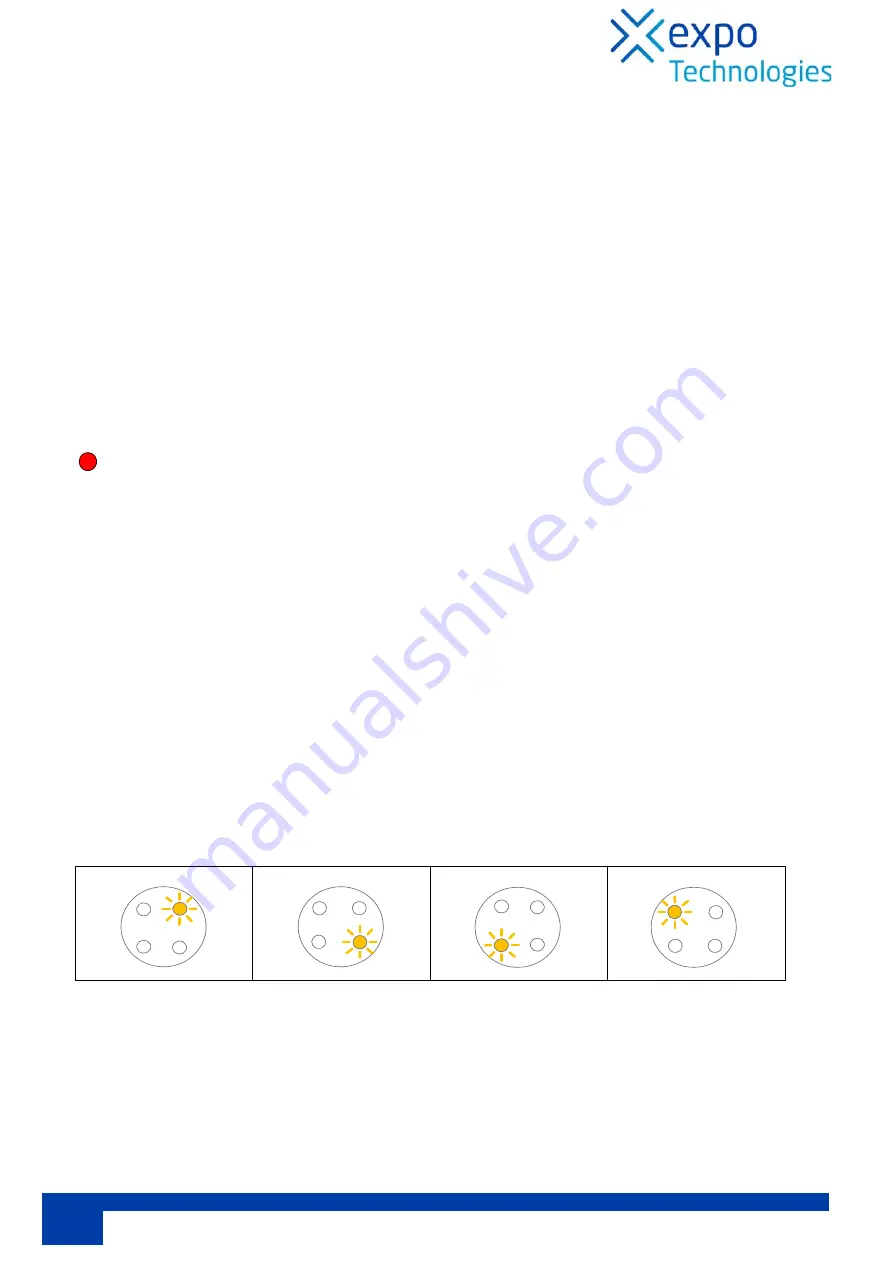
Page
7
ML434_ES | v11
Expo Technologies UK
T: +44 (0) 20 8398 8011
Expo Technologies US
T: +1 (440) 247 5314
Expo Technologies China
T: +86 532 8906 9858
Section 5: Main Components
Air Supply Filter / Regulator
The unit is provided with a 40
μ
m liquid / dust filter element as a precaution. The user of the MiniPurge
®
system
must ensure that air supply is to the quality stated in Air Supply Quality paragraph found in the Installation of
the System section. The regulator is factory set to 5 barg (73 psig) and regulates the pressure of an air supply
between 5 and 16 barg (73 to 232 psig). A pressure gauge is fitted down stream of the filter; this should
indicate no less than 5 barg (73 psig). During the purge cycle a pressure drop will be indicated on the gauge.
Logic Air Supply Regulator
This device provides the system with a stable air supply pressure to the logic system and allows consistent
operation. The pressure level is factory set to 2.5 barg (36 psig) and can be verified by means of the integral
pressure gauge.
Minimum Pressure Sensor
This monitors the pressure inside the pressurized enclosure. When the pressure is below the minimum required
for safe operation, the pressure sensor causes the system to reset and the Alarm / Pressurized indicator turns
Red
.
The sensor is factory calibrated and set to operate in falling pressure at or above the minimum
specified pressure.
Purge Flow Sensor
The Purge Flow Sensor monitors flow through the Purge Outlet Valve. At correct purge flow rates, above the
minimum specified for purging, the sensor sends a signal that activates the purge timer. This sensor is factory
calibrated to operate on falling flow rate at or above the minimum specified purge flow rate.
Intermediate Sensor
This sensor monitors the pressure inside the pressurized enclosure. It senses when the pressure is drops and
provides early warning before the low pressure sensor trips the system.
Electronic Purge Timer
When both the enclosure pressure and the purge flow rate are correct, the Purge Flow Sensor activates the
timer and the electronic timer starts. The timing period is selected using switches mounted on the timer
module.
Note: Setting the timer to 00 minutes will cause infinite purging; the cycle will never complete.
During timing, the percentage of the purge cycle is indicated by four LEDs which flashes sequentially while
the timer is running.
The Electronic Timer is powered by an EPPS (Electro-Pneumatic Power Supply.) Supply air must be available
for the EPPS to operate.
LED 1
LED 2
LED 3
LED 4
LED 1
LED 2
LED 3
LED 4
LED 1
LED 2
LED 3
LED 4
LED 1
LED 2
LED 3
LED 4
0 to 25%
of purge time
26 to 50%
of purge time
51 to 75%
of purge time
76 to 100%
of purge time