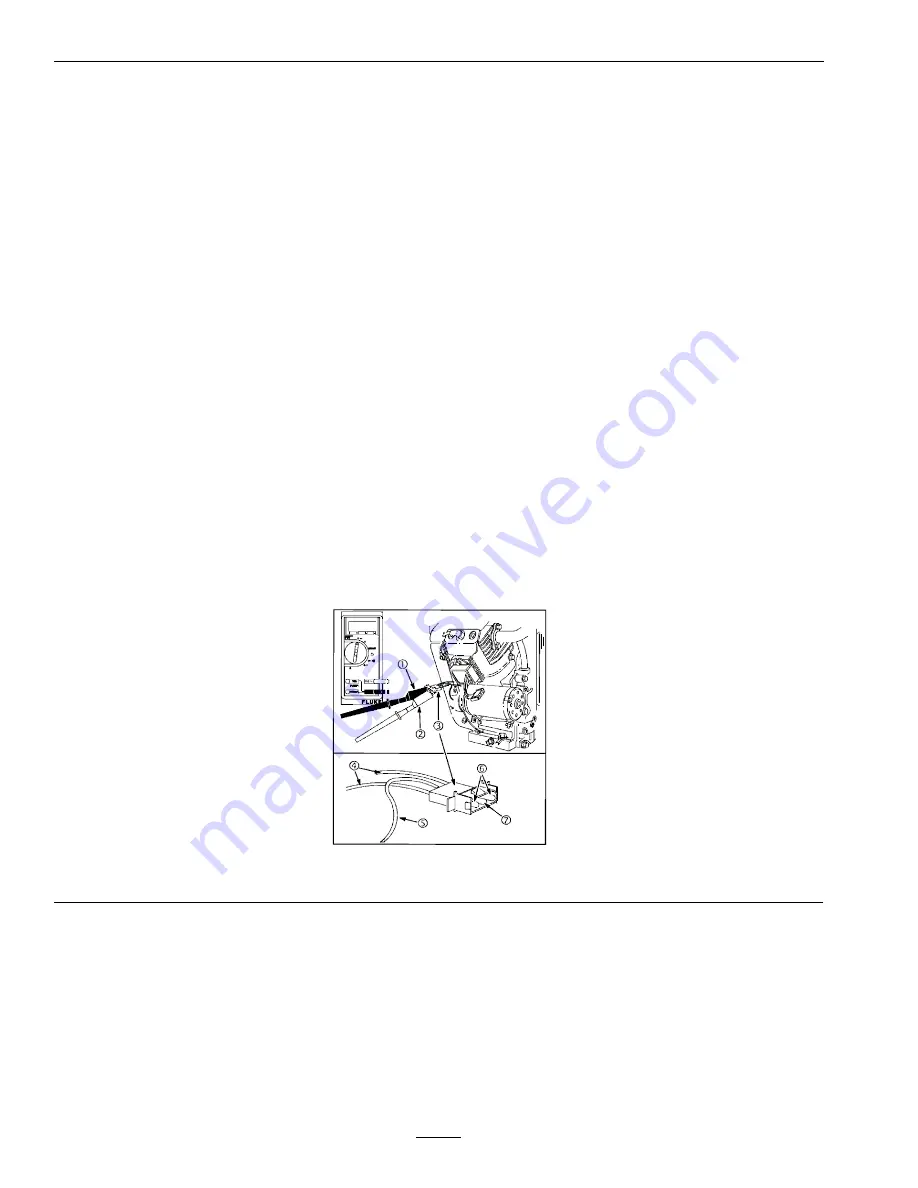
Troubleshooting
through the hopper door area, then Diffuser Guides are loose or worn allowing a gap between the door and
the hopper base. Also a potential factor is if the hopper cable is not completely closing the hopper door.
•
When your hopper door cannot open, there are typically 3 things to look at. One is that your hopper cable
may be frozen and locked up, the ball joint end may have broken off or there may be product jammed
between the hopper door and the base (due to loose door guides).
Charging Issues:
16 Amp Regulated Alternator
The 16 amp regulated alternator system provides AC current through two output leads to the regulator-rectifier.
The regulator-rectifier converts the AC current to DC, and regulates current to the battery. The charging
rate will vary with engine RPM and temperature.
1.
BLACK test lead from meter (1) (Figure 9)
2.
RED test lead from meter (2)
3.
Connector (3)
4.
Two YELLOW AC input leads (4)
5.
RED DC OUTPUT WIRE (5)
6.
AC Output terminals (6)
7.
RED DC output lead (7) to connector
Note:
Stator, regulator-rectifier and fly-wheel are NOT INTERCHANGEABLE with any other charging
system.
g268055
Figure 9
Output Test
WHEN CHECKING THE ALTERNATOR COMPONENTS, PERFORM THE TEST IN THE
FOLLOWING SEQUENCE:
Temporarily disconnect stator wire harness from regulator-rectifier.
1.
Insert RED test lead into VΩ receptacle in meter.
2.
Insert BLACK test lead into COM receptacle.
3.
Rotate selector to V~ (AC VOLTS) position.
24