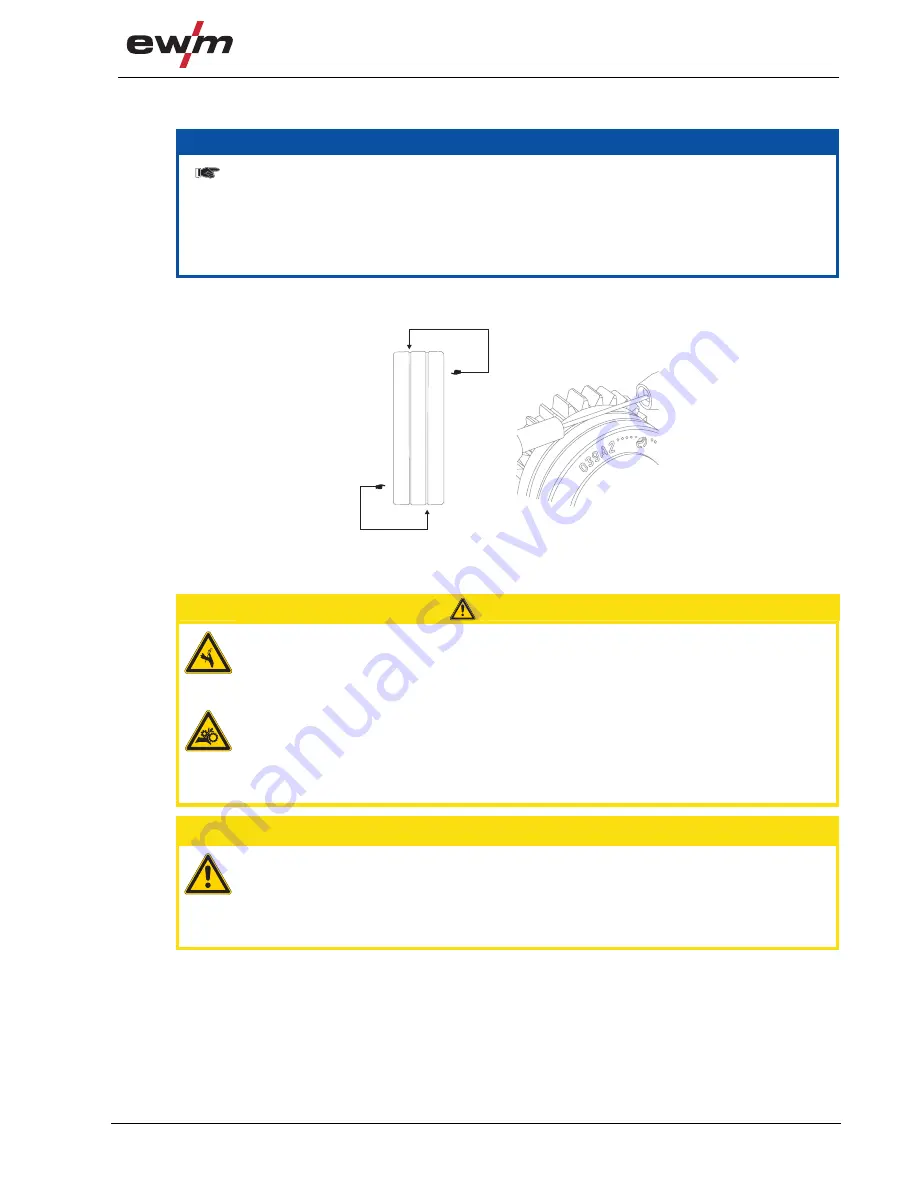
Design and function
MIG/MAG welding
099-005215-EW501
29.06.2011
33
5.7.3
Changing the wire feed rollers
NOTE
Unsatisfactory welding results due to faulty wire feeding!
Wire feed rollers must be suitable for the diameter of the wire and the material.
• Check the roller label to verify that the rollers are suitable for the wire diameter.
Turn or change if necessary!
• use V-groove rollers with for steel wires and other hard wires,
• use U-groove rollers for aluminium wires and other soft, alloyed wires.
• Slide new drive rollers into place so that the diameter of the wire used is visible on the drive roller.
• Screw the drive rollers in place with knurled screws.
Figure 5-7
5.7.4
Inching the wire electrode
CAUTION
Risk of injury due to welding wire escaping from the welding torch!
The welding wire can escape from the welding torch at high speed and cause bodily
injury including injuries to the face and eyes!
• Never direct the welding torch towards your own body or towards other persons!
Risk of injury due to moving parts!
The wire feed units are equipped with moving parts, which can trap hands, hair,
clothing or tools and thus injure persons!
• Do not reach into rotating or moving parts or drive components!
• Keep casing covers closed during operation!
CAUTION
Extensive wear due to incorrect contact pressure!
Incorrect contact pressure will cause extensive wear of the wire feed rollers!
• With the adjusting nuts of the pressure units set the contact pressure so that the wire
electrode is conveyed but will still slip through if the wire spool jams.
• Set the contact pressure of the front rollers (in wire feed direction) to a higher value!