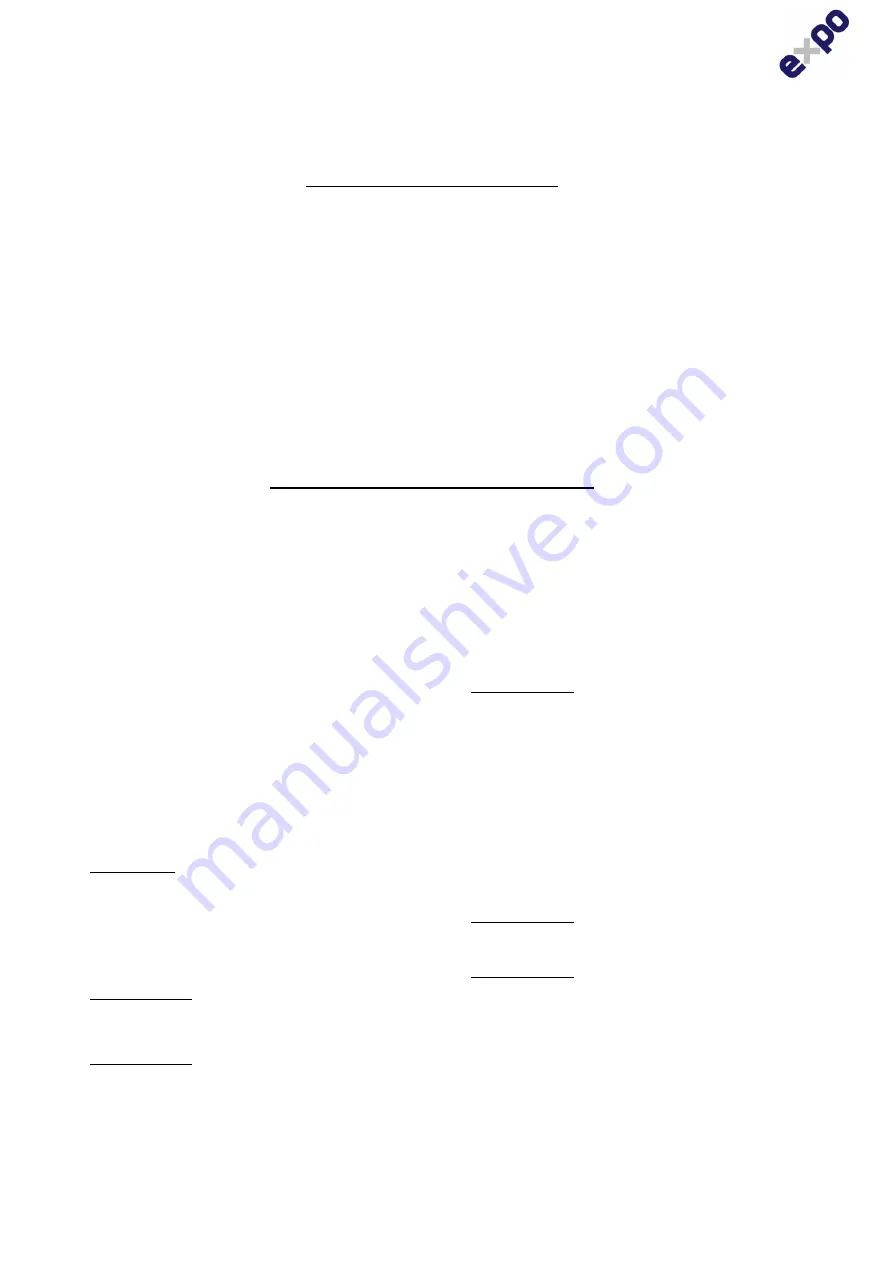
Expo Technologies Limited
¤
¤
Page 6 of 7
ML384 Issue 03
–
09.01.13
Section 3
Maintenance of the System
The maintenance recommended for the system consists of
the following, supplemented by any additional local
requirements imposed by the authority having jurisdiction.
3.1 Initial
Maintenance
Expo recommends that the commissioning test be
repeated at least every six months. They include checking
the opening pressure of the Relief Valve, setting of the
Minimum Pressure Sensor, the "Normal Working Pressure"
of the enclosure and, for "X" Purge systems, the setting of
the purge timer (as described in Section 2 of this manual).
In addition, the following checks are also recommended at
that time:
- Check the RLV and any other Spark Arrestors. Remove
any debris or corrosion, or replace the Spark Arrestor with
a spare.
- Check the condition of the air supply filter element.
Clean or replace it as necessary.
3.2 Routine
Maintenance
At least every two years, the following additional
checks are recommended:
- Apparatus is suitable for the Hazardous Location
- There are no unauthorized modifications
- The source of air is uncontaminated
- The interlocks and alarms function correctly
- Approval labels are legible and undamaged
- Adequate spares are carried
- The action on pressure failure is correct
Section 4
Fault Finding
–
LC and CFHP Systems
4.1 General
If the system does not behave in the manner described
above there is a fault. Some of the more likely faults are
dealt with below. If a cure cannot be effected by following
the procedure shown below please call Expo (24 hour
answering) or your supplier for further assistance.
The system has been designed for ease of fault finding
and many of the components fitted are plug-in or sub-base
mounted. Check components by substitution only after
establishing that such action is necessary. If the system is
less than 12 months old, parts under warranty should be
returned to Expo Technologies for investigation, with a full
report of the fault and the system Serial number.
NOTE: As with any pneumatic system the greatest
enemies are water, oil and debris in the air supply. For this
reason a dust and water filter should always be fitted. But
debris can enter from other sources and it is vital therefore
that the procedures described in Section 2 is carried out
before using the system for the first time, or following any
disconnection of the pipework. Failure to perform this work
may cause damage, which will not be covered under
warranty.
Fault Finding
NOTE: Before making the following checks verify that the
main supply pressure is between 60 and 115 psi (4-8 bar)
at the Control Unit and, for X-Purge systems, the regulated
pressure on the logic gauge is 30 psi (2 bar)
4.2 Minimum
Pressure
Alarm is ON Continuously
(“Pressurized” Indicator is Red)
Possible cause 1:
The Pressurized Enclosure (PE)
pressure is too low. Try increasing the setting of the
Leakage Compensation Valve (LCV) to raise the pressure
in the PE.
Possible cause 2: Enclosure fault?
- Is the ACTUAL PE pressure below the setting of
the Minimum Pressure Sensor? Check it with a
manometer or gauge.
- Is there debris stuck on the face of the Relief Valve
disk, perhaps held there because of the magnetic
material?
- Has the PE door been closed and all conduit/cable
glands sealed?
- Is the PE leaking too much?
- Has the pressure sensing tube been damaged?
Possible cause 3: System fault?
If checks above reveal that the PE is correct, the fault
probably lies in the Control Unit. The basic operation of
the Minimum Pressure Sensor can be checked by
unscrewing the 2.4” (60mm) diameter diaphragm and,
by using a finger, block the threaded hole in the top of
the valve module. The valve should operate and the
indicator should turn Green. If this works correctly and
the enclosure pressure is above the setting of the
Minimum Pressure Sensor it is likely that the Pressure
Sensor diaphragm needs re-calibrating or replacing.
(See 4.6)
4.3 Relief Valve Opens (Continuously or
Intermittently)
Possible cause 1: The PE pressure is too high.
The Leakage Compensation Valve (LCV) is too far
open. Adjust the LCV as described in Section 2 above.
Possible cause 2: Debris on the RLV disk allowing air
to leak from the valve. Remove the RLV cover and
clean the valve disk. The disk and spring may be
removed from the RLV without affecting the calibration.
4.4
“Purging” Indicator Will Not Turn Yellow
During Purging