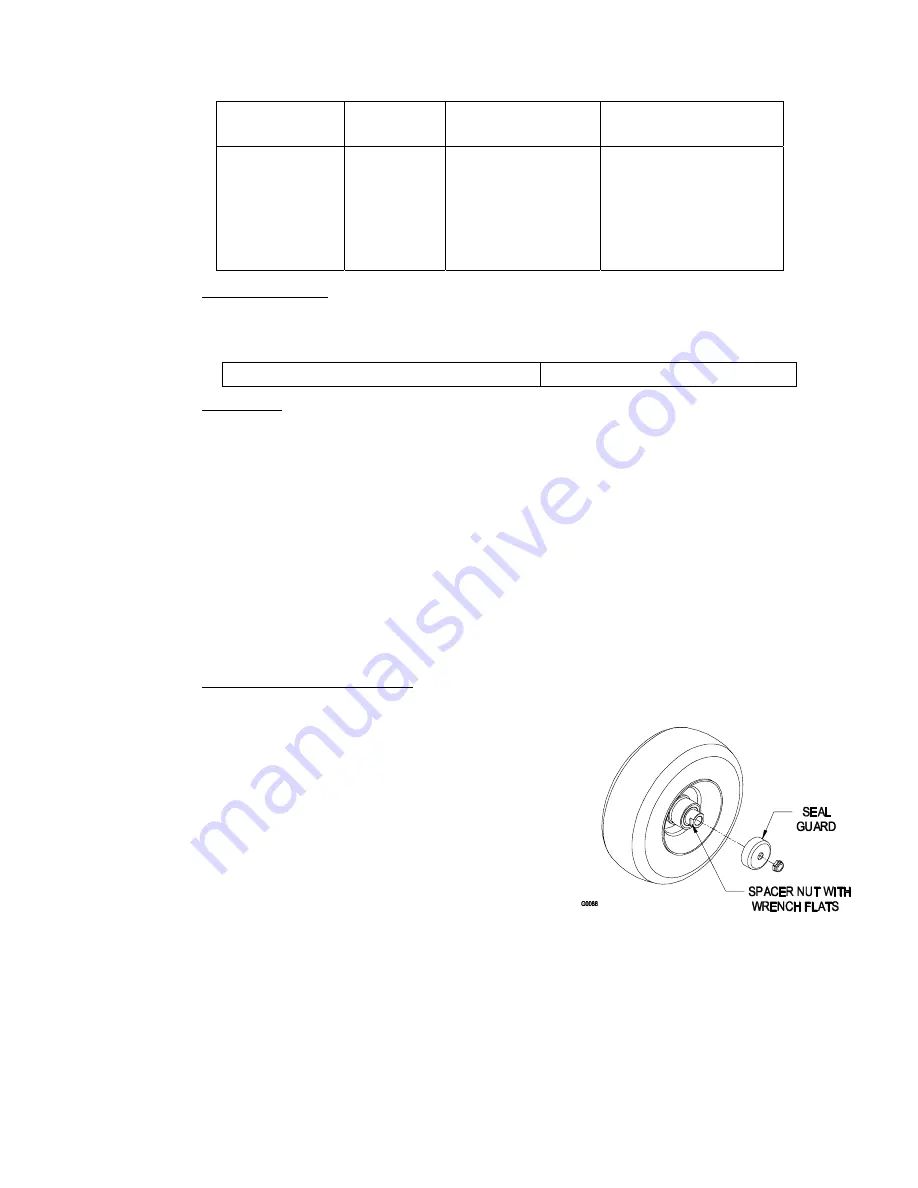
31
and 7 amps or less to avoid damaging the battery (see chart below for
recommended charger settings).
Voltage
Reading
Percent
Charge
Maximum
Charger Settings
Charging Interval
12.6 or greater 100%
16 volts/7 amps
No Charging Required
12.4 – 12.6
75 – 100%
16 volts/7 amps
30 Minutes
12.2 – 12.4
50 – 75%
16 volts/7 amps
1 Hour
12.0 – 12.2
25 – 50%
14.4 volts/4 amps
2 Hours
11.7 – 12.0
0 – 25%
14.4 volts/4 amps
3 Hours
11.7 or less
0%
14.4 volts/2 amps
6 Hours or More
4.1.21 Change fuel filter:
Service Interval: 400 hrs.
a)
A fuel filter is installed between the fuel tank and the fuel pump. Replace
when necessary
Replacement Filters
Kubota
P/N 12581-43012
4.1.22 Wheel hub - slotted nut torque specification.
Service Interval: 500 hrs
When tightening the slotted nut on the wheel motor tapered shaft:
a)
Torque the slotted nut to 125 ft. lbs (169 N-M).
b)
Check distance from bottom of slot in nut to inside edge of hole. Two
threads (0.1”) or less should be showing.
c)
If more than two threads (0.1”) are showing remove nut and install washer
(PN 1-523157) between hub and nut.
d)
Torque the slotted nut to 125 ft. lbs (169 N-m).
e)
Then tighten nut until the next set of slots line up with the cross hole in shaft.
f)
Replace cotter pin.
NOTE: Do not use antiseize on wheel hub.
4.1.23 Lubricate caster wheel hubs:
Service Interval: Once Yearly
a)
Stop engine, wait for all moving parts to
stop, and remove key. Engage parking
brake.
b)
Remove caster wheel from caster forks.
c)
Remove seal guards from the wheel hub.
d)
Remove one of the spacer nuts from the
axle assembly in the caster wheel. Note
that thread locking adhesive has been
applied to lock the spacer nuts to the
axle. Remove the axle (with the other
spacer nut still assembled to it) from the
wheel assembly.
e)
Pry out seals, and inspect bearings for
wear or damage and replace if necessary.
f)
Pack the bearings with a NGLI grade #1 multi-purpose grease.
g)
Insert (1) bearing, (1) new seal into the wheel.
NOTE
: Seals (Exmark PN 103-0063) must be replaced.
h)
If the axle assembly has had both spacer nuts removed (or broken loose),
apply a thread locking adhesive to (1) spacer nut and thread onto the axle
FIGURE 4
For Exmark Mower Parts Call 606-678-9623 or 606-561-4983
www.mymowerparts.com