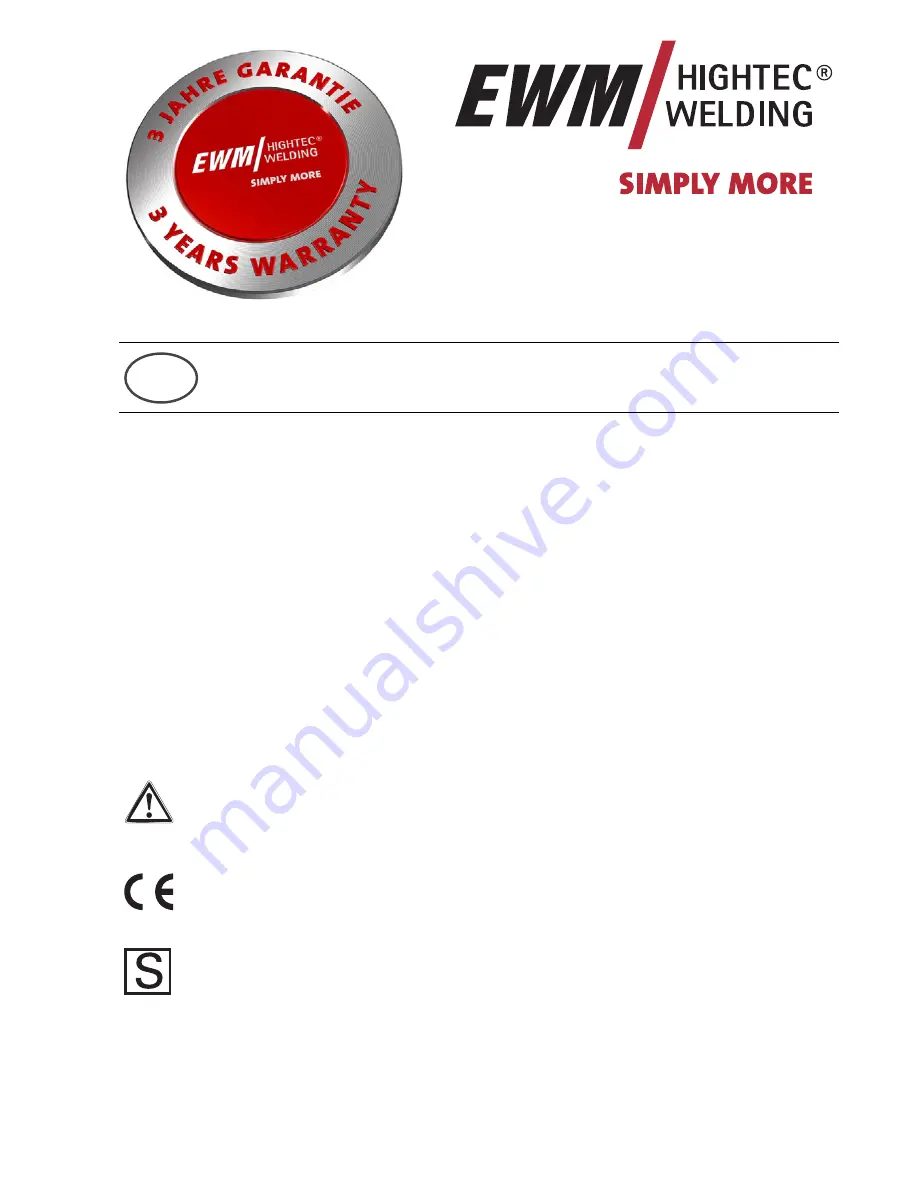
EWM
HIGHTEC WELDING GmbH
Dr. Günter-Henle-Straße 8 • D-56271 Mündersbach
Fon +49 2680 181-0 • Fax +49 2680 181-244
www.ewm.de
•
GB
Operating instructions
Machines for MIG/MAG welding
WEGA 351, 401, 451, 501, 601
WEGA DRIVE 41, 41L
N. B. These operating instructions must be read before commissioning.
Failure to do so may be dangerous.
Machines may only be operated by personnel who are familiar with the appropriate safety
regulations.
The machines bear the conformity mark and thus comply with the
• EC Low Voltage Directive (2006/95/ EG)
• EC EMC Directive (2004/108/ EG)
In compliance with IEC 60974, EN 60974, VDE 0544 the machines can be used in environments
with an increased electrical hazard.
©
The content of the operating instructions does not constitute grounds for any claims on the part
of the buyer.
The copyright to these operating instructions remains with the manufacturer.
Reprinting, including extracts, only with written approval.
© 2009 Subject to alteration.
Item No.: 099-004934-EWM01
Revised: 21.07.2009