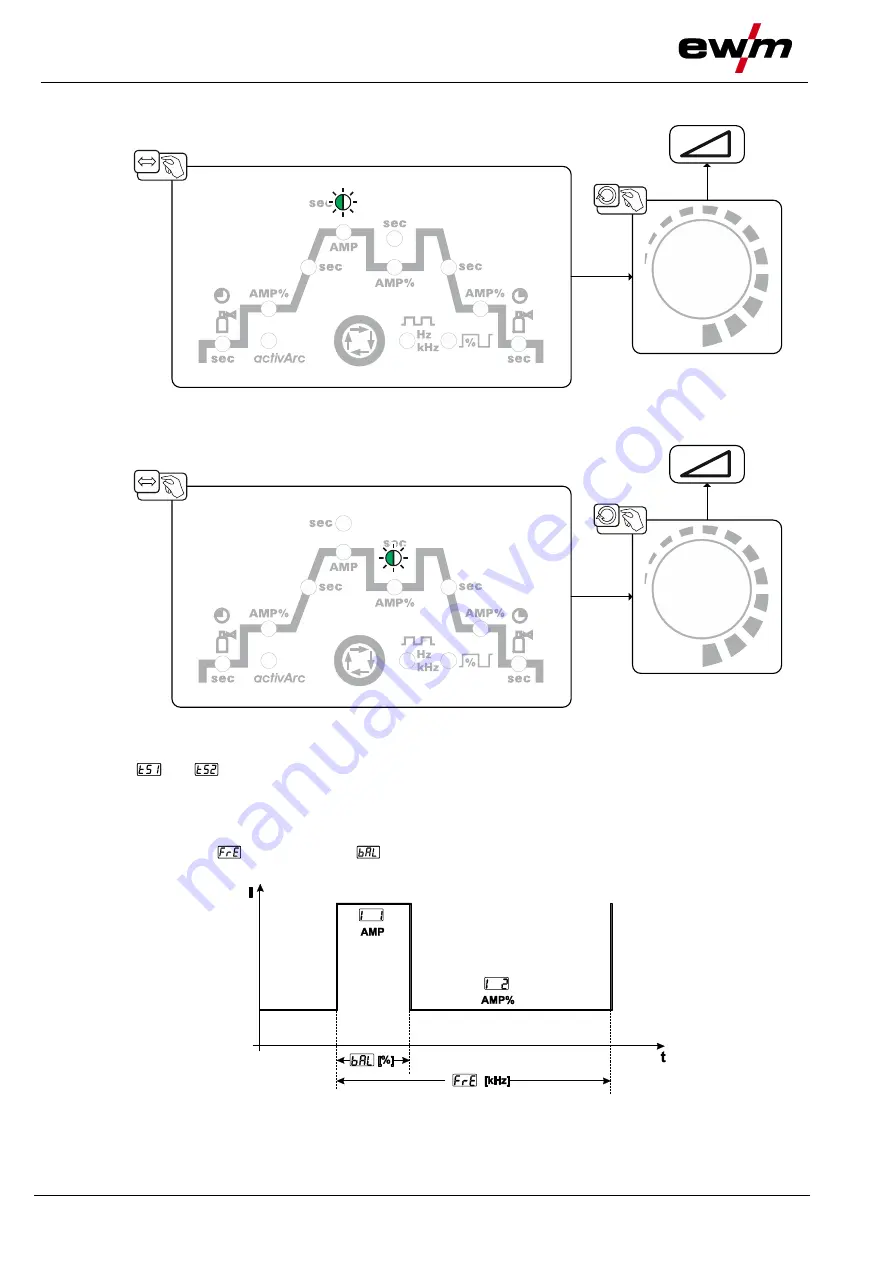
Design and function
TIG welding
62
099-000118-EW501
24.11.2017
Pulse time setting
Figure 5-44
Pulse pause setting
Figure 5-45
Pulse edge setting
The
and
pulse edges can be set in the Expert menu (TIG)
> see 5.9.16 chapter
.
5.9.13.3 Metallurgical pulsing (kHz pulsing)
Metallurgical pulsing (kHz pulsing) uses the plasma force (arc force) occurring at high currents which
allows you to achieve a constricted arc with concentrated heat input. Unlike thermal pulsing, no times are
set; a frequency
and the balance
are set instead. The pulsing process also occurs during the up-
slope and down-slope phase.
Figure 5-46