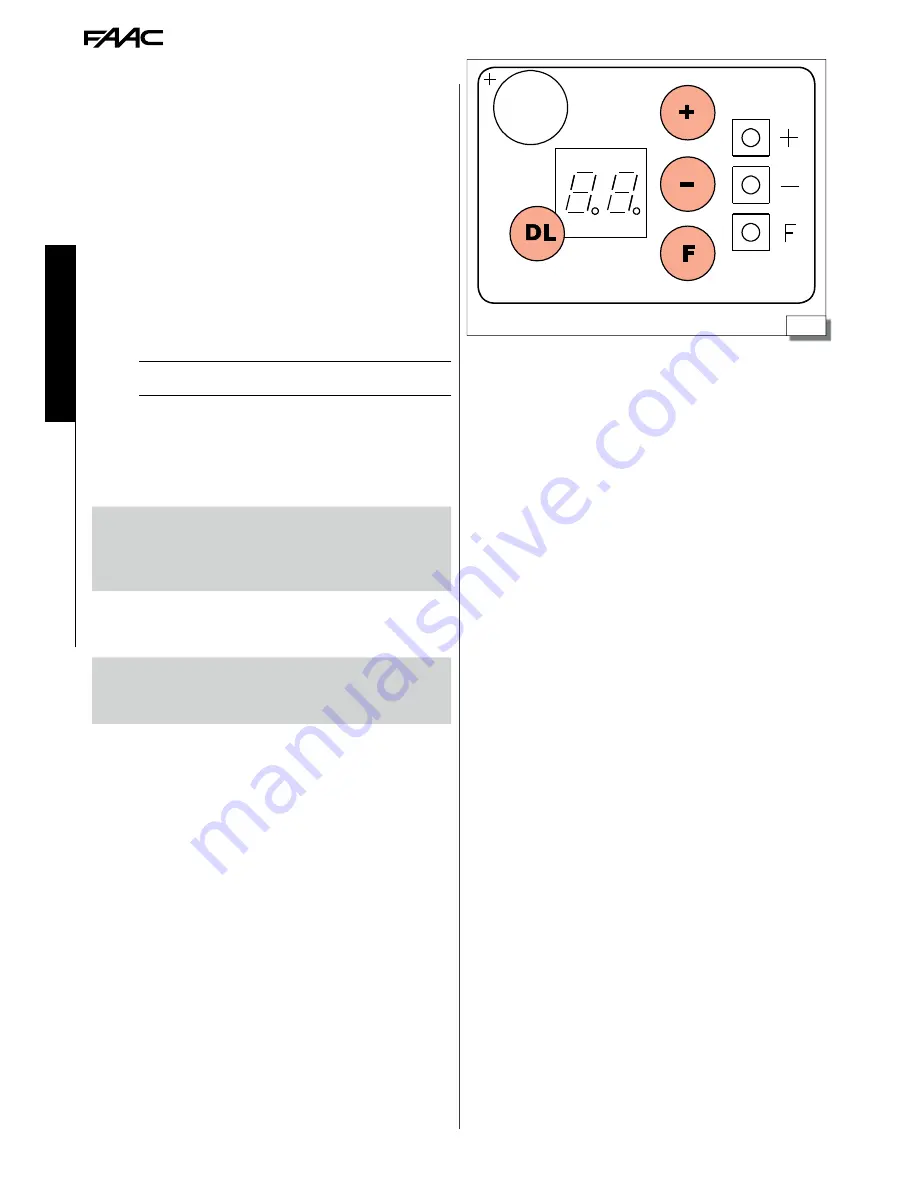
15
J355HA M50
14
532141 - Rev. A
Tr
ansla
tion of the original instruc
tions
ENGLISH
3.2 BOARD PROGRAMMING
After connecting and switching on the power to the control board as
per the previous chapter, select the work pre-setting for the bollard
J355HA M50 by performing the following operation:
1. Access level 1 programming by holding down the F button on the
control board (
15
). The display will show the letters dF.
2. Release the F button and with the +
+ button, select the value
06
3. Press the F button and hold it down whilst simultaneously pressing
the - button to exit programming screen and save the changes
made.
4. Press the F button and hold it down, as well as pr for
around 10 seconds, until the display shows
01
5. Release the buttons, then press the F button scroll until you reach
the
b6
parameter
6. Set the value
b6
=
Y
7. Press the F button and hold it down whilst simultaneously pressing
the - button to exit programming screen and save the changes
made.
For more information on programming the equipment, please refer
to the relevant instructions.
3.3 TROUBLESHOOTING
Below are a series of tips to help identify and solve a number of
particular issues.
CONDITION
SUGGESTION
The bollard will not rise, it remains in
the low position.
Check that you have selected default No. 6 on
the JE275 control board
Check that the bollard is set to automatic
operation (§2.9)
Check the wiring of the motor
The bollard will not lower, and remains
in the high closed position.
Check that there is nothing between the cyl-
inder and the slide bushing that is preventing
movement
Check the wiring of the motor
The flashing LED does not work
Check that you have selected default No. 6 on
the JE275 (§3.2) control board
Check that the power connector located under
the head is properly inserted.