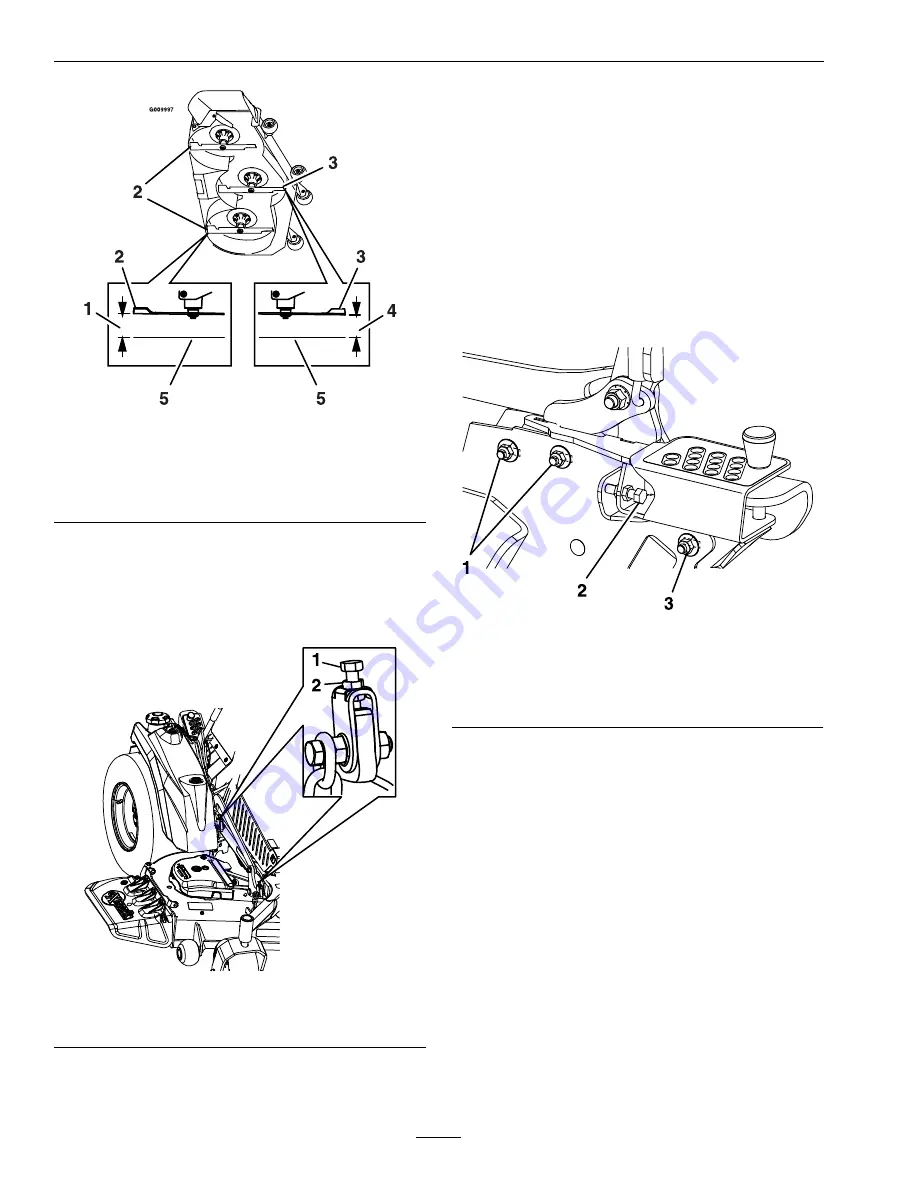
Maintenance
g009997
Figure 23
1.
3 1/4 inches (8.3 cm)
4.
3 inches (7.6 cm)
2.
Back blade tip
5.
Level surface
3.
Front blade tip
9.
Adjust the height — to increase, turn the
adjuster screw clockwise; to decrease, turn
counterclockwise. Fine tune the front deck lift
assembly by turning the adjuster screw until it
reaches the 3 inch (7.6 cm) height (see Figure 24).
g266564
Figure 24
1.
Adjuster screw
2.
Jam nut
10.
Measure the back tip height. Fine tune rear
adjusters as required; the single point adjustment
can be utilized to gain more adjustment. The
back tips of the side blades should measure 3 1/4
inches (8.3 cm).
11.
Re-measure until all four sides are the correct
height. Tighten all the nuts on the deck lift arm
assemblies.
12.
Lower the discharge deflector.
13.
If the four deck adjusters do not have enough
adjustment to achieve accurate cut height with the
desired rake, the single point adjustment can be
utilized to gain more adjustment (see Figure 25).
g266542
Figure 25
1.
Front height-of-cut plate mounting bolts
2.
Single point height adjustment bolt
3.
Rear height-of-cut plate mounting bolt
14.
To adjust the single point system, first loosen the
front and rear height-of-cut plate mounting bolts.
15.
If the deck is too low, tighten the single point
adjustment bolt by rotating it clockwise. If
the deck is too high, loosen the single point
adjustment bolt by rotating it counterclockwise.
Note:
Loosen or tighten the single point
adjustment bolt enough to move the height-of-cut
plate mounting bolts at least 1/3 the length of
the available travel in their slots. This will regain
some up and down adjustment on each of the
four deck links.
16.
Re-tighten front and rear height-of-cut plate
mounting bolts.
40
Summary of Contents for STARIS S Series
Page 1: ...STARIS S SERIES For Serial Nos 408 644 346 Higher Part No 4505 317 Rev A ...
Page 50: ...Schematics Schematics Electrical Schematic Kawasaki g303795 50 ...
Page 51: ...Schematics Electrical Schematic Kohler EFI g303794 51 ...
Page 52: ...Schematics Hydraulic Diagram g304191 52 ...
Page 54: ...Service Record Date Description of Work Done Service Done By 54 ...
Page 55: ...55 ...