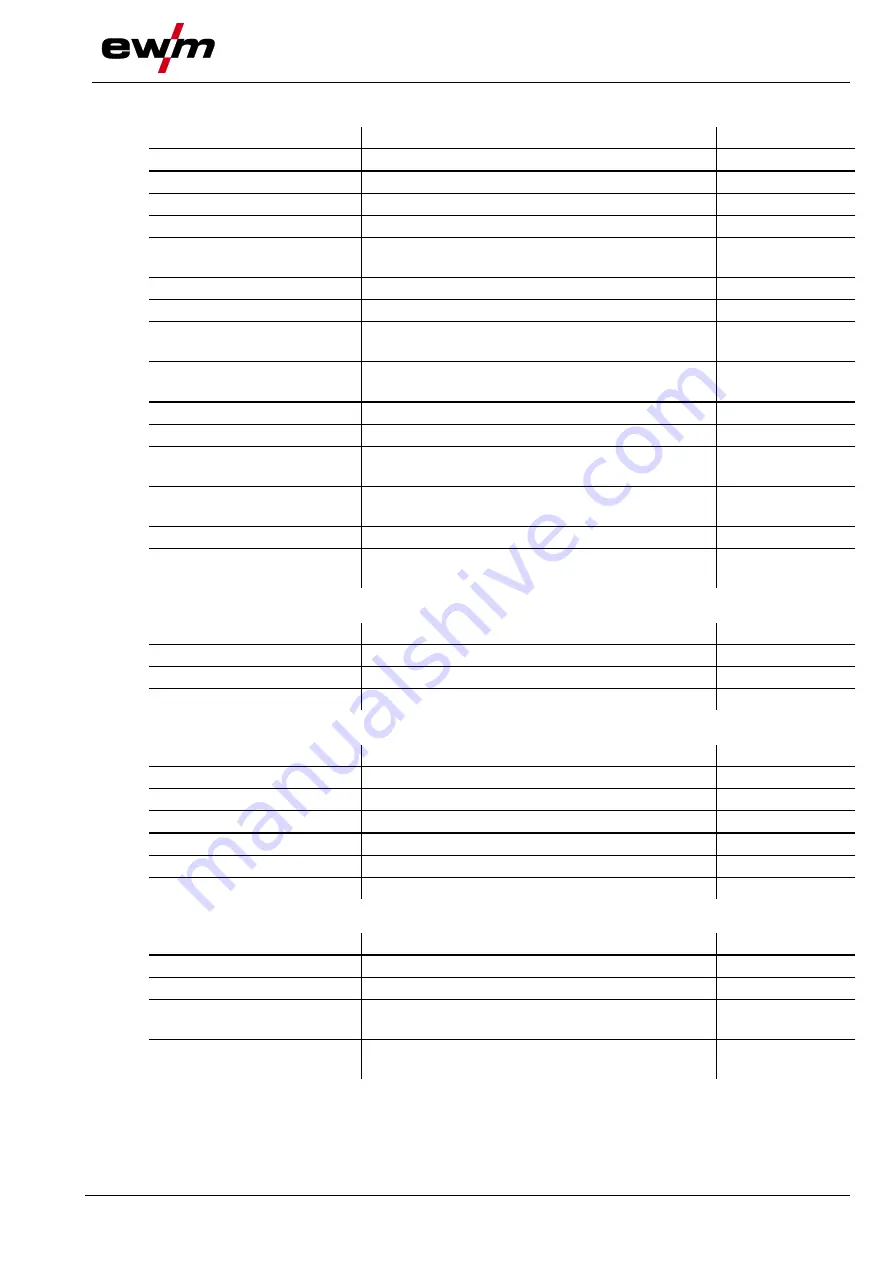
Accessories
Options
099-005670-EW501
7.03.2022
63
9.3 Options
Type
Designation
Item no.
ON Filter F06
Dirt filter for air inlet
092-003337-00000
ON Shock Protect F06
Ram protection
092-003334-00000
ON TS F06 R
Torch holder, right
092-003335-00000
ON TS F06 L
Torch holder, left
092-003360-00000
ON HS F06
Holder for holding long hose packages and welding
torch
092-003333-00000
ON CS F.06
Crane frame
092-003485-00000
ON CC F.06
Transparent cover cap for protection of control
092-004198-00000
ON PDM TG.11 Comfort 3.0 Transparent protective screen for device control
Comfort 3.0
092-004279-00000
ON PDM TG.11 Expert 3.0
Transparent protective screen for device control Ex-
pert 3.0
092-004278-00000
OU F06W
Conversion kit, water block
092-003492-00000
OU F06WRF
Conversion kit, water block with reinforced pump
092-003493-00000
OU F06R1/R2
Conversion kit, single cylinder holder to double cy-
linder holder
092-003494-00000
OU AIF F06
Conversion kit, 19-pole interface for automated
welding
092-004415-00000
ON Water Filter K.06
Optional water filter
092-004051-00000
ON RPH TIG F.06
Holder for TIG welding rods for mounting on flexFit
casing system
092-004388-00000
9.4 General accessories
Type
Designation
Item no.
32A 5POLE/CEE
Machine plug
094-000207-00000
KLF-L1-L2-L3-PE
Label of mains cable
094-023697-00000
ON AL D13/27
Cap for load sockets
092-003282-00000
9.5 Shielding gas supply (shielding gas cylinder for welding machine)
Type
Designation
Item no.
Mod. 842 Ar/CO2 230bar 15l Pressure regulator with manometer
394-002910-00015
DM 842 Ar/CO2 230bar 30l D Pressure regulator with manometer
394-002910-00030
GH 2X1/4'' 2M
Gas hose
094-000010-00001
G1 G1/4 R 3M
Gas hose
094-000010-00003
GH 2X1/4'' 5m
Gas hose
094-000010-00005
GH 2X1/4'' 10 m
Gas hose
094-000010-00011
9.6 Networking / Xnet
Type
Designation
Item no.
Xnet LAN Gateway
LAN gateway in external casing
090-008833-00502
Xnet WiFi Gateway
WiFi gateway in external casing
090-008834-00502
Xnet Extended-Set LAN
Xnet retrofit set LAN: One machine licence, a LAN
gateway and a network cable (10 m)
091-008833-00001
Xnet Extended-Set WiFi
Xnet retrofit set WiFi: One machine licence, one
WiFi gateway, one 7-pole connection cable (5 m)
091-008834-00001