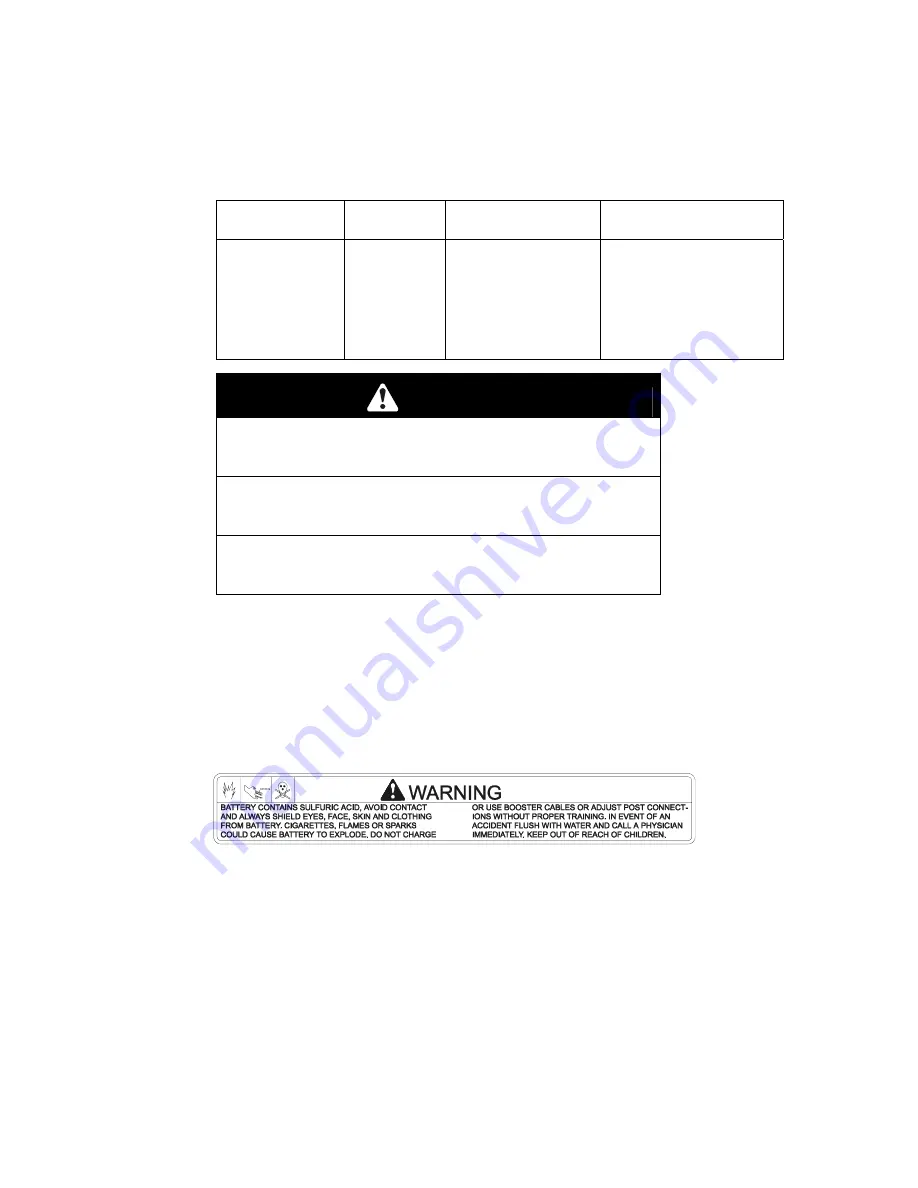
- 13 -
3.2.1
Check the voltage of the battery with a digital voltmeter. Locate the voltage reading
of the battery in the table below and charge the battery for the recommended time
interval to bring the charge up to a full charge of 12.6 volts or greater.
IMPORTANT:
Make sure the negative battery cables are disconnected and the
battery charger used for charging the battery has an output of 16 volts and 7
amps or less to avoid damaging the battery (see the following chart for
recommended charger settings).
Voltage
Reading
Percent
Charge
Maximum
Charger Settings
Charging Interval
12.6 or greater 100%
16 volts/7 amps
No Charging Required
12.4 – 12.6
75 – 100%
16 volts/7 amps
30 Minutes
12.2 – 12.4
50 – 75%
16 volts/7 amps
1 Hour
12.0 – 12.2
25 – 50%
14.4 volts/4 amps
2 Hours
11.7 – 12.0
0 – 25%
14.4 volts/4 amps
3 Hours
11.7 or less
0%
14.4 volts/2 amps
6 Hours or More
CAUTION
POTENTIAL HAZARD
♦
If the ignition is in the “ON” position there is potential
for sparks and engagement of components.
WHAT CAN HAPPEN
♦
Sparks could cause an explosion or moving parts
could accidentally engage causing personal injury.
HOW TO AVOID THE HAZARD
♦
Be sure ignition switch is in the “OFF” position before
charging the battery.
3.2.4
Connect the negative battery cables.
NOTE:
If the positive cable is also disconnected, connect the
positive (red)
cable and the red wire
to the positive terminal on the battery
first
,
then connect
the negative (black) cable and black wire to the negative terminal on the battery.
Slip insulator boot over the positive terminal.
NOTE:
If time does not permit charging the battery, or if charging equipment is
not available, connect the negative battery cables and run the vehicle
continuously for 20 to 30 minutes to sufficiently charge the battery.
3.3 INSTALL DRIVE WHEELS.
3.3.1
Mount drive wheels with the valve stem to the outside of the unit. Secure using
four (4) ½-20 wheel nuts installed on studs in hubs for each wheel. Torque to
95 ft-lbs (128 N-m).
3.4 CHECK TIRE PRESSURE.
3.4.1
Check tire pressure in drive tires. Proper inflation pressure for tires is 15 psi
(103 kPa). Adjust if necessary.
Mower deck casters and rear caster tires are semi-pneumatic and
do not need to
be inflated.
3.5 SERVICE ENGINE.
Engine is shipped with oil; check oil level and if necessary and fill to the appropriate
level with oil as specified in Engine Owner’s Manual.
Summary of Contents for Navigator NAV20KC
Page 1: ...Part No 103 8573 Rev B For Serial Nos 510 000 Higher ...
Page 44: ... 39 8 ELECTRICAL DIAGRAM ...
Page 45: ... 40 9 HYDRAULIC DIAGRAM ...
Page 47: ...42 ...