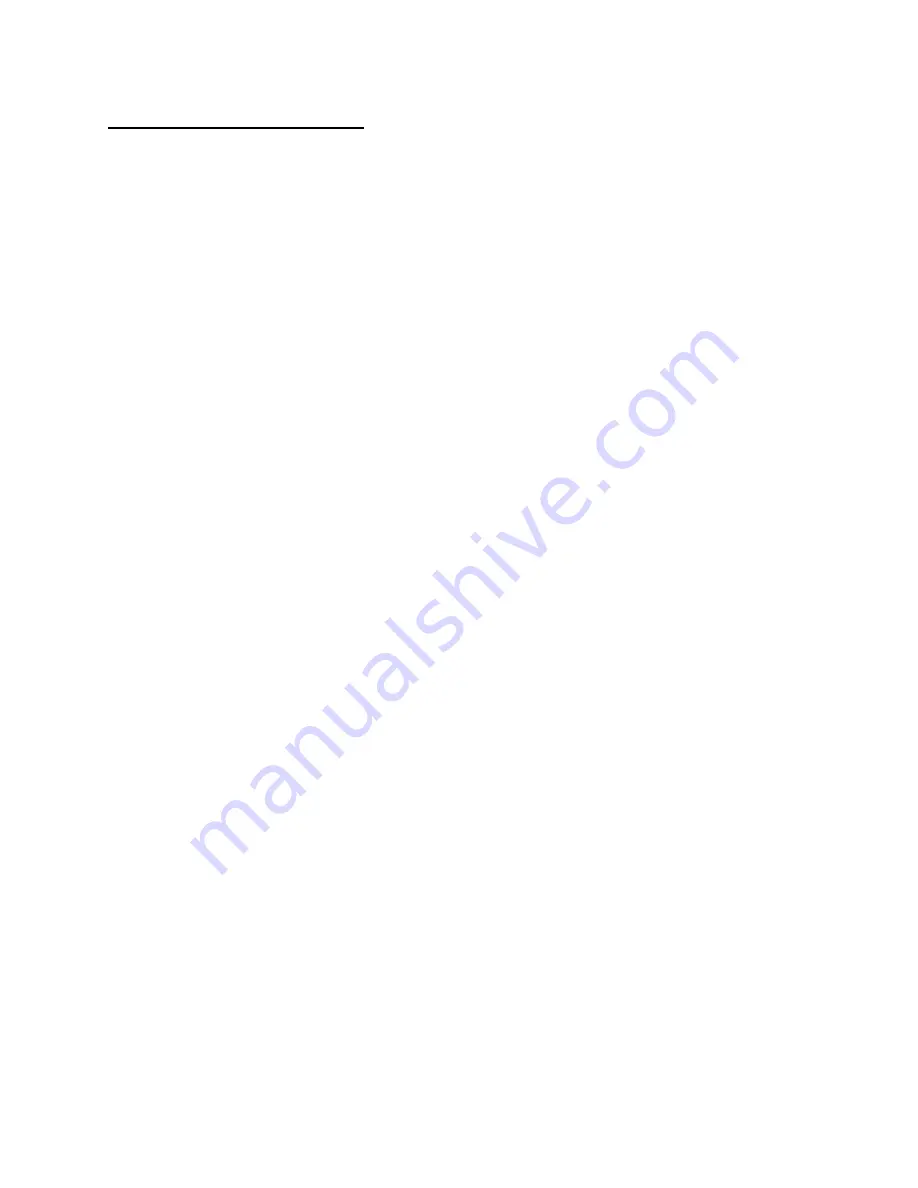
ELECTRICAL SAFETY RULES
1. Do not alter or bypass any protective interlock.
2. Before starting the machine, read and observe all warning labels and markings such as
nameplates and identification plates.
3. Only personnel who are properly trained and have adequate knowledge and skill should
undertake all electrical/electronic troubleshooting and repair.
4. Use extra precautions in damp areas to prevent yourself from accidental grounding.
5. Make sure you body and your tools are clear of electrical grounding.
6. The control panel doors should be opened only when it is necessary to check the electrical
equipment or electrical wiring.
7. Before applying power to any equipment, establish without a doubt that all persons are
clear.
8. Be alert and be sure you can work with no outside distractions.
9. Avoid wearing metal frame glasses or wearing a metallic necklace or chain, and never work
on electrical equipment while wearing rings, watches, or bracelets.
10. When replacing conductors, make sure they conform to the manufacturer’s specifications,
including proper color-coding.
11. Do not alter the electrical circuits. If machine damage is caused by an unauthorized
alteration, the user is responsible, not the manufacturer.
12. Always assume the electrical power is ON and treat circuit as live. This caution develops a
habit that may prevent an accident.
13. Give capacitors time to discharge. Otherwise, it should be done manually with care.
14. Use proper test equipment to make certain you have an open circuit. Test equipment must
be checked and calibrated at regular intervals.
15. Open the control panel doors only when it is necessary to check the electrical equipment or
disconnecting handle mechanism is in its proper position.
16. All covers on junction boxes must be closed before leaving any job.
Summary of Contents for XS-1A25
Page 18: ......
Page 19: ......
Page 20: ...MAIN FRAME GROUP...
Page 22: ...WORKING TABLE CONVEYOR GROUP...
Page 24: ...P HEAD GROUP...
Page 26: ...PRESSURE ROLLER GROUP...