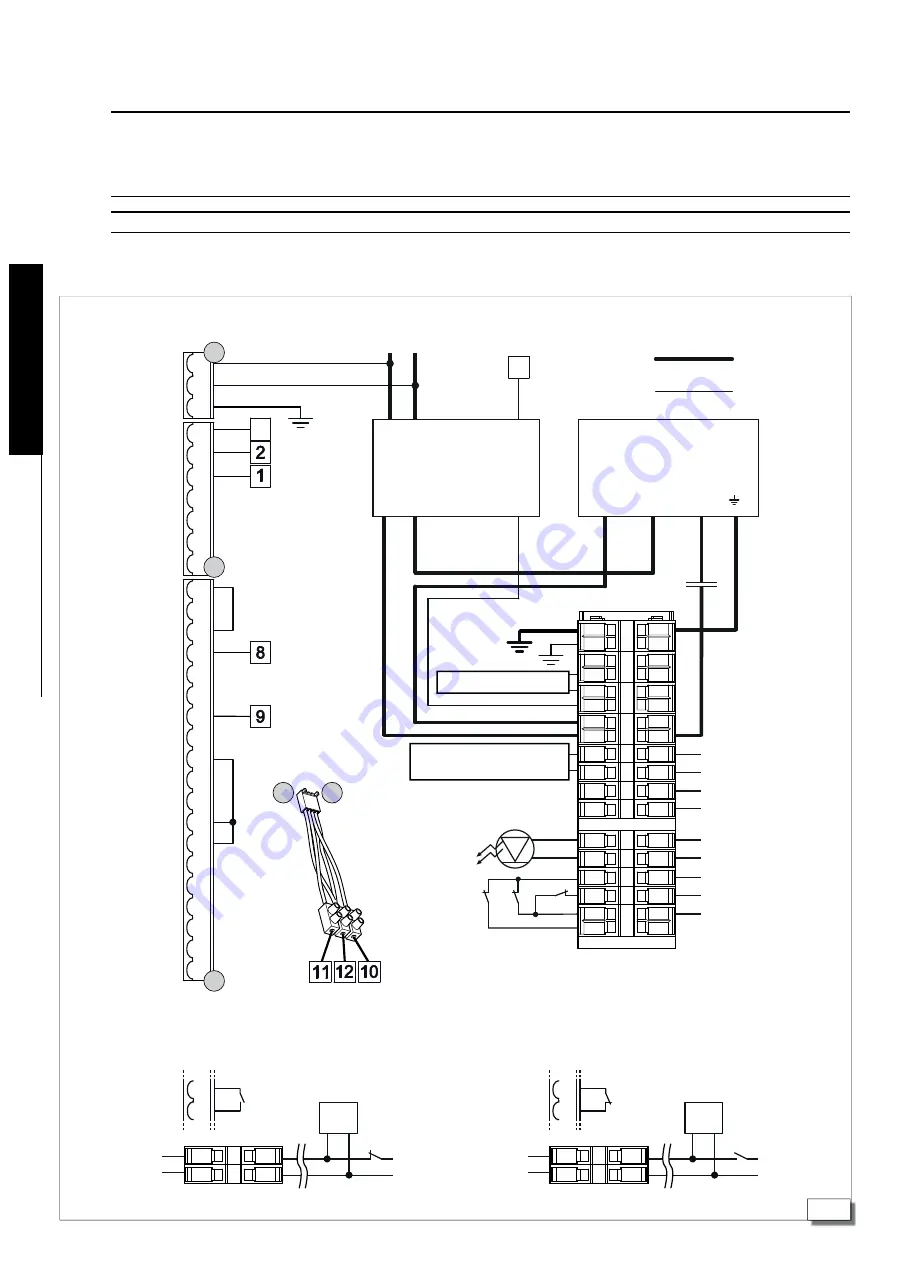
14
1
2
3
4
5
6
7
8
9
10
11
2 4 6 14 A2
1 3 5 13 A1
PE
COM
AP
CL
L N
19
18
OUT 4
GND
16
17
15
14
12
13
11
89
67
45
23
10
1
OPEN A
STOP
LOOP 1
LOOP 2
LOOP 2
LOOP 1
CLOSE
FSW
EMERGENCY
OUT 1
OUT 2
OUT 3
GND
GND
+24 V
+24 V
OUT 3
25
23
21
26
24
22
20
MOT1
COM
MOT2
COM
COM
LAMP
FAN
J1
NL
PE
J5
J3
A1
A1
4
5
9
10
EMERGENCY
GND
R1
12
R1
4
5
9
10
EMERGENCY
GND
R1
R1
J2
J9
230 V ~
230 V ~
230 V~
230 V~
FG7OR - 3G4
FG7OR - 16G1,5
+24V
Tr
ansla
tion of the original instruc
tions
ENGLISH
3. ELECTRONIC EQUIPMENT JE275
BOLLARD SIDE
JE275 BOARD SIDE
Limit switch
UP
Limit switch
DOWN
Lights
+24V
Limit switch UP
Limit switch DOWN
Limit switch common
EFO pressure
switch
EFO
solenoid valve
Heater
(optional)
Refer to the
diagram below
EFO N.O. connection (activtes also in case of black out)
EFO N.C. connection (voluntary activation only)
!
Before performing any work on the electronic equipment (connections, maintenance), always turn the power off.
Install a differential thermal breaker upstream with adequate tripping threshold (0.03A).
Connect the ground cable to the terminal on the J9 connector on the equipment (
14
).
Check that the mains switch is equipped with a locking key, unless this is fitted under the supervision of the operator/maintainer
The equipment must be installed at a height between 0.4 m and 2.0 m.
3.1 ELECTRICAL CONNECTIONS
Solenoid valve
Contactor
Motor
Bollard side
Bollard side
Board side
Board side
Br
ow
n
Blue
Black
www.FastGateOpeners.com | (800) 878-7829 | [email protected]