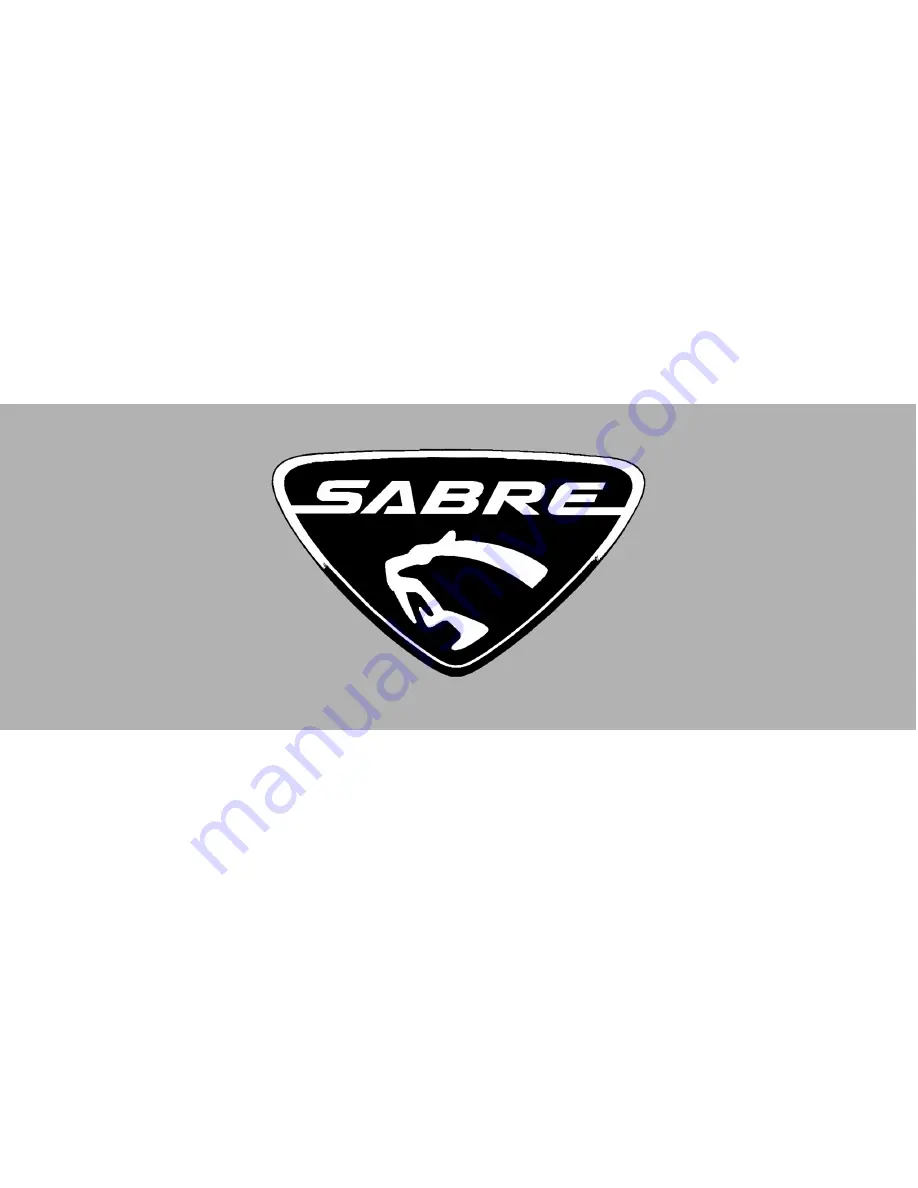
Sabre Lawn Tractor
38–Inch and 46–Inch (96 cm and 117 cm)
Models: 1338 Gear
John Deere Consumer Products Group
TM–GX10131 (Mar–97)
LITHO IN U.S.A. (New)
1538 Hydro
15538 Gear
1646 Hydro
1538 Gear
1638 Hydro
1646 Gear
Technical Manual
15538 Hydro
1546 Gear
www.servicemanualall.com
Buy, Download, Print...
www.servicemanualall.com
Summary of Contents for 1338 Gear
Page 7: ...SAFETY 1 6 3 5 97 www servicemanualall com...
Page 19: ...CONTENTS CONTINUED ENGINE 3 2 2 11 97 Page www servicemanualall com...
Page 25: ...CONTENTS CONTINUED ELECTRICAL 4 2 2 11 97 Page www servicemanualall com...
Page 53: ...GEAR POWER TRAIN CONTENTS CONTINUED 5 2 3 5 97 www servicemanualall com...
Page 65: ...GEAR POWER TRAIN 5 14 2 12 97 1 2 4 5 10 11 2 2 8 7 9 www servicemanualall com...
Page 112: ...DIAGNOSIS HYDROSTATIC POWER TRAIN 2 12 97 6 27 1 2 3 4 6 5 www servicemanualall com...
Page 114: ...DIAGNOSIS HYDROSTATIC POWER TRAIN 2 12 97 6 29 1 2 3 4 5 6 www servicemanualall com...
Page 147: ...NOTES STEERING 7 2 2 11 97 www servicemanualall com...
Page 153: ...NOTES ATTACHMENTS 8 2 2 14 97 www servicemanualall com...
Page 158: ...COMPONENT LOCATION ATTACHMENTS 3 5 97 8 7 www servicemanualall com...
Page 169: ...NOTES MISCELLANEOUS 9 2 3 5 97 www servicemanualall com...
Page 177: ...CONTENTS CONTINUED Service Information Bulletins 9 2 3 5 97 Page S www servicemanualall com...
Page 187: ...SERVICE INFORMATION BULLETINS 10 12 3 5 97 S www servicemanualall com...