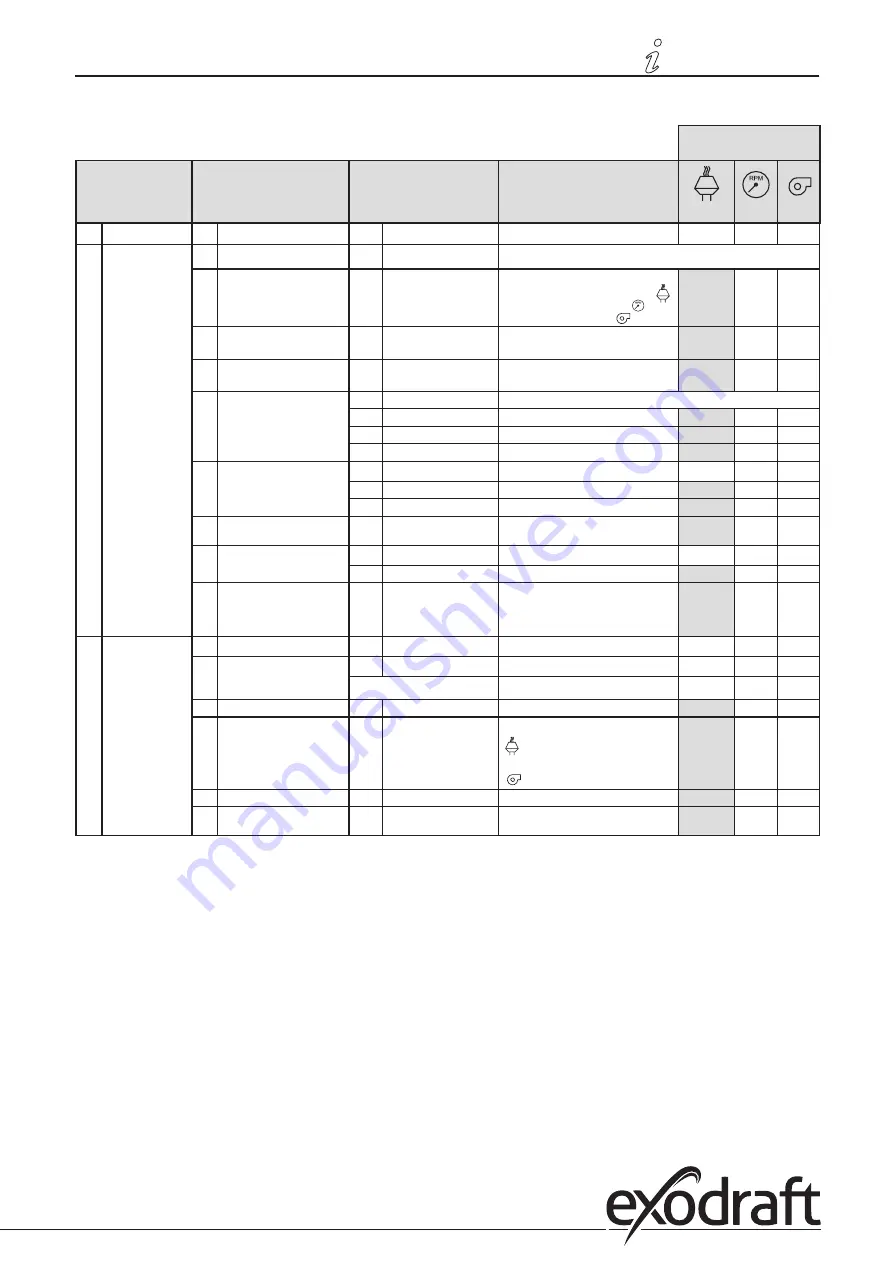
1.7.1
Overview of the service menu
The service menu is built up in four levels:
Base settings for the
three applications
Menu level 1
Menu level 2
Menu level 3
Function
Default
0
Exit Service menu
Return to operation screen
1
Operation settings
10
Exit operation settings
11
Operating mode
Setting of control/operating function
1 = Pressure-controlled regulation
2 = 2-stage speed regulation
3 = Supply air regulation
1
12
°C/°F
Select measuring unit for temperature
1 = °C, 2 = °F
1 (°C)
1 (°C)
1 (°C)
13
Pa/inWC
Measuring unit for pressure:
1 = Pa, 2 = inWC
1 (Pa)
1 (Pa)
1 (Pa)
14
Software versions
140
Exit
141
Controller version
View Controller software version
x.xx
x.xx
x.xx
142
Safety version
View Safety software version
x.xx
x.xx
x.xx
143
Display version
View Display software version
x.xx
x.xx
x.xx
15
Select XTP measurement
range
150
Exit
151
Set Low XTP value
from -500 Pa to 0 Pa
0 Pa
N/A
0 Pa
152
Set High XTP value
from 0 Pa to 500 Pa
150 Pa
N/A
150 Pa
16
Positive/negative pressure
1 = negative pressure
2 = positive pressure
1
N/A
1
17
OEM functions
170
Exit
171
Cooker function
Switch Cooker function ON and OFF
N/A
OFF
N/A
18
Reset to defaults
Reset to defaults. If you select “YES”, a
10-second countdown will start,
during which you can cancel your
choice by pressing any button.
NO
NO
NO
2
Alarm
20
Exit Alarm
21
Alarm Log
210
Exit
211-219
The 9 most recent alarms
22
Reset alarm log
Resets alarm log
NO
NO
NO
23
Flow Alarm limit
Set Flow Alarm limit in %:
50-80 %
(Alarm when pressure is below xx% )
100-300 %
(Alarm when pressure is above xx% )
64 %
N/A
300 %
24
Flow Alarm delay
Set Flow Alarm delay, 10–60 s
15 s
15 s
15 s
25
Reset auto / manual
1 = automatic, 2 = manual
1
(Auto)
1
(Auto)
1
(Auto)
3120049-EBC10-UK
Product information •
13
Product information •
13